Принципы построения системы Toyota. Информационная система "канбан"
Выбери формат для чтения
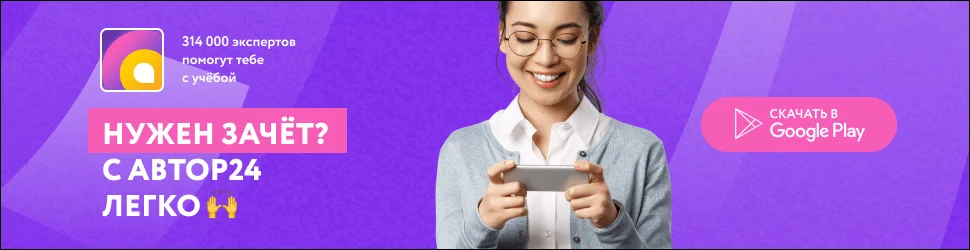
Загружаем конспект в формате pdf
Это займет всего пару минут! А пока ты можешь прочитать работу в формате Word 👇
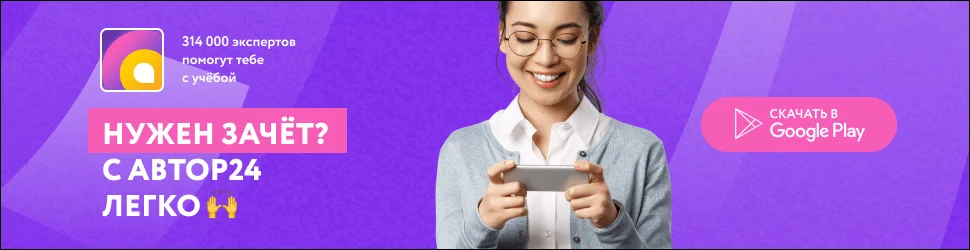
Лекция 19. Принципы построения системы Toyota. Информационная система
«канбан».
В данной теме рассматриваются вопросы построения системы Toyota, а также
информационной системы «канбан».
Система Toyota – это комплексная система управления предприятием (рисунок 1),
затрагивающая
практически
все
аспекты
производственного
(операционного)
менеджмента, которая предусматривает:
− ликвидацию всех ненужных элементов производственного процесса в целях
сокращения издержек производства;
− сокращение длительности производственного цикла, размера запасов и заделов
незавершенного производства;
− гибкое реагирование на колебания спроса на продукцию;
− обеспечение качества на всех стадиях производства;
− активизацию «человеческого фактора».
Рисунок 1 – Важнейшие составные части системы Тойота
Японская народная мудрость гласит:
а) богатеет не тот, кто много зарабатывает, а тот, кто мало платит;
б) упрощение – самый надежный путь к совершенству;
в) качество – вот единственная вновь созданная стоимость, все остальное –
издержки.
1
Система Toyota в полной мере воплотила эту мудрость. Ее цели можно представить
в виде следующей схемы: Снижение затрат на производство> Снижение нормы прибыли>
Снижение цены на продукцию> Завоевание рынков сбыта> Рост объема продаж>
Расширение масштаба производства> Рост массы прибыли.
Рассмотрим подробнее методы достижения поставленных целей, используемые в
системе Toyota.
Информационная система «канбан»
«Канбан»
–
это
информационная
система,
обеспечивающая
оперативное
управление на всех стадиях производственного процесса и основанная на жестком
выполнении правил движения карточек четырех видов. «Канбан» реализует механизм
«вытягивания» продукции из предыдущего производственного звена на основе системы
горизонтальных связей.
Средством передачи информации в технологической цепи служат специальные
карточки на бумажных, пластиковых (прикрепляемых к контейнеру), цифровых или иных
носителях информации. Различают карточки заказа (производственные) и отбора
(транспортные). Карточки отбора несут информацию о том, сколько и каких предметов
нужно забрать со склада и доставить к месту потребления, карточки заказа – сколько и
чего нужно изготовить в месте производства и доставить на склад. В свою очередь,
карточки заказа и отбора бывают двух видов:
− карточки заказа, предназначенные для использования при изготовлении изделий
мелкими и крупными партиями;
− карточки отбора внутренние (межоперационные и т. д.) и внешние (карточки
поставщика, перевозчика и т. п.).
Виды используемых при этом карточек показаны на рисунке 2.
Рисунок 2 – Виды карточек «канбан»
2
Для выполнения своих функций внутренние карточки отбора и карточки заказа
имеют следующие реквизиты:
1) обозначение типоразмера детали или сборочной единицы;
2) номер производящего их участка или линии;
3) номер потребляющего их участка или линии (этот реквизит у карточек заказа
отсутствует);
4) тип и вместимость тары в потоке деталей (сборочных единиц) данного
типоразмера;
5) номер склада, где хранятся данные детали или сборочные единицы;
6) номера и расположение стеллажа и позиций для хранения;
7) номер карточки;
8) общее количество карточек в обороте.
Сигнальные карточки имеют дополнительные реквизиты: точку заказа и размер
партии поставки. Эти карточки имеют треугольную форму и навешиваются на контейнер
с мелкими деталями широкого использования (т. е. унифицированными деталями) на
уровне точки заказа. Карточки поставщика содержат дополнительные реквизиты,
указывающие на способ и периодичность доставки комплектующих изделий от фирмпроизводителей на головное предприятие.
На фирме Toyota для внешних поставщиков обычно принят интервал доставки,
равный четырем часам, тогда как внутри автосборочного завода интервал планирования
составляет всего два часа. Информационные системы, аналогичные «канбан», существуют
в любой организации. Они определяют формы и правила обращения документов,
сопровождающих движение материальных потоков в производстве.
Однако информационная система «канбан» – принципиально новый шаг в этом
направлении. Ее новизна определяется не столько формой и реквизитами карточек,
сколько выполняемыми функциями и правилами обращения, вытекающими из них. Кроме
того, новизна системы не имела бы смысла, если бы правила не выполнялись. Правила
движения карточек «канбан»:
1. Любое перемещение изделий без карточек запрещено;
2. Для
перемещения
используются
только
стандартные
контейнеры
фиксированной емкости;
3. Бракованная продукция не должна поступать на следующую операцию
(находиться в контейнере);
4. На каждый контейнер приходится только одна карточка заказа и одна карточка
отбора;
3
5. Любой отбор, превышающий указанное в карточке количество, запрещен;
6. Производство в больших количествах, чем указано в карточке, запрещено;
7. Число карточек, находящихся в обороте, должно быть минимальным;
8. Различные типоразмеры изделий производятся в последовательности, заданной
порядком поступления карточек заказа на участок.
В простейшем случае механизм «вытягивания» предметов обработки с помощью
карточек «канбан» реализуется следующим образом (рисунок 3).
Рисунок 3 – Схема движения материального потока изделий и оборота
сопровождающих их карточек в системе JIT
Пусть в технологической цепи произвольно выделена некоторая связанная пара
«поставляющее звено – потребляющее звено», которые взаимодействуют между собой
4
только через назначенный им буфер (склад, накопитель, зону хранения). Буфер
предназначен для хранения оборотного и, если нужно, страхового задела предметов труда
в контейнерах, а также для накопления пустых контейнеров. Каждый контейнер несет
одну прикрепленную к нему карточку:
− карточку отбора – при движении от буфера к потребляющему звену, когда он
заполнен, и от потребляющего звена к буферу, когда он пуст;
− карточку заказа – при движении от буфера к поставляющей позиции, когда он
пуст, и от поставляющей позиции к буферу, когда он полон.
Смена на контейнере карточки заказа на карточку отбора, относящихся к одному
типоразмеру деталей, может происходить только в буфере, где циклы оборота карточек
пересекаются. Смена карточки на такую же, но относящуюся к другому типоразмеру
деталей, может происходить только на потребляющей и поставляющей позициях через
картотеки 1 и 2 соответственно.
Работа механизма «вытягивания» включает три фазы:
1) потребляющее звено, получив заказ от последующего по ходу технологического
процесса звена, определяет свою потребность в деталях, необходимых для выполнения
данного заказа. Из картотеки 1 выбираются соответствующие карточки отбора (одна или
несколько), которые по мере освобождения контейнеров по одной прикрепляются к ним и
транспортируются в буфер;
2) в буфере на основании информации карточек отбора выбираются контейнеры,
заполненные требуемыми деталями. С них снимаются карточки заказа и прикрепляются
на поступившие пустые контейнеры, с которых, в свою очередь, карточки отбора
перемещаются на отобранные заполненные контейнеры.
Таким образом, на каждом отобранном контейнере с деталями карточка заказа
заменяется на карточку отбора, на таком же количестве пустых контейнеров карточки
отбора заменяются на карточки заказа. Заполненные контейнеры с карточками отбора
отправляются
к
месту потребления.
Пустые
контейнеры
с
карточками
заказа
отправляются к месту производства;
3)
поставляющее звено, получив из буфера пустые контейнеры с карточками
заказа, планирует свою потребность в материалах и размещает соответствующие заказы в
предыдущих (по ходу технологического процесса) звеньях. Поступившие с пустыми
контейнерами карточки заказа служат основанием для запуска в производство именно
таких и именно в таком количестве предметов труда, чтобы восполнить ими
уменьшившийся запас в буфере. Если поставляющее звено еще занято выполнением предыдущих заказов, вновь прибывшие карточки ставятся в конец очереди на выполнение (в
5
картотеку 2). Когда заказ выполнен и контейнеры заполнены, они с прикрепленными
карточками заказа отправляются в буфер, где запас восполняется до прежнего уровня.
Приведенная схема движения материального потока показывает, как бы одну «плоскость»
процесса, обеспечивающую «вытягивание» и производство одного типоразмера деталей.
Гибкость системы, т. е. быстрый переход в другую «плоскость» или к другому
типоразмеру, поддерживается картотекой 1. А именно, когда контейнер с заготовками
оказывается порожним, в картотеке выбирается карточка отбора со склада заготовок того
типоразмера, который заказан этой линии следующим за ней производственным
подразделением (например, сборочным конвейером). После чего действует та же схема,
но применительно к другому типоразмеру деталей.
При возникновении дефицита на складе в оборот запускаются срочные карточки с
одной красной полосой, проходящие картотеку 2 вне очереди, или аварийные с двумя
красными полосами, требующие снятия с линии очередной партии и запуска аварийной
партии. Общее число карточек, находящихся в обороте, призвано точно и адекватно
отражать объем незавершенного производства.
Действительно, так как межлинейная транспортировка и хранение на складе
предметов труда разрешено только в стандартных контейнерах, а на каждый контейнер
приходится по одной карточке каждого вида, то количества контейнеров и карточек
каждого вида равны. Контроль числа карточек позволяет контролировать незавершенное
производство. Стремление к его минимизации приводит к правилу минимального числа
карточек, находящихся в обороте. Необходимое число карточек для некоторого изделия
можно рассчитать, пользуясь методами теории управления запасами.
Например, следующим образом: Z=DT (1+K)/Q, где Z – общее число карточек
(контейнеров), находящихся в обороте;
D – среднедневное потребление предметов труда, шт.;
Т – ожидаемое время пополнения запаса, дн.;
Q – емкость контейнера, шт.;
К – коэффициент страхового запаса.
Пути минимизации заделов показаны на рисунке 4.
6
Рисунок 4 – Пути минимизации запасов и заделов незавершённого производства в
системе JIT
7