Основы технологии производства и ремонта подвижного состава
Выбери формат для чтения
Загружаем конспект в формате pdf
Это займет всего пару минут! А пока ты можешь прочитать работу в формате Word 👇
Министерство транспорта Российской Федерации
Федеральное агентство железнодорожного транспорта
Федеральное государственное бюджетное
образовательное учреждение высшего образования
«Дальневосточный государственный
университет путей сообщения»
Кафедра «Транспорт железных дорог»
ПРОИЗВОДСТВО И РЕМОНТ
ПОДВИЖНОГО СОСТАВА
Основы технологии производства
и ремонта подвижного состава
Рекомендовано
методическим советом по качеству
образовательной деятельности ДВГУПС
в качестве учебного пособия
Составители: Е.Н. Кузьмичев, Д.Н. Никитин
2-е издание, исправленное и дополненное
Хабаровск
Издательство ДВГУПС
2019
УДК 629.44 (075.8)
ББК О 22я73
П 80
Рецензенты:
Кафедра «Электропоезда и локомотивы»
Иркутского государственного университета путей сообщения
(доктор технических наук, профессор А.Н. Савоськин)
Начальник отдела планирования ремонта локомотивов
Дальневосточной дирекции тяги – структурного подразделения
Дирекции тяги – филиала ОАО «РЖД»
Р.Л. Титов
Составители: Е.Н. Кузьмичев, Д.Н. Никитин
П 80
Производство и ремонт подвижного состава. Основы технологии
производства и ремонта подвижного состава : учеб. пособие
/ сост. Е.Н. Кузьмичев, Д.Н. Никитин. – 2-е изд., испр. и доп. – Хабаровск : Изд-во ДВГУПС, 2019. – 146 с.
Учебное пособие соответствует учебным программам дисциплин «Подвижной состав железных дорог», «Электрический транспорт железных дорог», «Вагоны».
Подробно изложен материал по таким вопросам, как: характеристики
производственного и технологического процессов, их проектирование; восстановление деталей; основные положения по техническому обслуживания
и ремонту подвижного состава; основы технологий ремонта сборочных
единиц локомотивов и вагонов; причины возникновения неисправностей в
деталях машин; технологические методы повышения износостойкости деталей; механические, электрофизические способы восстановления работоспособности деталей.
Предназначено для студентов 4 и 5 курсов всех форм обучения по специальности 23.05.03 «Подвижной состав железных дорог», может быть полезно
для работников предприятий по ремонту подвижного состава, проходящих повышение квалификации в ИДО ДВГУПС.
УДК 629.44 (075.8)
ББК О 22я73
© ДВГУПС, 2019
2
СОКРАЩЕНИЯ И УСЛОВНЫЕ ОБОЗНАЧЕНИЯ
ДР – деповской ремонт
КР – капитальный ремонт
КВР – капитально-восстановительный ремонт
КТП – карта технологического процесса
КРП – капитальный ремонт с продлением полезного использования
КТТП – карта типового (группового) технологического процесса
КЭ – карта эскизов
ЛС – легированный слой
ОП – операционная карта
ОР – объект ремонта
ПТО – пункт технического обслуживания
СР – средний ремонт
СЕ – сборочная единица
ТИ – технологическая инструкция
ТО – техническое обслуживание
ТОД – техническое обслуживание с диагностированием
ТП – технологический процесс
ТР – текущий ремонт
ЭИЛ – электроискровое легирование
D – диаметр торца детали до обработки, мм
D1 – диаметр торца детали после обработки, мм
i – количество ходов суппорта токарного станка, ед.
Ф – время, затрачиваемое на изготовление изделий, мин
N – число изделий за текущий период, шт.
R – ритм выпуска деталей, шт./мин
τ – такт выпуска деталей, шт.
n – частота вращения заготовки или шпинделя станка, об/мин
S – подача, мм/об
t – глубина резания, мм
С – цеховая себестоимость обработки, руб.
– коэффициент загрузки оборудования
К m – коэффициент использования материала
Т – трудоемкость технологического процесса чел.-ч
Р – Производительность технологического процесса, 1/чел.-ч
kи.м – коэффициент использования материала
kо.в – коэффициент основного времени
kмех – степень механизации (автоматизации) технологического процесса
Ппр – пробег вагона до подачи его в очередной ремонт, тыс. км
3
Пгр – груженный пробег вагона, тыс. км
Ппор – порожний пробег вагона, тыс. км
Сэ – эквивалент по углероду
HCS – чувствительность сварного соединения к образованию горячих трещин
HVmax – максимальная твердость стали
4
ВВЕДЕНИЕ
Железнодорожному транспорту отводится особая роль и в обустройстве территорий, и в перемещении грузов и населения, и в обеспечении
обороноспособности государства.
Основная задача железнодорожного транспорта – обеспечение требуемых грузовых и пассажирских перевозок исправным подвижным составом, который должен максимальное время находиться в эксплуатации, при
этом часть времени приходится на техническое обслуживание и ремонт.
На железнодорожном транспорте традиционно уже более 100 лет система
ремонта локомотивов носит планово-предупредительный характер, при
котором локомотивы обслуживаются и ремонтируются в определенном
объеме и в регламентированные сроки по времени эксплуатации и пробегу. Планово-предупредительная система хорошо зарекомендовала себя,
однако для современных локомотивов она становится слишком затратной.
Система ремонта по фактическому состоянию («сломалось – починили»)
менее затратна, но недопустима, исходя из требований безопасности движения и обеспечения качества перевозочного процесса. Необходим третий путь – поэтапный переход на систему ремонта с учетом технического
состояния по данным бортовых, стационарных и переносных автоматизированных диагностических систем.
При организации ремонта по техническому состоянию достигается
максимальная эффективность применения средств технического контроля, диагностирования и их результатов. Особенность планового вида
ремонта – это обобщенный подход, когда в соответствии с нормативнотехнической документацией планирование объемов ремонта, количества ремонтов, моментов постановки на ремонт, продолжительности ремонта, а также затрат на него осуществляется на длительный период
для каждой серии локомотивов.
Ремонт по техническому состоянию – это индивидуальный подход, когда
планируются периодичность и объем контроля технического состояния в
соответствии с нормативно-технической документацией для каждой серии
локомотивов (вагонов), а объем и момент начала ремонта определяются
техническим состоянием оборудования каждого локомотива (вагона). Как
правило, эффективность индивидуального подхода к сервисному обслуживанию техники значительно выше, чем при обобщённом подходе.
Переход на ремонт по техническому состоянию требует наличия нормально работающей базы плановых видов ремонта. В противном случае
обеспечить качество требуемого объема ремонта по техническому состоянию – невозможно.
Чтобы получить наиболее быструю окупаемость затрат на ремонт по
техническому состоянию оборудования локомотивов (вагонов), на первом этапе необходимо определить оборудование, лимитирующее по
надёжности и затратам на сервисное обслуживание.
5
На втором этапе, с учетом имеющихся средств технического контроля
и диагностирования, провести на базовом предприятии необходимые эксперименты для обоснования перечня контролируемых параметров и периодичности их измерений для указанного выше оборудования, учитывая
при этом экономическую эффективность, затем, исходя из этого, разработать соответствующую нормативно-техническую документацию.
На третьем этапе следует внедрить запланированный вид ремонта
на это лимитирующее оборудование в другие ремонтные подразделения, где параллельно должны выполняться работы по восстановлению
требований технологий плановых видов ремонта для этого оборудования и переходу на его ремонт по техническому состоянию.
При этом часть сэкономленных средств, полученных от каждого предыдущего этапа, следует направлять на проведение ремонтных работ по
переходу на ремонт по техническому состоянию следующего лимитирующего оборудования.
Изучив дисциплину «Производство и ремонт подвижного состава»,
студент должен:
знать:
– причины отказов и брака, некачественного производства и ремонта
подвижного состава, а также его узлов;
– методы и приемы проверки технических решений по совершенствованию ремонта подвижного состава.
уметь:
– оценивать качество ремонта подвижного состава; анализировать
технологические процессы производства и ремонта подвижного состава
как объекта управления;
– осуществлять поиск и проверку новых технических решений, связанных с ремонтом подвижного состава.
владеть:
– методами оценки качества ремонта подвижного состава; навыками
применения технологических процессов производства ремонта подвижного
состава;
– навыками работы с техническими регламентами, стандартами и другими нормативными документами при проведении технического обслуживания, текущего и деповского ремонтов подвижного состава.
6
1. ХАРАКТЕРИСТИКИ ПРОИЗВОДСТВЕННОГО
И ТЕХНОЛОГИЧЕСКОГО ПРОЦЕССОВ
1.1. Виды производственных процессов
Производственный процесс – это комплекс технологических и трудовых процессов, превращающих предметы труда в готовую продукцию, соответствующую по качеству установленным стандартам или техническим
условиям (ГОСТ, ОСТ, ТУ). Под предметами труда принято понимать
сырьё, заготовки и комплектующие детали.
В силу целого ряда географических, производственных, экономических
и других причин на одном предприятии не существует «полного производственного процесса», включающего в себя все стадии производства – от
добычи природного сырья до выпуска готовых изделий. Полный производственный процесс разделён на отдельные части, выполнение которых осуществляется на следующих специализированных предприятиях:
на предприятиях по добыче металлургического сырья; на заводах по
выплавке чугуна, его переработке в сталь, производству проката и литью заготовок; на машиностроительных заводах и др.
Производственные процессы осуществляются на конкретных заводах:
металлургическом, машиностроительном, вагоностроительном, вагоноремонтном и др. В пределах завода производственный процесс осуществляется в различных цехах, которые являются основными производственными единицами.
По своему назначению и той роли, которая отводится производственным процессам, они подразделяются:
– на основные;
– вспомогательные;
– обслуживающие.
Рассмотрим их.
Основными производственными процессами называются процессы, результатом выполнения которых является непосредственный выпуск продукции – машин (подвижного состава) и запасных частей (колёсных пар, автосцепок и др.). Если все основные производственные
процессы объединить, то получится основное производство, которое
осуществляется в основных и заготовительных цехах (вагоносборочном,
колёсном, литейном и др.).
К вспомогательным производственным процессам относятся
процессы, связанные с изготовлением продукции, которая используется в
основном производстве. Это изготовление нестандартного инструмента
приспособлений и моделей, ремонт оборудования и др. Эти процессы реализуются во вспомогательных цехах – инструментальном, модельном, ремонтно-механическом и др.
7
Обслуживающими производственными процессами называются
процессы, обеспечивающие эффективное функционирование основного
и вспомогательного производства. Сюда относятся транспортные и
складские работы, научно-техническое обслуживание и др. Эти процессы выполняются соответственно в транспортном цехе, складском хозяйстве, лабораториях и других подразделениях.
Из вышесказанного следует, что все три производственных процесса –
это составляющие технологических процессов.
1.2. Виды технологических процессов
Технологический процесс – это изменение качественного состояния объекта работ (материала заготовки), взаимного расположения и
соединения деталей в целях получения готовой продукции.
Изменение качественного состояния объекта работ может проявляться в следующем:
– в изменении формы предметов труда путем механической обработки заготовки, получении заготовки литьём, ковкой, штамповкой. В
связи с этим существуют технологические процессы механической обработки, литья и др.;
– изменении свойств материала детали по всему её сечению путем
применения различных видов термообработки: технологических процессов закалки, отпуска, нормализации и др.;
– изменении свойств и химического состава поверхностного слоя материала детали путем осуществления технологических процессов химико-термического упрочнения, таких, как цементация, азотирование и др.;
– соединении деталей в сборочные единицы путём применения технологических процессов сборки с созданием подвижных и неподвижных,
разъёмных и неразъёмных соединений в соответствии с конструкцией
изделия;
– изменении внешнего вида изделия (например, окраски).
Производственный процесс включает в себя трудовой процесс.
Трудовой процесс – это воздействие рабочего на предмет труда,
при котором он затрачивает:
– физический труд путём выполнения определённых трудовых действий;
– умственный труд путём управления оборудованием, наблюдения за
его работой, контроля за ходом процесса.
Мерой оценки затрат труда является норма трудоёмкости, единицей
измерения которой является чел.-ч (чел.-мин).
Продолжительность трудового процесса, измеряемая в часах (мин),
называется нормой времени. В том случае, когда трудовой процесс
выполняется одним рабочим, норма трудоёмкости численно равна норме времени.
8
Последние 20 лет преимущественным способом получения точных
размеров деталей машиностроительных конструкций является механическая обработка, так как достичь заданных форм деталей, с требуемой
точностью и качеством их поверхностей, можно в основном механической
обработкой, при этом обеспечивается выполнение технических требований, установленных конструктором. Процесс механической обработки
осуществляется на металлообрабатывающих станках, с использованием
режущего и измерительного инструментов.
Механическая обработка деталей повышает качество выпускаемой
продукции, но при этом увеличивается её трудоёмкость и себестоимость.
Общеизвестно, что производство подвижного состава – это одна из отраслей машиностроения. Именно поэтому в изучаемой вами дисциплине
«Технология производства и ремонт подвижного состава», как и в других
специальных дисциплинах машиностроительного цикла, определяющая
роль отводится вопросам технологии механической обработки
деталей и сборки изделий.
Технологический процесс механической обработки – это последовательное изменение состояния заготовки (геометрические формы, размеры и качество поверхностей) благодаря её обработке режущим инструментом до момента получения готовой продукции. Выполняется технологический процесс на рабочих местах.
Рабочее место – это часть производственной площади цеха (участка), на которой располагается следующее (ГОСТ 14.004-831):
1) основное оборудование (станки, машины, автоматические линии и
др.);
2) вспомогательное оборудование (сборочные и сварочные стенды,
рольганги и др.);
3) технологическая оснастка (приспособления, инструмент, технологическая документация);
4) организационная оснастка (столы, тумбочки, средства сигнализации, освещения и др.).
Так как технологические процессы многообразны, то для удобства
механической обработки их расчленяют на отдельные части, среди которых основной является операция.
Операция – это часть технологического процесса, выполняемая на одном рабочем месте одним или группой рабочих. В операциях обработки
резанием наименование операции определяется, видом оборудования, на
котором она выполняется (например токарная, фрезерная и т. д.). На сле1
ГОСТ 14.004-83. Технологическая подготовка производства. Термины и определения основных понятий: Введ. 07.01.83. М.: Изд-во Стандартинформ, 2008. 50 с.
9
сарных и слесарно-сборочных работах наименование операции отражает
характер выполняемых работ (например, зачистка, сборка, клепка и др.).
В технологических документах запись содержания операции начинается с ключевого слова – глагола в неопределённой форме (например,
«строгать клин в соответствии с эскизом»; «собрать буксу в соответствии с чертежом» и т. д.). Операция является основой для производственного планирования и нормирования технологического процесса,
т. е. она служит основанием для расчётов трудоёмкости изготовления
изделий, необходимого оборудования, оснастки, материалов и требуемого количества рабочих соответствующей квалификации. В технологических документах операциям присваивается номер с использованием
арабских цифр – 5, 10, 15 и т. д. Допускается в номере операции добавлять слева нули (например, 005, 010, 015 и т. д.).
В состав операции входят её элементы: установ, позиция, переход, ход.
Установ – это часть операции, выполняемая при неизменном закреплении обрабатываемой заготовки на станке или в приспособлении.
Например, обточка вала при его закреплении в центрах с одного конца – это первый установ; обточка вала после его поворота и закрепления в центрах с другого конца – второй установ.
На эскизе заготовки условными
2
обозначениями указываются опоры и
3
1
зажимы (рис. 1.1).
3
4
Установы в технологических документах обозначаются буквами А, Б
и др.
Позиция – фиксированное положение, занимаемое закреплённой обРис. 1.1. Графическое изображение
рабатываемой заготовкой совместно
крепления заготовки в установе:
с приспособлением относительно ин1 – заготовка; 2 – условное обозначеструмента или неподвижной части
ние трехкулачкового патрона; 3 – вращающийся центр; 4 – опора
оборудования при выполнении определённой части операции.
Например, при изготовлении детали на многопозиционных карусельных станках заготовка устанавливается в приспособление, расположенное на столе станка. Далее, при неизменном её закреплении на столе,
она последовательно подводится поворотом стола, к позициям, на которых осуществляется обработка с помощью силовых головок.
Переходы подразделяются на технологические и вспомогательные.
Технологический переход – это часть операции, характеризующаяся обрабатываемой поверхностью, рабочим инструментом и режимом
работы станка. В течение перехода эти характеристики неизменны.
10
2
Ø25h10
Ø50
Вспомогательный переход – это часть операции, состоящая из
действий человека и оборудования, которые не сопровождаются изменением формы, размеров, шероховатости поверхности, но необходимы
для выполнения технологического перехода (например, установка или
снятие инструмента, поворот суппорта, измерение размера и т. д.).
Переходы в операционных картах обозначаются подробно.
Например: «подрезать торец с диаметра D до D1 начерно (начисто)».
На эскизе заготовки поверхность обработки выделяется толстой линией,
в конце поверхности обработки показывается положение режущего инструмента, а стрелкой указывается направление подачи (инструмента
или заготовки). В операционных картах переходы обозначаются арабскими цифрами 1, 2 и т. д.
Переход включает в себя ходы.
В свою очередь ход разделяется на рабочий и вспомогательный.
Рабочий ход – это часть перехода, состоящая из однократного перемещения инструмента относительно заготовки, сопровождаемая изменением формы, размеров, шероховатости поверхности. За каждый
рабочий ход снимается один слой металла.
Вспомогательный ход – это часть перехода, состоящая из однократного перемещения режущего инструмента относительно заготовки,
не сопровождаемая изменением формы, размеров, шероховатости поверхности.
Rz= 2,5
2×45о
Например, возвращение суппорта
токарного станка в исходное положение. В нормировочных картах указывается количество ходов ( i = 1; i = 2
и т. д.).
40
Рассмотрим в качестве примера
50
разработку плана изготовления валика (рис. 1.2) […] путем механической обработки заготовки из пруткоРис. 1.2. Чертёж детали. Технические
требования: 1. Неуказанные прового сортового проката Ø50 мм.
дольные отклонения – h14
План обработки выполняется в
табличной форме (рис. 1.3)2.
С 1975 г. в отечественном машиностроении введена Единая система
технологической подготовки производства (ЕСТПП), построение которой
представлено на рис. 1.43.
Мотовилов К.В., Лукашук В.С., Криворудченко В.Р., Петров А.А. Производство и
ремонт вагонов / под ред. К.В. Мотовилова. М.: Маршрут, 2008.
3
Классификация, разработка и применение технологических процессов:
Р 50-54-93-83: введ. 04.07.84. М.: Изд-во Ротапринт ВНИИНМАШ, 1989. 33 с.
11
Номер Наименование
операции
операции
Установы
Переходы
Эскиз установов
и переходов
Ходы
3
А
–
–
80
1. Подрезать
торец на 3 мм
2
40
05
2. Проточить
на длину 40 мм
с Ø50 на Ø25
Токарная
3
2x45
3. Снять фаску
2×45
1
50
3
4. Отрезать
на длину 50 мм
1
Рис. 1.3. План обработки валика
ЕСТПП
Единая
система
конструкторcкой документации (ЕСКД)
Единая
система
технологической документации (ЕСКД)
Государственная
система
обеспечения
единства
измерений
Единая система
классификации
и кодирования
экономической
документации
Планово и
организационнораспорядительная
документация
Единая
Разработка и
система
постановка на
аттестации
производстве
качества
(ГОСТ 15001-73)
продукции
Нормативнотехническая
документация
Документация
по механизации
и автоматизации
обработки
информации
Рис. 1.4. Структурная схема единой системы
технологической подготовки производства
12
1.3. Документация производственного
и технологического процессов
Одной из функций Единой системы технологического процесса производства (ЕСТПП) является разработка технологических процессов изготовления изделий на основе Единой системы технологической документации (ЕСТД). В Министерстве путей сообщения в 2009 г. разработан руководящий технологический документ (РД 32 ЦВ 096-20094) по оформлению и комплектации технологической документации на предприятиях вагонного хозяйства.
Система ЕСТД устанавливает на всех предприятиях вагонного хозяйства единые правила оформления и ведения технологической документации, обеспечивает стандартизацию обозначений и унификацию документации на различные виды работ. Технологические документы подразделяются на документы общего и специального назначения5.
Документами общего назначения являются: маршрутная карта;
карта эскизов (КЭ) и технологическая инструкция (ТИ).
Маршрутная карта содержит перечень всех технологических операций, включая контроль и перемещение деталей в порядке технологической
последовательности, с указанием данных по оборудованию, оснастке, материальным нормативам и трудозатратам.
Карта эскизов является графическим документом, содержащим эскизы, поясняющие выполнение технологического процесса по операциям и переходам.
Технологическая инструкция содержит описание техпроцесса, методов и приёмов выполнения работ, правил эксплуатации средств технического оснащения.
Документами специального назначения являются:
– карта технологического процесса (КТП);
– карта типового (группового) технологического процесса (КТТП);
– операционная карта (ОП).
Карта технологического процесса содержит перечень операций техпроцесса одного вида формообразования (обработки, сборки и др.) и сведения по оборудованию, оснастке, материальным и трудовым затратам.
Карта типового (группового) технологического процесса разрабатывается для группового техпроцесса и содержит сведения, аналогичные КТП.
4
Оформление и комплектация технологической документации на предприятиях и
в организациях вагонного хозяйства: РД 32 ЦВ 096-2009. Взамен РТМ 32 ЦВ 200-87;
ввд. 12.10.09. М.: Изд-во стандартов, 2009. 116 с.
5
Мотовилов К.В., Лукашук В.С., Криворудченко В.Р., Петров А.А. Указ. соч.
13
Операционная карта разрабатывается на каждую операцию с указанием:
– последовательности выполнения работ по переходам;
– данных о техническом оснащении;
– режимов обработки;
– нормы времени.
ВОПРОСЫ ДЛЯ САМОКОНТРОЛЯ
1. Что такое производственный процесс? Назовите его виды.
2. Приведите примеры основного, вспомогательного и обслуживающего производственного процесса.
3. Что такое технологический процесс? Назовите его виды.
4. Что затрачивается для выполнения трудового процесса?
5. Дайте определение понятия «операция». Приведите примеры технологического процесса.
6. Назовите элементы процесса «операция». Объясните это на примерах по каждому элементу.
7. Изобразите структурную схему «Единой системы технологической
подготовки производства».
8. Назовите виды технологических документов общего назначения в
соответствии с ЕСТД.
9. Какие виды технологических документов относятся к специальным
в соответствии с ЕСТД?
Рекомендуемая литература: [32] (см. Библиографический
список).
2. ПРОЕКТИРОВАНИЕ ТЕХНОЛОГИЧЕСКИХ ПРОЦЕССОВ
МЕХАНИЧЕСКОЙ ОБРАБОТКИ
2.1. Технологический процесс механической обработки
Стандартами ЕСТД установлены следующие характеристики технологического процесса.
Цикл технологической операции – интервал времени от начала и
до конца периодически повторяющейся технологической операции независимо от числа одновременно изготовляемых изделий.
Например, в приспособление устанавливают и одновременно фрезеруют пять заготовок. Время фрезерования (10 мин) – цикл фрезерной
операции. Через 10 мин начинают обработку следующих пяти заготовок.
14
Такт выпуска – интервал времени, через который периодически выпускается изделие определенного наименования, типоразмера и исполнения.
Такт выпуска tВ определяется отношением времени Ф, затраченном на
изготовление изделий к числу N изделий, изготовленных за этот период.
Например, за 10 мин обработано пять заготовок. В этом случае такт
выпуска tВ Ф 10 2 шт.
N
5
Ритм выпуска – количество изделий определенного наименования,
типоразмера и исполнения, выпускаемых в единицу времени. Ритм выпуска R – величина, обратная такту выпуска tВ .
Для предыдущего примера ритм R 1 Ф 5 0,5 шт./мин
tВ
N
10
(или 30 шт./ч).
Производственная программа – перечень наименований изготовляемых или ремонтируемых изделий с указанием объема выпуска и срока
выполнения по каждому наименованию. Производственная программа
машиностроительного завода (или цеха) содержит: номенклатуру всех
изготовляемых деталей или собираемых изделий (с точным указанием
типов и размеров); сведения о количестве изделий каждого наименования, подлежащих выпуску в течение года (месяца или другого периода);
перечень наименований и количество запасных деталей к выпускаемым
изделиям. К производственной программе прикладывают следующую
техническую документацию: чертежи общих видов, сборочные чертежи и
деталировки; спецификации и описания конструкций (назначение,
устройство, принцип действия, условия эксплуатации и пр.); технические
условия на изготовление и приемку (методики контроля показателей качества, программы испытаний и др.).
Согласно ЕСТД (ГОСТ 3.1109-826) различают три вида технологических
процессов (ТП): 1) единичный; 2) типовой; 3) групповой. Каждый ТП разрабатывают при подготовке производства изделий, конструкции которых отработаны на технологичность. Технологические процессы разрабатывают
для изготовления нового изделия или совершенствования выпускаемого.
Единичный ТП – это ТП изготовления или ремонта изделия одного
наименования, типоразмера и исполнения независимо от типа производства. Единичные ТП разрабатывают для изготовления оригинальных
изделий (деталей, сборочных единиц), не имеющих общих конструктивных и технологических признаков с изделиями, ранее изготовленными
на предприятии.
Типовой ТП – это ТП изготовления группы изделий с общими конструктивными и технологическими признаками, характеризующимися общностью содержания и последовательностью выполнения операций, и пе6
ГОСТ 3.1109-82. Единая система технологической документации. Термины и
определения основных понятий. М.: Изд-во Стандартинформ, 2012. 187 с.
15
реходов. Типовой ТП используют как информационную основу при создании рабочих ТП и как рабочий ТП при наличии всей необходимой информации для производства изделий. На базе этих ТП разрабатывают стандарты предприятий (СТП) для типовых технологических процессов.
Групповой ТП – это технологический процесс изготовления группы изделий с разными конструктивными, но общими технологическими признаками; это процесс обработки заготовок различной конфигурации, состоящий
из комплекса групповых технологических операций, выполняемых на специализированных рабочих местах в последовательности технологического
маршрута изготовления определенной группы изделий. Групповые ТП разрабатывают для всех типов производств только на уровне предприятия.
Типовые и групповые ТП являются унифицированными ТП, относящимися к группе изделий с общими конструктивными и (или) технологическими признаками. Они (ТП) находят широкое применение в мелкосерийном и серийном производствах, но и реже в крупносерийном.
По классификации ЕСТД каждый из рассмотренных ТП может быть
перспективным или рабочим.
Перспективным называют технологический процесс, соответствующий современным достижениям науки и техники, методы и средства которого полностью или частично предстоит освоить на предприятии.
Рабочий ТП – это ТП, выполняемый по рабочей технологической и
(или) конструкторской документации. Рабочие ТП разрабатывают на
предприятиях для изготовления различных изделий. Рабочие ТП могут
быть проектными, стандартными и временными.
Проектный ТП – это ТП, выполняемый по предварительному проекту технологической документации.
Стандартный ТП – это установленный стандартом ТП, который
выполняют по рабочей технологической и (или) конструкторской документации, оформленной в соответствии с требованиями стандартов
(ОСТ, СТП), и который относится к конкретному оборудованию, режимам
обработки и технологической оснастке.
Временный ТП – это ТП, применяемый на предприятии в течение ограниченного периода времени из-за отсутствия необходимого оборудования
или в связи с аварией до замены на более современный и экономичный.
При создании автоматических линий, гибких автоматизированных
производств и в других случаях разрабатывают комплексные ТП, в состав
которых, кроме основных механических операций, включают операции
перемещения, термической обработки, контроля и очистки обрабатываемых заготовок и др.
Разрабатываемый ТП должен обеспечивать повышение производительности труда и качества изделия, снижение трудовых и материальных
затрат, сокращение вредных воздействий на окружающую среду. ТП дол16
жен соответствовать требованиям техники безопасности и промышленной санитарии, установленным системой стандартов безопасности труда (ССБТ), инструкциями и другими нормативными документами. Основой для разработки ТП обычно служат имеющиеся типовой или групповой ТП, а при их отсутствии – действующие единичные ТП изготовления
аналогичных изделий.
Исходную информацию для разработки ТП подразделяют на базовую, руководящую и справочную.
Базовая информация – это данные, содержащиеся в чертежах и
технических условиях на изготовление и приемку изделия, а также объем программного задания и срок его выполнения (по этапам).
Руководящая информация содержит: закрепленные государственными и отраслевыми стандартами требования к технологическим процессам и методам управления ими, к оборудованию и оснастке; документацию на действующие единичные, типовые и групповые ТП; производственные инструкции; документацию по технике безопасности и промышленной санитарии, материалы по выбору технологических нормативов (режимы обработки, припуски, нормы расхода материалов) и др.
Справочная информация состоит из описаний прогрессивных методов изготовления, каталогов, паспортов, справочников, альбомов компоновок средств технологического оснащения, планировок производственных участков и др.
При проектировании ТП для действующих предприятий технолог
должен быть знаком со структурой предприятия, принятой системой
планирования, возможностями заготовительных и вспомогательных цехов. Технолог должен учитывать общую производственную обстановку
(состав и степень загрузки оборудования, возможности комплектования
инструментом и приспособлениями, обеспеченность предприятия квалифицированной рабочей силой и др.).
Цель проектирования ТП механической обработки – подробное описание процессов изготовления детали с необходимыми технико-экономическими расчетами и обоснованиями принятого варианта. В основе разработки ТП обычно лежат два принципа: 1) технический и 2) экономический.
В соответствии с техническим принципом спроектированный ТП
должен полностью обеспечивать соблюдение всех требований рабочего
чертежа и технических условий на изготовление данного изделия.
ТП должен выполняться с наиболее полным и правильным использованием всех технических возможностей оборудования, инструментов и
прочих средств технологического оснащения.
В соответствии с экономическим принципом изделия должны быть
изготовлены с минимальными затратами труда и издержками производства при наименьших затратах времени и наименьшей себестоимости
17
изделия. Эффективность и рентабельность проектируемого ТП выявляют по всем элементам, из которых ТП рассчитывают либо определяют
по укрупненным показателям.
Оптимизация ТП заключается в том, что в установленный промежуток времени необходимо обеспечить выпуск требуемого количества изделий заданного качества при возможной минимальной себестоимости
их изготовления. В простейшем случае оптимизируют основные лимитирующие операции, в более сложных случаях – все операции. В качестве
целевых функций при оптимизации чаще всего принимают достижение
минимальной себестоимости изделия, реже – достижение наибольшей
производительности или наивысшего качества и др.
Из имеющихся вариантов технологических процессов изготовления одного и того же изделия предпочтение отдают наиболее производительному и рентабельному. При равной производительности сопоставляемых
вариантов выбирают наиболее рентабельный, а при равной рентабельности – наиболее производительный. В исключительных случаях (срочный
выпуск важной продукции, ликвидация возникающих «узких мест» производства и т. п.) в рамках данного предприятия на определенный период за
основу может быть принят наиболее производительный (но менее рентабельный) вариант ТП. Тогда для изготовления изделий составляют временный рабочий единичный технологический процесс.
Разработку технологических процессов начинают с изучения и технологического контроля исходных данных (чертежи, описания, технические
условия и прочая конструкторская документация), а также программных
заданий на выпуск изделия. По этим материалам знакомятся с назначением и конструкцией изделия, его техническими характеристиками, требованиями к качеству, сроками его изготовления и условиями эксплуатации.
Дальнейшая работа складывается из следующих одиннадцати
основных этапов:
1) определяют возможный тип производства (единичное, серийное
или массовое);
2) с учетом установленного типа производства анализируют технологичность конструкции изделия и разрабатывают мероприятия по ее повышению. Отработку изделия на технологичность считают обязательным этапом технологического проектирования;
3) выбирают, а затем подтверждают соответствующими расчетами
наиболее технологичный и экономичный метод получения заготовки;
4) подбирают эффективные способы и последовательность обработки поверхностей, определяют технологические базы;
5) составляют технологический маршрут обработки детали. Для каждой операции предварительно подбирают оборудование и технологическую оснастку, определяют величину припусков на обрабатываемые поверхности;
18
6) уточняют структуру и степень концентрации операций: устанавливают содержание и последовательность выполнения всех переходов;
7) для каждой операции окончательно выбирают режущий, вспомогательный, контрольно-измерительный инструмент и приспособления;
8) устанавливают необходимые режимы резания и настроечные размеры, а также рассчитывают составляющие силы и моменты сил резания;
9) проверяют соответствие подобранного оборудования по мощности
приводов, прочности его механизмов и степени загрузки;
10) выполняют аналитические расчеты прогнозируемой точности обработки и шероховатости функциональных поверхностей;
11) производят техническое нормирование операций, устанавливают
квалификацию исполнителей, определяют экономичность и эффективность спроектированного технологического процесса;
12) разрабатывают комплект необходимой технической документации.
В процессе разработки технологических процессов для конкретных
деталей объем всего комплекса проектных работ и содержание отдельных этапов могут уточняться и изменяться. Несколько взаимосвязанных
этапов могут объединяться в один общий, при этом может меняться последовательность их выполнения.
Для установления типа производства необходимо рассчитать такт
выпуска деталей по формуле
τ
60 Фд
,
N
(2.1)
где Фд – действительный фонд времени в планируемом периоде; N – программа выпуска за этот период.
Если τ tоп , где tоп – оперативное время обработки детали (оценивается ориентировочно), а планируемый период исчисляется годами, то
производство считается массовым. Поэтому для обработки детали организуются поточные или автоматические линии, а технологический процесс строится по принципу дифференциации или концентрации операций. Если период выпуска исчисляется месяцами, то производство считается серийным, оборудование располагается по ходу технологического процесса или организуются переменно-поточные линии обработки,
а технологический процесс выполняется дифференцированно.
Если τ tоп , то производство считается единичным, оборудование
располагается по групповому признаку, а технологический процесс выполняется по принципу концентрации операций.
Выбор исходной заготовки (прокат, литьё, поковка и др.) оценивается
её себестоимостью, качеством и минимальными затратами на обработку.
19
План обработки детали – это последовательность обработки различных поверхностей детали с установлением метода обработки (точение, фрезерование и т. д.). При установлении последовательности выполнения операций (переходов), то есть технологического маршрута,
требуется руководствоваться следующим:
1) реализовать принцип среднеэкономической точности;
2) в первую очередь следует обрабатывать поверхности, которые
будут являться базами для дальнейшей обработки, применяя принципы
постоянства и совмещения баз;
3) затем необходимо обрабатывать поверхности с наибольшими припусками, что позволит обнаружить внутренние дефекты в материале заготовки;
4) операции, где возможен брак из-за сложности механической обработки, должны выполняться в самом начале процесса;
5) дальнейшая последовательность операций устанавливается в зависимости от требуемой точности обработки, то есть более точные операции сдвигаются на конец технологического процесса.
В зависимости от вида заготовки, используя справочные данные,
распределяют общий припуск на межоперационные припуски.
При выборе типа-размера станков исходят из операций обработки,
габаритов заготовки, обеспечения необходимой точности и шероховатости. Если эти требования можно выполнить на различных станках, то
необходимо руководствоваться следующим:
а) возможно более полным использованием станка по мощности;
б) наименьшей ценой станка;
в) наименьшими затратами времени на обработку;
г) наименьшей стоимостью обработки.
Одновременно с выбором станка необходимо установить, какое приспособление требуется для выполнения намеченной операции. Если приспособление является принадлежностью станка, то указывается его
наименование (патрон, тиски и др.). Если возникает потребность в изготовлении специального приспособления то, прежде чем приступить к разработке конструкции, определяется его экономическая целесообразность.
Выбор режущего инструмента зависит от типа станка, материала заготовки, её размеров, конфигурации, требуемой точности и шероховатости.
Особое внимание уделяется выбору материала режущей части инструмента (инструментальные стали, твердые сплавы, металлокерамические сплавы и др.).
Измерительный инструмент (линейки, штангенциркули, микрометры, нутромеры и т. д.) выбирается в зависимости от вида измеряемой
поверхности, габаритов детали, требуемой точности.
20
Установление режимов резания основывается на следующем:
– на данных об изготавливаемой детали (чертёж и технические условия) и заготовке;
– роде материала заготовки, его характеристике;
– форме, размерах заготовки и допусках на обработку;
– точности и качестве обработки детали;
– паспортных данных станков.
Рассчитанные элементы режимов резания (частота вращения заготовки
или шпинделя станка n, 1/мин; подача S, мм/об; глубина резания t, мм)
должны обеспечивать наибольшую производительность и загрузку станка по мощности и наименьшую себестоимость.
Профессия и разряд рабочего устанавливается по тарифно-квалификационным справочникам.
Технико-экономическая оценка разработанных технологических процессов производится по следующим показателям:
а) норма времени, определяемая по формулам:
1) при массовом производстве
Т шт tшт i ;
(2.2)
2) при серийном производстве
tпз
;
n
(2.3)
Т шт к Т шт tпз ,
(2.4)
Т шт к Т шт
3) при единичном производстве
где Т шт – штучная норма времени, это время, затрачиваемое на выполнение всех операций технологического процесса, мин; tшт i – штучное время на выполнение одной операции, мин; Т шт к – штучно-калькуляционная норма времени, мин; tпз – подготовительно-заключительное
время (получение и сдача работы, материала, инструмента, приспособлений и др.), мин; n – количество деталей в партии.
Штучное время при выполнении одной операции определяется по
формуле
tшт i to tв tо.е tоб ,
(2.5)
где to – основное время, время непосредственного выполнения работы
(процесса резания), мин; tв – вспомогательное время, это время, затрачиваемое на подготовку к выполнению основной работы (установка заготовки,
инструмента, режимов резания и др.), мин; to tв tоп – оперативное вре21
мя, мин; tо.е – время на отдых и естественные надобности, мин; tоб – время на обслуживание рабочего места (подготовка и уборка станка), мин.
Время на tо.е , tоб , tпз нормируется в процентах от tоп :
а) цеховая себестоимость обработки определяется по формуле
С RM Z,
(2.6)
где R – стоимость основной рабочей силы, руб.; M – стоимость материалов (заготовки), руб.; Z – стоимость накладных расходов, руб.
Стоимость основной рабочей силы определяется исходя из нормы
времени, количества рабочих, их тарифного разряда, доплат за стаж работы и территориальный пояс. Стоимость накладных расходов составит
Z %N R ,
(2.7)
где %N – процент цеховых накладных расходов.
%N
К
100 ,
R
(2.8)
где К – сумма косвенных годовых расходов цеха (расходы на отопление, электроэнергию, воду, амортизацию зданий и оборудования, оплату
труда инженерно-технических работников и др.), руб.; R – годовой
фонд заработной платы основных рабочих цеха, руб.;
б) коэффициент загрузки оборудования, определяется по формуле
р
,
пр
(2.9)
где р – потребное (расчётное) количество оборудования; пр – принятое количество оборудования;
в) коэффициент использования материала, определяется по формуле
G
,
(2.10)
Кт
Gзаг
где G – масса готовой детали; Gзаг – масса заготовки.
2.2. Типизация технологических процессов
Для обработки одной и той же детали можно разработать различные
варианты технологических процессов, применив различные методы обработки. Даже при одинаковых производственных условиях и программе вы22
пуска разработка техпроцессов зависит не только от опыта технического
персонала, но и опыта, накопленного на предприятии. Все эти обстоятельства создают сложности при разработке технологических процессов и требуют больших затрат времени для установления лучшего варианта.
Упростить и ускорить разработку технологических процессов помогает типизация технологических процессов, то есть создание типовых
процессов для обработки определённого типа деталей, имеющих близкое конструктивное исполнение и размеры. Идея типизации принадлежит профессору А.П. Соколовскому. Типизация базируется на классификации деталей, то есть их разделении на классы.
Например, класс Валы (В). Сюда входят валы, валики, оси, штоки,
пальцы, цапфы и др.; класс Втулки (А). К нему относятся: втулки, вкладыши, гильзы и другое, и т. д.
Детали каждого класса разбиваются на группы, группы на подгруппы,
подгруппы на типы. В итоге получается совокупность деталей всё более
схожих по технологическим признакам.
В один тип объединяются те детали, при обработке которых применяется и одинаковый маршрут выполнения операций, и одинаковые
оборудование и технологическая оснастка. На перечень деталей данного типа разрабатывается технологический процесс, который будет являться типовым технологическим процессом и по которому будут обрабатываться все детали данного типа.
Если технологи какого-либо предприятия имеют типовые технологические процессы, то они могут:
а) после определения к какому классификационному типу относится
данная деталь применить для неё соответствующий типовой технологический процесс, если позволяет оборудование данного предприятия;
б) использовать типовой технологический процесс (заимствовать режимы резания, инструмент, приспособления) для разработки нужного,
этим достигается экономия времени и повышается качество разработки.
2.3. Групповые технологические процессы
На заводах серийного производства
применяются групповые технологические
процессы (ГТП). ГТП – это технологический
процесс изготовления группы деталей с
различными конструктивными, но общими
технологическими признаками. В этом случае технологический процесс разрабатывается на комплексную деталь (рис. 2.1)7.
7
Рис. 2.1. Комплексная деталь
Мотовилов К.В., Лукашук В.С., Криворудченко В.Р., Петров А.А. Указ. соч.
23
Комплексная деталь объединяет мелкие партии деталей, каждую из которых нерационально обрабатывать на поточных линиях. Но после их объединения в комплексную деталь возможна организация переменнопоточных линий, позволяющих обрабатывать детали мелкими партиями,
применяя режимы обработки для поверхностей фактической детали, соответствующие аналогичным поверхностям комплексной детали.
2.4. Экономическая оценка технологических разработок
В основу разработки технологических процессов изготовления и ремонта вагонов должны быть положены два принципа – технический и экономический. В соответствии с первым принципом проектируемый технологический процесс должен обеспечить выполнение всех требований рабочих
чертежей и технических условий на изготовление (ремонт) и приемку изделия. Согласно второму принципу изготовление или ремонт вагона должны
вестись с минимальными затратами труда и издержками производства.
Проектирование технологического процесса является многовариантной
задачей. Для изготовления (ремонта) одной и той же детали или сборочной
единицы могут быть разработаны различные технологические процессы,
отличающиеся структурой, содержанием, технологической оснащенностью,
методами восстановления деталей, затратами на их выполнение.
Технический и экономический принципы проектирования технологических процессов всегда находятся в диалектическом противоречии. Разрешение этого противоречия достигается путем компромисса и решения задач оптимизации технологических процессов. Технический принцип должен
соблюдаться всегда. Поэтому компромисс возможен только между затратами труда (производительностью) и издержками производства. При равной
производительности сопоставляемых вариантов технологических процессов выбирают процесс, обеспечивающий минимум затрат. При равных затратах выбирают более производительный технологический процесс.
Технологический процесс – это продукт труда инженера-технолога,
причем практически всегда это новый продукт. Как и любой продукт труда, он не может быть создан в идеальном виде за один прием, а должен
рождаться в процессе инженерного творчества. Кроме этого, инженертехнолог не имеет права на грубую ошибку, поскольку она может привести к безвозвратным потерям времени и средств на подготовку производства или аварийной ситуации при эксплуатации вагона.
Из сказанного следует, что необходимо иметь систему показателей,
по которым можно было бы сопоставлять варианты технологического
процесса, а также определять качество окончательной технологической
разработки.
Показатели качества технологического процесса можно подразделить
на две группы – технические и технико-экономические. Наиболее важными
и ёмкими техническими показателями качества технологического процесса
являются его надёжность, трудоёмкость и производительность.
24
Надежность технологического процесса – свойство обеспечивать
изготовление или ремонт составных частей вагона в заданном объеме,
при сохранении во времени установленных требований к их качеству.
Для оценки надежности технологического процесса принимают тс же показатели, что и для оценки надежности любой машины.
Отметим, что технологический процесс является весьма сложной системой. Поэтому для обеспечения его высокой надежности необходимо
поддерживать на очень высоком уровне надежность его элементов.
Трудоемкость технологического процесса определяется суммой нормы
штучного (штучно-калькуляционного) времени по всем его операциям8
n
Т Tшт i ,
(2.11)
i 1
где n – общее число операций в технологическом процессе; Tшт i – норма
штучного времени на операцию.
Трудоемкость изготовления (ремонта) вагона определяется суммой
трудоемкостей всех технологических процессов.
Производительность технологического процесса – величина, обратная его трудоемкости, Р 1/ Т . Поскольку норма штучного времени отводится на операцию при изготовлении одного изделия, а ее измеритель –
чел.-ч (маш.-ч), то физический смысл производительности технологического процесса состоит в числе изделий, изготовленных одним рабочим (машиной) в единицу времени. Это число далеко не всегда оказывается целой величиной.
Для сопоставления вариантов технологического процесса на ранних
стадиях проектирования, кроме рассмотренных, могут быть применены такие показатели, как коэффициент использования материала kи.м. , коэффициент основного времени kо.в , степень механизации (автоматизации)
технологического процесса kмех , которые определяются соответственно
выражениями9
kи.м
n
n
тд
t
, kо.в o , kмех tоп i м / tоп i ,
тз
Т шт
i 1
i 1
(2.12)
где тд , тз – масса соответственно детали и заготовки; tоп i м – оперативное время операции, выполняемое с применением механизмов или в
автоматическом режиме; tоп i – общее оперативное время на операцию.
8
9
Там же.
Там же.
25
Из изложенного выше важно отметить следующее10.
1. Нельзя производительность трактовать как число изделий, изготовляемых в единицу времени, так как это понятие имеет другой смысл.
2. По данным литературных источников рекомендуется определять
показатель kмех как отношение числа автоматизированных единиц технологического оборудования к их общему числу.
Полагаем, что такой подход не вполне объективен, поэтому воспользуемся выражением (2.12) для определения показателя kмех , что позволит рассчитывать данный показатель, в том числе и для слесарных и
слесарно-сборочных работ, при которых технологические переходы часто выполняются рабочими, а не станками.
Наиболее общим экономическим показателем технологического процесса является технологическая себестоимость изготовления изделия.
Технологическая (цеховая) себестоимость изготовления (ремонта) изделия – это сумма всех затрат по цеху, необходимых для изготовления
(ремонта) изделия. Для сопоставления вариантов технологического процесса необходимо пользоваться следующим развернутым выражением11
С См К з Зо Зв Ао Св.м Си Сэ Ср Ц р ,
(2.13)
где См – стоимость материалов (при поставке заготовки другим цехом и
для сборочных технологических процессов – это стоимость полуфабрикатов собственного изготовления); К з – коэффициент отчислений (единый
социальный налог) от заработной платы рабочих ( Зо – основных, Зв –
вспомогательных); Ао – амортизационные отчисления от стоимости технологического оборудования; Св.м – стоимость расходных и вспомогательных материалов (присадочных, лакокрасочных, смазочных и др.); Си –
доля стоимости инструмента и малоценных приспособлений, приходящаяся на одно изделие; Сэ – стоимость энергоресурсов (электроэнергии на
технологические цели, сжатого воздуха и др.); Ср – доля затрат на ремонт
и содержание оборудования; Ц р – цеховые расходы (амортизационные
отчисления и расходы на содержание производственных площадей и др.).
Метод прямого расчета себестоимости трудоемкий. При сопоставлении вариантов технологического процесса целесообразно из приведенного выражения исключить слагаемые, остающиеся одинаковыми для
сравниваемых вариантов (например, для сборочных технологических
процессов слагаемое См будет всегда одинаковым, слагаемое Ц р будет
одинаковым при одинаковой программе выпуска изделий).
10
11
Там же.
Там же.
26
Сравнение вариантов на основе минимума себестоимости проводят
в том случае, если сравниваемые варианты не требуют дополнительных
капиталовложений и не приводят к изменению программы выпуска изделий. Если эти условия не выполняются, то вариант технологического
процесса выбирают по критерию минимума приведенных затрат12
З Сгод Ен Кд ,
(2.14)
где Сгод – себестоимость годовой программы выпуска изделий; Ен – нормативный коэффициент экономической эффективности капиталовложений
( Ен 115
, 1, 2 ); К д – размер дополнительных капиталовложений.
При оптимальном проектировании технологических процессов (оптимизация проводится в процессе их проектирования) оптимальный вариант
является результатом проектирования. При этом в качестве функции цели
может быть принят комплексный критерий Ц Р / Зус , где Зус – условные приведенные затраты, рассчитанные без учета заработной платы
основных производственных рабочих, так как она косвенно учтена в
производительности Р через штучное время. Оптимальным считается
вариант технологического процесса, обеспечивающий Ц max .
При разработке технологических процессов ремонта вагона возникает необходимость установления целесообразности ремонта деталей
способами их восстановления. Способ восстановления детали может
быть выбран по критерию минимума себестоимости, аналогично рассмотренному выше.
После выбора способа восстановления детали необходимо определить
целесообразность восстановления вообще. Критерием целесообразности
восстановления детали (сборочной единицы) может служить условие13
Св Сз / Т в Сн Сз / Т н ,
(2.15)
где Св – себестоимость восстановления детали; Сз – себестоимость работ
по замене детали (разборка-сборка); Т в , Т н – средний срок службы восстановленной и новой детали соответственно; Сн – себестоимость изготовления новой детали (для покупных изделий – цена).
Отметим, что расходы на изготовление детали на конкретном вагоноремонтном заводе могут значительно превышать ее цену при условии
поставки детали другими предприятиями.
12
13
Там же.
Там же.
27
ВОПРОСЫ ДЛЯ САМОКОНТРОЛЯ
1. Назовите характеристики технологического процесса.
2. В чем заключается цель проектирования и оптимизация технологического процесса?
3. Назовите этапы разработки технологического процесса.
4. Чем следует руководствоваться при установлении последовательности выполнения технологического маршрута?
5. Каким образом осуществляется выбор типа, размера станков, режущего инструмента и измерительного инструмента?
6. На чем основывается выбор режимов резания на станках?
7. Назовите показатели технико-экономической оценки разработанных технологических процессов.
8. Какова цель типизации технологических процессов?
9. Что такое групповой технологический процесс?
10. Назовите технические показатели качества технологического
процесса.
11. Какие показатели используются для сопоставления вариантов
технологического процесса? Приведите формулы.
Рекомендуемая литература: [32, 35] (см. Библиографический
список).
3. ОСНОВНЫЕ ПОЛОЖЕНИЯ
ПО ТЕХНИЧЕСКОМУ ОБСЛУЖИВАНИЮ
И РЕМОНТУ ПОДВИЖНОГО СОСТАВА
3.1. Планово-предупредительная система
технического обслуживания и ремонта локомотивов
Под системой технического обслуживания (ТО) и текущего ремонта (ТР) следует понимать совокупность взаимосвязанных средств,
документации и исполнителей, необходимых для поддержания и восстановления работоспособности локомотивов.
Под ТО понимают комплекс работ профилактического характера (по
осмотру, очистке, смазке, креплению, регулировке и т. д.), цель которых
постоянно поддерживать локомотив в работоспособном состоянии.
Под ремонтом понимают комплекс работ, направленных на восстановление работоспособного состояния локомотивов, путем устранения
неисправностей в деталях и узлах.
Ремонты подразделяются на плановые и неплановые.
Плановый ремонт – это ремонт, предусмотренный требованиями
нормативно-технической документации.
28
Неплановый ремонт – это ремонт, постановка на который осуществляется без предварительного назначения. Плановый ремонт подразделяется на текущий, средний и капитальный.
Текущий и средний ремонт (СР) – это ремонт, выполняемый для частичного восстановления ресурса локомотива и состоящий в замене и
восстановлении отдельных деталей и узлов. Эти виды ремонта выполняются в локомотивных депо или на заводах.
Капитальный ремонт (КР) – это ремонт, выполняемый для устранения
неисправностей и восстановления полного или близкого к полному ресурса
локомотива, с заменой или восстановлением любых его частей, включая и
базовые. Капитальный ремонт выполняется на ремонтных заводах.
Планово-предупредительная система обслуживания и ремонта состоит из ТО-1, ТО-2, ТО-3, ТО-4, ТО-5, ТР-1, ТР-2, ТР-3, СР и КР.
Периодичность ТО и ремонтов локомотивов регламентирована Распоряжением ОАО «РЖД» № 2070р от 21.09.18 г. (см. прил. 1, 2, 3).
Согласно данному распоряжению нормы продолжительности простоя
и трудоемкости ТО и ремонтов устанавливаются по каждому локомотивному депо начальником железной дороги. Дифференцированные нормы
продолжительности технического обслуживания и ремонта локомотивов
для локомотивных депо устанавливаются по согласованию с Дирекцией
тяги с отклонением не более 30 % от средних для ОАО «РЖД» норм.
Средние для ОАО «РЖД» Нормы продолжительности технического обслуживания и ремонта локомотивов см. в прил. 4.
3.2. Система обслуживания и ремонта вагонов
На железных дорогах России действует система ремонта вагонов,
которой предусматривается два вида ремонта: 1) ремонт по техническому состоянию вагона и 2) планово-предупредительный ремонт.
Ремонт по техническому состоянию вагона направлен на устранение неисправностей, выявленных при его техническом обслуживании.
Такой ремонт принято называть текущим. В зависимости от условий, при
которых выявлены неисправности грузового вагона, различают три вида
текущих ремонтов:
1) ТО – техническое обслуживание грузовых вагонов в поездах без
отцепки их от состава;
2) текущий ремонт (ТР-1) порожних вагонов, осуществляемый при
комплексной подготовке их к перевозкам с отцепкой от состава и подачей на специализированный ремонтный путь;
3) текущий ремонт (ТР-2) вагонов с отцепкой их от транзитных, прибывших или сформированных составов.
29
Техническое обслуживание пассажирских вагонов состоит из: технического обслуживания (ТО-1) вагонов в поездах, на пунктах технического
обслуживания (ПТО) станций формирований и оборота пассажирских
поездов перед каждым отправлением в рейс, а также в пути следования.
Техническое обслуживание (ТО-2) вагонов перед началом летних и
зимних перевозок в пунктах формирования пассажирских поездов.
Техническое обслуживание (ТО-3) – единая техническая ревизия основных узлов пассажирских вагонов. ТО-3 производится для купейных,
некупейных и межобластных вагонов через 150 тыс. км пробега, но не
более чем через шесть месяцев.
Планово-предупредительный ремонт направлен на устранение неисправностей вагона, накопленных в процессе эксплуатации, а также на
частичную его модернизацию в соответствии с изменившимися условиями эксплуатации. В зависимости от объема ремонтных работ различают деповской и капитальный ремонты.
Деповской ремонт (ДР) выполняется на специализированных линейных предприятиях вагонного хозяйства и предназначен для восстановления работоспособности вагона с заменой или ремонтом отдельных
деталей и узлов.
Капитальный ремонт (КР) грузовых вагонов выполняется на специализированных вагоноремонтных заводах или депо и предназначен для
восстановления ресурса вагона, близко к полному, а при необходимости
и его модернизации в целях продления полезного использования (КРП).
Периодичность технического обслуживания и ремонта грузовых и пассажирских вагонов регламентирована Положениями ОАО «РЖД» № 15 от
13.01.11 г., № 54 от 17.10.12 г., которые представлены в прил. 5–9.
Необходимо отметить, что до недавнего времени критерием изъятия
вагона из эксплуатации и подачи его в ремонт (деповской или капитальный) являлся календарный период эксплуатации от постройки или
предыдущего ремонта.
Отметим, что сама по себе система планово-предупредительного
ремонта вагонов (не по их техническому состоянию) является прогрессивной и позволяет поддерживать безопасность движения поездов на
высоком уровне. Однако принцип подачи вагонов в ремонт по истечении
определенного срока не учитывает интенсивность эксплуатации и объем
работы, выполненный вагоном за межремонтный период. Это приводит к
тому, что поступающие в ремонт однотипные вагоны могут нуждаться в
существенно различных объемах ремонта.
При подаче вагонов в ремонт учитывают не только межремонтный
срок, но и общий пробег вагона.
Например, основанием для подачи грузового вагона в деповский ремонт, после деповского ранее чем через 2 года, является общий пробег,
тыс. км: платформы – 110; полувагоны, цистерны и остальной парк – 100.
Общий пробег до деповского ремонта после капитального для всех ти30
пов вагонов установлен 160 тыс. км. Деповской ремонт после постройки
и капитально-восстановительного ремонта (КВР) производится после
пробега 210 тыс. км, но не более чем через 3 года.
Подача пассажирских вагонов в деповской ремонт производится после пробега 300 тыс. км, но не более чем через 2 года. Данные о пробеге
вагона получают по справке № 2610 Главного вычислительного центра
(ГВЦ) ОАО «РЖД» России.
При регламентации межремонтных пробегов вагонов нового поколения
в качестве ориентиров могут быть приняты их показатели надежности.
Например, для вагона-углевоза модели 3111 производства Брянского
машиностроительного завода (АО «УК «БМЗ»») установлены следующие
показатели надежности: назначенный срок службы до первого капитального ремонта – 13 лет; назначенный пробег (межремонтный период) от постройки и от капитального ремонта до первого деповского ремонта –
500 тыс. км, но не более 4 лет; назначенный пробег (срок) между деповскими ремонтами в период эксплуатации до капитального ремонта –
450 тыс. км, но не более 3 лет; назначенный пробег (срок) между деповскими ремонтами в период эксплуатации после капитального ремонта –
400 тыс. км, но не более 3 лет.
Отметим, что общий пробег вагона тоже не может объективно характеризовать степень износа вагона, поскольку интенсивность изнашивания существенно зависит от того, в каком виде вагон следует в составе –
груженом или порожнем. Развитие информационных систем на железнодорожном транспорте позволяет учитывать и груженый, и порожний
пробег по каждому вагону. Следовательно, можно рекомендовать принимать в качестве критерия подачи вагона в очередной ремонт некоторый приведенный пробег, определяемый как сумма груженого и порожнего пробега, взятого с поправочными коэффициентом:
Ппр Пгр k Ппор ,
(3.1)
где k – коэффициент приведения порожнего пробега к груженому, определяемый опытным путем по средней интенсивности изнашивания деталей и узлов вагона.
3.3. Объемы работ, выполняемых при техническом обслуживании
и ремонте локомотивов
Система технического обслуживания и ремонта локомотивов предусматривает следующие виды планового технического обслуживания и
ремонта14:
14
Распоряжение о системе технического обслуживания и ремонта локомотивов
ОАО «РЖД»: № 1651р : утв. ОАО «РЖД» 21.009.18 : введ. в действие с 21.09.18. М.:
ОАО «РЖД», 2018. 10 с.
31
а) техническое обслуживание ТО-1;
б) техническое обслуживание ТО-2;
в) техническое обслуживание ТО-3;
г) техническое обслуживание ТО-4;
д) техническое обслуживание ТО-5 (а, б, в, г);
е) текущий ремонт ТР-1;
ж) текущий ремонт ТР-2;
з) текущий ремонт ТР-3;
и) средний ремонт СР;
к) капитальный ремонт КР.
Техническое обслуживание ТО-1 выполняется локомотивной бригадой при приемке-сдаче и экипировке локомотива, при остановках на железнодорожных станциях. По отметкам в журнале формы ТУ-152 принимающая локомотив бригада обязана убедиться в соблюдении установленной периодичности технического обслуживания ТО-2, проверки
АЛСН, КЛУБ, САУТ и радиосвязи, ознакомиться с замечаниями локомотивной бригады, сдающей локомотив, и с записями о выполнении ремонта по этим замечаниям.
Техническое обслуживание ТО-2 выполняется работниками в пунктах
технического обслуживания локомотивов (ПТОЛ) с участием работников
других служб для выполнения работ по оснащению устройств АЛСН,
КЛУБ и устройств безопасности. Пункт технического обслуживания
(ПТО) оснащается в соответствии с утвержденным регламентом необходимым оборудованием, (переносными средствами контроля и диагностирования), инструментом и приспособлениями, обеспечивается технологическим запасом деталей, приборов и материалов.
При техническом обслуживании ТО-3 (для тепловозов) при работающем дизеле проверяется: частота вращения коленчатых валов дизелей на всех позициях рукоятки контроллера; срабатывание предельного
регулятора дизеля; исправность работы автоматики системы охлаждения, вращение колеса воздухоочистителя при работе компрессора на
холостом ходу; давление масла в системе смазки дизеля при постановке
и выпуске тепловоза из технического обслуживания ТО-3; срабатывание
предохранительного устройства при нажатии кнопки аварийной остановки дизеля; работа и исправность действия системы аварийного питания
дизеля топливом; срабатывание реле боксования и действие сигнализации поочередным включением тяговых электродвигателей в режиме тяги; срабатывание реле заземления созданием искусственного замыкания на корпус. Кроме того, производится безреостатная диагностика систем возбуждения и автоматики. Замеряется величина наддува вентиляторов охлаждения ТЭД. Проверяется отсутствие нагрева подшипни-
32
ковых узлов вспомогательных электрических машин и производится их
диагностика при наличии соответствующего оборудования.
При техническом обслуживании ТО-4 производится обточка колесных пар без выкатки из-под локомотива. Обточенные колесные пары
должны соответствовать требованиям действующей инструкции по
формированию, ремонту и содержанию колесных пар тягового подвижного состава железных дорог колеи 1520 мм15.
После обточки проверяется состояние осевых упоров при их установке, добавляется смазка в буксы.
Обточка колёсных пар по возможности должна совмещаться с техническим обслуживанием ТО или текущим ремонтом ТР.
Техническое обслуживание ТО-5а проводится с целью подготовки
локомотива к постановке в запас или в резерв железной дороги.
Техническое обслуживание ТО-5б проводится с целью подготовки
локомотива к отправке в недействующем состоянии.
Техническое обслуживание ТО-5в проводится с целью подготовки к эксплуатации локомотива, прибывшего в недействующем состоянии, после
постройки, после ремонта вне локомотивного депо приписки или после
передислокации.
Техническое обслуживание ТО-5г проводится для подготовки локомотива к эксплуатации после содержания в запасе (резерве железной дороги).
При текущем ремонте ТР-1 (для тепловозов) выполняются все работы, предусмотренные техническим обслуживанием ТО-3, а также дополнительно осуществляется ревизия и необходимый ремонт дизеля,
вспомогательного оборудования, электрического оборудования, экипажа
и приборов безопасности.
При текущем ремонте ТР-1 (для электровозов) выполняются работы
по вспомогательным машинам, масляному насосу, тормозам, песочницам,
звуковым сигналам, напору и распределению воздуха по тяговым двигателям (при подготовке к летним перевозкам). При каждом ТР-1 выполняются
все работы, предусмотренные ТО-2.
При текущих ремонтах ТР-2 и ТР-3 (для тепловозов) выполняются
все работы в объеме ТР-1 и дополнительно работы по дизелю, вспомогательному оборудованию, электрическому оборудованию и экипажу,
автоматическому гребнесмазывателю (АГС)
При текущих ремонтах ТР-2 и ТР-3 (для электровозов) выполняются
работы, предусмотренные в объеме ТР-1, и дополнительные работы по
экипажу, автосцепным и поглощающим устройствам, гидродемпферам, токоотводящим устройствам, тормозному оборудованию, электрооборудованию и электрическим машинам, тормозным компрессорам, АГС.
15
Инструкция по осмотру, освидетельствованию, ремонту и формированию колесных пар локомотивов и моторвагонного подвижного состава железных дорог колеи 1520:
ЦТ-329 : утв. ОАО «РЖД» 22.12.16 : введ. в действие с 22.12.16. М.: ОАО «ВНИИЖТ»,
2016. 121 с.
33
При средних ремонтах СР (для тепловозов) выполняются следующие объемы работ:
1) по дизелю и вспомогательному оборудованию: полная разборка
дизеля с проверкой, ремонтом и восстановлением изношенных и заменой
негодных узлов и деталей; проверка и восстановление постелей подшипников коленчатых и кулачковых валов, посадочных мест в блоке дизеля
под цилиндровые гильзы, вертикальную передачу и толкатели топливных
насосов; шлифовка и полировка шеек коленчатых валов по размерам ремонтных градаций; замена цилиндровых гильз, шатунных и коренных
вкладышей, поршневых колец независимо от состояния; разборка и ремонт с восстановлением изношенных и заменой негодных деталей вертикальной передачи, антивибратора, шатунно-поршневой группы, топливной аппаратуры, турбокомпрессоров, масляных и водяных насосов и их
эластичных приводов, механизма управления дизелем, регулятора частоты вращения дизеля, воздухоохладителя; ремонт масляных и топливных фильтров с заменой фильтрующих элементов; ремонт муфты соединения дизеля и генератора; разборка, ремонт и замена негодных узлов
холодильного устройства, вентиляторов, терморегуляторов, коллекторов,
секций, вентиляторов охлаждения тяговых электродвигателей; ремонт
теплообменника и топливоподогревателя; ремонт или замена негодных
деталей регулятора частоты вращения дизеля и рычажной системы топливных насосов; разборка, ремонт и опрессовка масляного, водяного и
топливного трубопровода с заменой негодных труб; замена асбестовых,
резиновых, паронитовых и других уплотнений независимо от их состояния; очистка, ремонт и испытание водяных и топливных баков;
2) по кузову и раме тепловоза: проверка и ремонт рамы с заменой негодных деталей; ремонт автосцепных устройств в соответствии с инструкцией16; ремонт кузова с заменой негодных частей обшивки, поручней,
лестниц, люков, окон, дверей, полов; ремонт внутренней обшивки кабины
машиниста, съемной части кузова и холодильной камеры, тепло- и звукоизоляции кабины машиниста, окон и дверей с заменой негодных деталей;
ремонт путеочистителей; удаление разрушившегося лакокрасочного покрытия в местах, подверженных механическим и другим видам повреждения; восстановление антикоррозийных покрытий всех элементов кузова;
3) по тележкам: выкатка, очистка разборка, проверка и ремонт рамы
тележки со снятием всего оборудования; ремонт, сборка и обкатка колесно-моторного блока; ремонт кожухов тягового редуктора; полное
освидетельствование и ремонт колесных пар; дефектация, ремонт и
сборка букс; ремонт рессорного подвешивания с тарировкой цилиндрических пружин, заменой пружин, не удовлетворяющих требованиям чертежей и руководства; ремонт или замена на новые деталей тормозной
16
Инструкция по ремонту и обслуживанию автосцепного устройства подвижного состава железных дорог : № 2746р: утв. Советом по ж.-д. трансп. Государств-участников
Содружества 20.10.10 : введ. в действие с 28.12.10. М.: ОАО «ВНИИЖТ», 2010. 68 с.
34
рычажной передачи; ремонт подвесок тяговых двигателей; окраска тележек; ремонт и восстановление или замена на новые деталей гасителей
колебаний; ремонт и восстановление или замена на новые деталей узла
смазки гребней АГС; сборка и проверка тележек;
4) по электрическим аппаратам и электрической проводке: снятие,
очистка, разборка, ремонт, регулировка, проверка и испытание всех
электрических устройств и аппаратов, в том числе штепселей и розеток
межсекционных соединений с заменой негодных элементов аппаратов,
шунтов, полупроводниковых элементов, датчиков, катушек и других деталей; изношенных более допустимых пределов контактов электрических аппаратов; замена негодной низковольтной и высоковольтной проводки; установка новых аккумуляторных батарей;
5) разборка, очистка, ремонт и испытание всего тормозного оборудования, воздушных резервуаров в соответствии с инструкцией17;
6) по оборудованию общего назначения: ремонт и испытание автоматической локомотивной сигнализации, автостопов, приборов бдительности, скоростемеров; демонтаж и монтаж оборудования систем КЛУБ-У
и автоведения; демонтаж, ремонт и монтаж оборудования унифицированного пульта управления.
При средних ремонтах СР (для электровозов) выполняются следующие объемы работ:
1) по тележкам: выкатка, очистка, разборка, проверка и ремонт рам
со снятием всего оборудования; ремонт сочленения с восстановлением
или заменой деталей; ремонт резиновых уплотнителей опор и возвращающих устройств с заменой резинометаллических изделий (сайлентблоков); ремонт рессорного подвешивания с переборкой листовых и тарификацией цилиндрических рессор или заменой листовых и цилиндрических рессор, заменой изношенных втулок и восстановлением или заменой валиков новыми (при этом производится измерение высоты рессор и пружин в свободном состоянии и под рабочей нагрузкой); ремонт и
восстановление или замена на новые деталей тормозной рычажной передачи; ремонт автосцепных устройств; сборка и окраска тележек;
2) по кузову: ревизия и ремонт шкворней, ремонт шаровой связи и
гидравлических гасителей колебаний; осмотр и проверка рамы, стен,
крыши, жалюзи, люков, окон, дверей, лестниц, поручней, полов и обшивки кабин, каркасов под аппараты и оборудование с устранением дефектов; наружная и внутренняя окраска кузова и кабин с удалением старой
краски (при наличии коррозии и отслоившейся краски); ремонт системы
гребнесмазывателей;
17
Инструкция по техническому обслуживания, ремонту и испытанию тормозного
оборудования локомотивов и моторвагонного подвижного состава : ЦТ-533 : утв.
МПС Рос. Федерации 27.01.98 : введ. в действие с 27.01.98. М.: ПКБ ЦТ, 1998. 88 с
35
3) полное освидетельствование и ремонт колесных пар в соответствии с инструкцией18;
4) ремонт электрических машин в соответствии с руководством19;
5) ремонт буксовых узлов и агрегатов с подшипниками качения в
соответствии с инструкцией20;
6) по электрическим аппаратам и электрической проводке: снятие,
очистка, разборка, ремонт, регулировка, проверка и испытание всех
электрических устройств и аппаратов, в том числе штепселей и розеток
межсекционных соединений с заменой негодных деталей; установка новых аккумуляторных батарей;
7) разборка, очистка, ремонт и испытание всего тормозного оборудования, воздушных резервуаров в соответствии с инструкцией;
8) разборка, ремонт и испытание устройств автоматической локомотивной сигнализации и автостопов, скоростемеров, дополнительных устройств безопасности движения;
9) ремонт и проверка действия всех защитных устройств.
При капитальных ремонтах КР (для тепловозов) выполняются
все работы, предусмотренные средним ремонтом и дополнительно производятся следующие работы:
1) замена внутренней обшивки кабины машиниста, тепло- и звукоизоляции в кабине машиниста, пола кабины машиниста независимо от
состояния;
2) полная очистка от старой краски и ржавчины наружной поверхности
кузова;
3) полная замена низковольтной и высоковольтной проводки;
4) очистка воздухопроводов с заменой негодных труб и соединений;
5) замена поршней дизеля;
6) снятие и ремонт топливного бака.
При капитальных ремонтах КР (для электровозов) выполняются
все работы, предусмотренные средним ремонтом и дополнительно производятся следующие работы:
1) ремонт опор кузова с выпрессовкой и заменой (при наличии
сверхдопустимых износов, трещин, изгибов) шкворней;
2) восстановление или замена изношенных частей рамы, каркасов и
обшивки;
18
Инструкция по осмотру, освидетельствованию, ремонту и формированию
колесных пар локомотивов и моторвагонного подвижного состава железных дорог
колеи 1520 : ЦТ-329 : утв. ОАО «РЖД» 22.12.16 : введ. в действие с 22.12.16. М.:
ОАО «ВНИИЖТ», 2016. 121 с.
19
Руководство по среднему и капитальному ремонту электрических машин электровозов : РД 103.11.320-2004 : утв. ОАО «РЖД» 15.06.04 : введ. в действие с
15.06.04. М.: ОАО «Желдорреммаш, 2005. 243 с.
20
Инструкция по техническому обслуживанию и ремонту узлов с подшипниками
качения локомотивов и моторвагонного подвижного состава : ЦТ-330 : утв. МПС Рос.
Федерации 11.07.95 : введ. в действие с 11.07.95. М.: ПКБ ЦТ, 1995. 73 с.
36
3) полная очистка от старой краски и ржавчины наружной поверхности
кузова. Восстановление антикоррозийных покрытий всех элементов кузова;
4) полная разборка внутренней обшивки и полов кабин с заменой
теплоизоляции. Ремонт оконных блоков и дверей кабин;
5) полная разборка и очистка воздухопроводов с заменой негодных
труб и соединений. Гидравлические испытания воздухопроводов тормозной и питательной магистралей в соответствии с инструкцией21;
6) полная замена высоковольтных и низковольтных проводов.
3.4. Объемы работ, выполняемых
при техническом обслуживании и ремонте вагонов
Система технического обслуживания и ремонта вагонов предусматривает следующие виды планового технического обслуживания и ремонта22, 23:
а) техническое обслуживание ТО;
б) техническое обслуживание с диагностированием ТОД;
в) текущий отцепочный ремонт ТР подразделяющийся:
1) на текущий отцепочный ремонт ТР-1;
2) текущий отцепочный ремонт ТР-2;
г) деповской ремонт ДР;
д) капитальный ремонт КР;
е) капитальный ремонт с продлением срока службы КРП.
Техническое обслуживание ТО – комплекс операций или операция по
поддержанию работоспособности или исправности вагона в сформированных или транзитных поездах, а также порожнего вагона при подготовке к перевозкам без его отцепки от состава или группы вагонов.
Техническое обслуживание с диагностированием ТОД – комплекс
операций по инструментальному контролю технического состояния составных частей вагона с использованием диагностических средств, переводу вагонов в нерабочий парк и подаче их на специализированные пути.
21
Инструкция по техническому обслуживанию и ремонту узлов с подшипниками
качения локомотивов и моторвагонного подвижного состава : ЦТ-330 : утв. МПС Рос.
Федерации 11.07.95 : введ. в действие с 11.07.95. М.: ПКБ ЦТ, 1995. 73 с.
22
Положение о системе технического обслуживания и ремонта грузовых вагонов, допущенных в обращение на железнодорожные пути общего пользования в международном обращении : протокол № 54 : утв. Советом по ж.-д. трансп. государств-участников
Содружества 17.10.12 : введ. в действие с 17.10.12. М.: ОАО «ВНИИЖТ», 2012. 19 с.
23
Положение о внесение изменений в приказ Министерства путей сообщения Российской Федерации от 4 апреля 1997 г. № 9Ц «О введении новой системы технического
обслуживания и ремонта пассажирских вагонов» : протокол № 15 : утв. М-вом трансп.
Рос. Федерации 13.01.11 : ввод. в действие с 13.01.11. М.: ОАО «ВНИИЖТ», 2011. 14 с.
37
Текущий отцепочный ремонт ТР – ремонт, выполняемый для обеспечения или восстановления работоспособности вагона с заменой или
восстановлением отдельных составных частей, отцепкой от состава или
группы вагонов, с переводом их в нерабочий парк и подачей на специализированные пути.
Текущий отцепочный ремонт ТР-1 – ремонт порожнего вагона, выполняемый при его подготовке к перевозке с отцепкой от состава или
группы вагонов.
Текущий отцепочный ремонт ТР-2 – ремонт в целях восстановления
работоспособности груженого или порожнего вагона, с отцепкой от транзитных и прибывших в разборку поездов или сформированных составов.
Деповской ремонт ДР – ремонт, выполняемый для восстановления
исправности и частичного восстановления ресурса вагона с заменой или
восстановлением составных частей ограниченной номенклатуры и контролем технического состояния составных частей.
Капитальный ремонт КР – ремонт, выполняемый для восстановления
исправности полного или близкого к полному восстановлению ресурса вагона, с заменой или восстановлением любых его частей, включая базовые.
Капитальный ремонт с продлением срока службы КРП – контроль
технического состояния всех несущих элементов конструкции вагона с
восстановлением их назначенного ресурса, заменой или восстановлением любых его составных частей, включая базовые, и назначением нового срока службы.
3.5. Основная техническая документация
по техническому обслуживанию
и ремонту локомотивов и вагонов
При техническом обслуживании, текущем и деповском ремонтах локомотивов (вагонов) и их сборочных единиц руководствуются технологическими инструкциями (картами), процессами по восстановлению поврежденных деталей, разработанными Проектно-конструкторскими бюро
локомотивного и вагонного хозяйства ОАО «РЖД» (ПКБ ЦТ и ПКБ ЦВ
ОАО «РЖД»)24. При этом, перечень нормативно-технической документации по вагонному хозяйству, структурированный в соответствии с классификацией, утвержденной распоряжением ОАО «РЖД» от 7 марта 2017 г.
№ 418р «Об утверждении Порядка управления жизненным циклом документов технического характера в ОАО «РЖД».
24
Руководство по техническому обслуживанию и текущему ремонту тепловозов
2ТЭ116: ТЭ116 ИО : утв. ОАО «РЖД» 31.12.04 : введ. в действие с 31.12.04. М.: ПКБ ЦТ,
2004. 320 с.
38
Данные по измерениям, о замене и модернизации основных сборочных единиц записываются в техническом паспорте (в формуляре сборочной единицы) локомотива (вагона)25, 26:
а) ТУ-23 – предварительная опись состояния локомотива;
б) ТУ-25 – акт проверки технического состояния локомотива, мотор–
вагонного подвижного состава, крана, предназначенных для пересылки
в недействующем состоянии;
в) ТУ-27 – книга регистрации ремонта, технического обслуживания и
учета пробега локомотивов, моторвагонного подвижного состава между
всеми видами ремонта и технического обслуживания
г) ТУ-28 – объем ремонта с учетом замечаний прибывшей локомотивной бригады, записанный в журнале технического состояния локомотива (форма ТУ-152);
д) ТУ-29 – сведения о повреждениях и отказах сборочных единиц;
е) ТУ-31 – акт о готовности локомотива к эксплуатации после текущего и деповского ремонта;
ж) ВУ-23М – уведомление на ремонт грузовых вагонов;
з) ВУ-25М – акт о повреждении вагона;
и) ВУ-27ВЦ – акт о техническом состоянии вагона;
к) ВУ-32 – журнал приемки отремонтированных тележек грузовых вагонов.
В целях повышения технического уровня и укрепления ремонтной
базы локомотивных депо, выполняющих техническое обслуживание, текущие ремонты и ремонт в объеме СР магистральных и маневровых
тепловозов, электровозов постоянного и переменного тока, вагонов
ПКБ ЦТ и ПКБ ЦВ ОАО РЖД разработаны и утверждены технические регламенты технологического оснащения локомотивных депо27, 28.
Технические регламенты устанавливают требования к оснащенности
предприятий основным специализированным технологическим оборудованием и средствами диагностики. Ими следует руководствоваться при оцен-
25
Распоряжение об утверждении внутренних форм первичного учета ОАО «РЖД» в
локомотивном хозяйстве : № 2531р : утв. ОАО «РЖД» 11.12.09 : введ. в действие с
11.12.09. М.: ОАО «РЖД», 2009. 12 с.
26
Распоряжение об оптимизации технологии подготовки и передачи учетноотчетных форм в вагонном хозяйстве : № 785р : утв. ОАО «РЖД» 24.04.06 : введ. в
действие с 24.04.06. М.: ОАО «РЖД», 2006. 9 с.
27
Проектно-конструкторское бюро локомотивного хозяйства – филиал открытого
акционерного общества «Российские железные дороги»: перечень технической документации [Электронный ресурс]. М.: ПКБ ЦТ. Режим доступа: http://www.pkbct.ru.
28
Проектно-конструкторское бюро вагонного хозяйства – филиал открытого акционерного общества «Российские железные дороги»: перечень технической документации [Электронный ресурс]. М.: ПКБ ЦВ. Режим доступа: http://www.pkbcv.ru.
39
ке технологической оснащенности ремонтных предприятий, а также при выполнении проектных работ по реконструкции и новому строительству.
По своему составу документы выполнены в виде перечня оборудования, средств диагностики и приборов. В перечне, который представляет
собой таблицу, указаны наименование технологических операций и основное оборудование, необходимое для их выполнения, а также разработчик и изготовитель (поставщик) оборудования.
По мере уточнения и дополнения перечня работ по ремонтам и техническому обслуживанию, разработки передовых технологий и внедрения прогрессивного технологического оборудования и средств диагностики в регламенты должны быть внесены изменения.
ВОПРОСЫ ДЛЯ САМОКОНТРОЛЯ
1. Что понимается под планово-предупредительной системой технического обслуживания и ремонта локомотивов?
2. Дайте определения понятиям «плановый ремонт» и «неплановый
ремонт» локомотивов.
3. Назовите виды и сроки периодичности технического обслуживания
и ремонта локомотивов. Какова их значимость?
4. Назовите нормы продолжительности простоя и трудоемкости технического обслуживания и ремонта для локомотивов.
5. Назовите виды и назначение видов ремонта для вагонов.
6. Какова периодичность технического обслуживания и ремонта грузовых и пассажирских вагонов?
7. Каковы объемы работ, выполняемых при техническом обслуживании и ремонте локомотивов?
8. Каковы объемы работ, выполняемых при техническом обслуживании и ремонте вагонов?
9. Назовите основную техническую документацию по техническому
обслуживанию и ремонту локомотивов и вагонов.
Рекомендуемая литература: [1–32, 34–36] (см. Библиографический список).
40
4. ОСНОВЫ ТЕХНОЛОГИИ РЕМОНТА
СБОРОЧНОЙ ЕДИНИЦЫ ЛОКОМОТИВА И ВАГОНА
4.1. Основные термины и определения показателей
для описания технического обслуживания
и ремонта подвижного состава
Показатели технического обслуживания и ремонта подвижного состава, эксплуатируемого на железнодорожных путях общего и необщего
пользования, описываются следующими терминами и определениями29:
проверка (осмотр) – это комплекс операций или операция по
определению состояния или положения деталей, проводников, подвижных и неподвижных соединений (включая контактные), изоляции и т. п. в
сборочных единицах или состояния самих сборочных единиц подвижного состава путем визуального осмотра (по внешним признакам), отстукивания, по показаниям приборов, воздействия на органы управления, измерения отдельных параметров;
дефектация – комплекс операций или операция по выявлению
дефектов (повреждений) деталей, проводников, подвижных и неподвижных соединений, изоляции и т. п. в собранных, частично или полностью
разобранных сборочных единицах, с применением соответствующих
технологических средств (измерительные инструменты, стенды, средства технической диагностики и вычислительной техники);
ревизия – это комплекс операций или операция по определению
состояния или положения деталей, проводников, подвижных и неподвижных соединений, изоляции, смазки и т. п. в сборочных единицах или
их положения на подвижном составе с применением соответствующих
технологических средств (инструменты, приспособления и т. п.). В ревизию могут входить операции по частичной разборке и сборке сборочной
единицы, съёмке крышек, люков, операции по устранению незначительных дефектов и повреждений, смене смазки и т. п.;
ремонт – комплекс операций по восстановлению исправности или
работоспособности подвижного состава. В ремонт могут входить операции по проверке, дефектации, ревизии, разборке, очистке, восстановлению, сборке, смазке, испытанию и т. д., деталей и сборочных единиц.
Содержание части операции ремонта может совпадать с содержанием
некоторых операций проверки, дефектации и ревизии;
диагностирование – процесс определения технического состояния объекта (обнаружение и поиск дефектов) с помощью приборов без
его разборки;
29
Гапанович В.А., Андреев В.Е., Митрохин Ю.В., Яговкин А.Н., Иванов К.В. Эксплуатация и техническое обслуживание подвижного состава: учеб. пособие для вузов
ж.-д. транспорта / под общ. ред. В.А. Гапановича. М.: «ИРИС ГРУПП», 2012. 572 с.
41
освидетельствование – система проверки технического состояния объекта на соответствие установленным требованиям;
дефект – каждое отдельное несоответствие объекта установленным требованиям;
деталь – изделие, изготовленное из одного по наименованию и
марке материала без применения сборочных операций;
исправная деталь – деталь, состояние которой удовлетворяет
требованиям соответствующей технической документации, пригодная
для дальнейшей работы без какого-либо ремонта и испытаний;
неисправная деталь – деталь, требующая ремонта или проверки,
состояние которой не отвечает требованиям соответствующей инструкции;
негодная деталь – деталь, имеющая дефект, исправление которого запрещено правилами ремонта;
объект ремонта (ОР) – подвижной состав, либо его сборочная
единица, или деталь, подвергающаяся ТО или ремонту;
сборочная единица (СЕ) – изделие, составные части которого соединены между собой сборочными операциями (свинчивание, сварка,
напрессовка): с разъемными подшипниками скольжения и качения; неразъемными подшипниками скольжения; с цилиндрическими деталями,
движущимися возвратно-поступательно; с резиново-металлическими деталями и сальниковыми уплотнениями. Соединения разделяются на резьбовые, прессовые, конусные неподвижные, конусные подвижные, шлицевые,
шпоночные, паяные, сварные, зубчатые, и т. п.;
исправное состояние подвижного состава – состояние подвижного состава, при котором он соответствует всем требованиям нормативной
и (или) технической документации на этот подвижной состав;
неисправное состояние подвижного состава – состояние подвижного состава, при котором он не соответствует хотя бы одному из
требований нормативной и (или) технической документации на этот подвижной состав;
работоспособное состояние подвижного состава (составной части подвижного состава) – состояние подвижного состава (составной части подвижного состава), при котором он способен выполнить
все предусмотренные техническими требованиями функции в полном
объеме при условии, что предоставлены необходимые ресурсы;
частично работоспособное состояние подвижного состава
(составной части подвижного состава) – состояние подвижного состава (составной части подвижного состава), при котором он не способен
выполнить хотя бы одну из предусмотренных техническими требованиями
функций в полном объеме;
42
неработоспособное состояние подвижного состава (составной части подвижного состава) – состояние подвижного состава (составной части подвижного состава), при котором он не способен выполнить
все предусмотренные техническими требованиями функции;
неработоспособное состояние подвижного состава по внутренним ресурсам – неработоспособное состояние подвижного состава,
при котором он не способен выполнить требуемую функцию из-за внутренней неисправности или профилактического технического обслуживания;
неработоспособное состояние подвижного состава по внешним ресурсам – неработоспособное состояний подвижного состава, при
котором он не способен выполнить требуемую функцию из-за отсутствия
или нехватки внешних ресурсов;
предельное состояние подвижного состава – состояние подвижного состава, при котором его дальнейшая эксплуатация недопустима
и восстановление его работоспособного состояния невозможно30.
4.2. Технологический процесс ремонта сборочной единицы
Технологический процесс ремонта СЕ можно представить в виде
следующей схемы (рис. 4.1)31.
Ремонт СЕ
Очистка СЕ
Разборка СЕ
Очистка деталей
Контроль (дефектация) деталей
Детали, требующие ремонта
Годные детали
Участок восстановления деталей
Комплектование
Негодные
детали
Склад утиля
Складирование
Сборка СЕ
Готовые запасные части
Приемка СЕ
Рис. 4.1. Схема ремонта сборочной единицы
30
ГОСТ Р 56046-2014. Показатели использования локомотивов. Термины и определения : введ. 11.06.2014. М.: Изд-во стандартов, 2014. 28 с.
31
Гапанович В.А., Андреев В.Е., Митрохин Ю.В., Яговкин А.Н., Иванов К.В. Эксплуатация и техническое обслуживание подвижного состава: учеб. пособие для вузов
ж.-д. транспорта / под общ. ред. В.А. Гапановича. М.: «ИРИС ГРУПП», 2012. 572 с.
43
Прежде чем приступить к разборке локомотива (вагона), полезно
вспомнить о маркировке, о том, что нужно проверить перед съемкой и
разборкой любого объекта ремонта и почему нельзя обезличивать детали отдельных соединений32.
Маркировка. Локомотив (вагон) состоит из десятков тысяч деталей.
В процессе его сборки многие детали подбирают по весу и размерам,
часть деталей совместно обрабатывают, а некоторые, кроме того, прирабатывают друг к другу; при соединении двух агрегатов их валы центрируют, т. е. делают соосными; взаимное расположение ряда деталей
регулируют прокладками, большинство механизмов после установки
фиксируют штифтами. Для того чтобы в процессе последующей сборки
быстро распознать место, ранее занимаемое той или другой деталью,
одноименные и комплектные детали маркируют, т. е. наносят на них
особые метки (знаки, цифры, буквы и т. п.).
Например, маркировка АБ9 на гильзе цилиндра означает, что она
принадлежит девятому цилиндру дизеля АБ; маркировка АВ8НГ на
вкладыше коренного подшипника коленчатого вала указывает на то, что
он относится к дизелю АВ, восьмому подшипнику его нижнего вала и является верхним вкладышем. Система маркировки каждой машины или
механизма приводится в технической документации, а места постановки
маркировки указываются на чертежах деталей или узлов.
Технологический процесс съемки и разборки. В процессе съемки
и разборки производят внешний осмотр, определяют положение деталей в собранном узле, собственно съемку и разборку.
Внешний осмотр нужен для проверки наличия маркировки, определения надежности посадки и состояния деталей по видимым признакам. Если на деталях знаков маркировки в местах, предусмотренных
чертежом, почему-либо нет или они перепутаны, их наносят тотчас же
после разборки объекта33.
Часто нарушение посадки и неисправности деталей удается определить до разборки объекта по внешним признакам.
Например, об ослаблении посадки вкладышей подшипника коленчатого вала дизеля можно судить по смещению разъемов вкладышей и
гнезда подшипника. Слабо укрепленную или плохо уплотненную катушку
на сердечнике полюса электрической машины определяют по следам
32
Данковцев, В.Т., Киселев В.И., Четвергов В.А. Техническое обслуживание и
ремонт локомотивов: учеб. для студентов вузов ж.-д. трансп. М.: Учеб.-метод. центр
по образованию на ж.-д. трансп., 2007. 557 с.
33
Мотовилов К.В., Лукашук В.С., Криворудченко В.Ф., Петров А.А. Технология производства и ремонта вагонов / под ред. К.В. Мотовилова. М.: Маршрут, 2003. 382 с.
44
смещения (натертости), а также по наличию ржавчины на металлических
деталях или поверхности самой катушки. Обугленная изоляция – признак ослабшего контактного соединения. Скопление пыли в виде жилки
или небольшого валика на поверхности деталей (особенно экипажной
части) укажет на наличие трещины или ослабление посадки детали.
Жилка в этом случае будет как бы обрисовывать контур трещины.
Определение положения деталей в собранном узле. Наиболее достоверные данные о величинах зазоров и разбегов между трущимися деталями, об искажении их формы, деформации и износе можно получить
лишь тогда, когда измерения ведутся при рабочем положении деталей34.
Например, зазор «на масло» в подшипниках коленчатого вала дизеля,
в якорных и моторно-осевых подшипниках тягового электродвигателя, боковой зазор между зубьями различных зубчатых передач или деталями
шлицевого соединения наиболее точно можно определить в собранном
узле. Так, искажение формы постелей подшипников коленчатого вала дизеля или моторно-осевых подшипников тягового электродвигателя можно
установить лишь в том случае, когда крышки подшипников нормально закреплены на своих местах. О деформации гильзы цилиндра дизеля можно
достоверно судить лишь при нахождении ее в блоке цилиндров. Внешний
осмотр и определение положения деталей в собранном узле являются одними из элементов технической диагностики объекта ремонта.
Съемка и разборка объекта. Трудоемкость разборочных и сборочных работ составляет значительную часть (примерно 35–45 %) от общей
трудоемкости ремонта ТР-З (для локомотивов) и ДР (для вагонов). Эта
цифра заметно уменьшается, когда сокращается число пригоночных работ, отпадает необходимость восстановления поврежденных при разборке деталей, поиске потерянных крепежа, прокладок и т. п. Поэтому
правильная организация процессов съемки и разборки, а также качественное их выполнение оказывают весьма заметное влияние на продолжительность, трудоемкость и стоимость ремонта тепловоза.
При демонтаже или разборке объекта ремонта необходимо придерживаться следующих правил. Начнем с инструмента. Он должен быть по
возможности механизированным и универсальным, удобным и безопасным в эксплуатации, обязательно исправным, обеспечивающим сохранность деталей. Выколотки желательно применять из алюминия, красной
меди или фибры.
Несколько рекомендаций по разборке объекта. Во всех случаях,
когда это возможно, объект ремонта до поступления на рабочее место
нужно очистить, что создаст благоприятные условия для дальнейшей работы. Регулировочные прокладки и шайбы, цилиндрические и конические
34
Мотовилов К.В., Лукашук В.С., Криворудченко В.Ф., Петров А.А. Технология производства и ремонта вагонов / под ред. К.В. Мотовилова. М.: Маршрут, 2003. 382 с.
45
штифты и т. п., служащие для фиксации или регулировки взаимного расположения деталей, следует сохранить, чтобы при последующей сборке
или монтаже объектов не производить лишних, иногда очень трудоёмких,
операций по их центровке и регулировке. При снятии люков, крышек или
крупных деталей, установленных на герметизирующих прокладках, нужно
соблюдать осторожность, чтобы обеспечить их сохранность. Открытые
полости оборудования, не снятого с локомотива (вагона), в том числе и
труб, а также полости демонтированных объектов, следует закрыть
крышками или пробками, чтобы избежать засорения. Весь годный крепёж
(гайки, болты, шпильки) по возможности вновь поместить на прежние места. Если это не удается, крепеж нужно рассортировать по размерам и
разместить в ячейках комплектовочных корзин или тележек.
Особая осторожность должна быть проявлена при разборке электрических машин. Небрежное обращение с якорем или катушками полюсов,
как правило, ведет к повреждению изоляции. Очень часто причиной
пробоя изоляции служит стальная стружка, вдавившаяся в изоляцию.
Нельзя якорь или катушку перетаскивать волоком или перекатыванием.
Для этой цели существуют простые и удобные чалочные приспособления и подставки. Разбирать объект ремонта «до винтика» не следует.
Детали неразъемных (например, клепаных) или разъемных соединений,
но с нормальной посадкой деталей нужно разбирать лишь при необходимости. Часто бывает так, что многие детали оказываются годными и
могут быть повторно использованы, а объект ремонта после сборки
установлен на свое прежнее место. Поэтому в процессе демонтажных
работ снятые детали следует размещать таким образом, чтобы после
очистки и осмотра каждую деталь можно было легко найти и поместить
на прежнее место. Эта рекомендация особенно важна для спаренных
деталей, обезличивание которых не только приводит к потере времени,
но и отрицательно влияет на долговечность работы тепловоза.
Что касается характера демонтажных работ, то, несмотря на разнообразие конструктивных элементов оборудования локомотива (вагона), они
состоят из небольшого числа повторяющихся операций. К ним следует,
прежде всего, отнести разборку резьбовых и прессовых соединений.
Схема разборки позволяет в пространстве показать последовательность работ с выполнением приемов по измерению размеров и применению специального инструмента или приспособлений (рис. 4.2).
Схему разборки можно представить в виде «дерева» из последовательно выполненных приемов, на основном стволе которого располагаются снятые детали, а на ветвях – подсборки, требующие дальнейшей
разборки. На рис. 4.2, а изображен эскиз объекта ремонта (редуктор), а
на рис. 4.2, б – схема его разборки35.
35
Там же.
46
а
13
5
17
4
9
3
1
2
10
8
15
6
11
16
7
14
12
Редуктор в сборе
б
Шкиф
1
2
Измерить боковой зазор
между шестернями,
пометить зубья
Фланец
2
3, 8
Вал ведущий
в сборе
Крышка
4
4, 5, 6, 7
Вал ведомый
в сборе
Подшипник
1
9
Верхний картер
17
1
Подшипник
1
12
Шестерня
1
13
Картер
Шестерня
1
14
Подшипник
1
10
Вал
1
16
1
Измерить боковой
зазор в шлицах
1
Снять
при необходимости
Подшипник
1
11
Вал ведомый
1
15
Номер
позиции
Кол-во
Рис. 4.2. Схема разборки сборочной единицы «дерево»: а – эскиз объекта ремонта (редуктор); б – схема разборки редуктора: 1 – ведущий вал; 2 – шкиф;
3, 8 – фланцы; 4, 5, 6, 7 – крышки; 9, 10, 11, 12 – подшипники; 13, 14 – шестерни;
15 – ведомый вал; 16 – картер; 17 – верхний картер
ВОПРОСЫ ДЛЯ САМОКОНТРОЛЯ
1. Какими терминами и определениями описываются показатели технического обслуживания и ремонта подвижного состава, эксплуатируемого на железнодорожных путях общего и необщего пользования?
2. Дайте определения понятиям «объект ремонта» и «сборочная единица».
47
3. Что понимается под исправным состоянием и неисправным состоянием подвижного состава?
4. Объясните, в чем различите неработоспособного состояния подвижного состава от неработоспособного состояния подвижного состава
по внутренним ресурсам и неработоспособного состояния подвижного
состава по внешним ресурсам?
5. Объясните в чем различие следующих понятий: «проверка (осмотр)»,
«дефектация» и «ревизия».
6. Изобразите схему технологического процесса ремонта сборочной
единицы.
7. С какой целью маркируются детали локомотива или вагона?
8. Сколько позиций включает технологический процесс съемки и разборки сборочной единицы локомотива или вагона? Назовите их порядок.
9. Какие операции повторяются наиболее часто при демонтажных
работах?
10. Изобразите схему «дерево» разборки сборочной единицы локомотива или вагона.
Рекомендуемая литература: [32, 34, 35] (см. Библиографический список).
5. ПРИЧИНЫ ВОЗНИКНОВЕНИЯ НЕИСПРАВНОСТЕЙ
В ДЕТАЛЯХ МАШИН
5.1. Теория трения и изнашивания: основные понятия
В процессе эксплуатации подвижного состава появляются различные
неисправности, которые приходится устранять при техническом обслуживании или ремонте. Причинами этих неисправностей могут быть:
1) процессы естественного происхождения; 2) ошибки при выборе конструкторских или технологических решений; 3) нарушения правил технической эксплуатации локомотива (вагона).
Неисправности, обусловленные процессами естественного происхождения, проявляются чаще всего в виде значительного изнашивания
деталей и сборочных единиц, накапливающегося в результате длительной эксплуатации локомотива (вагона) (постепенный отказ), или в форме
внезапных отказов, вызванных исчерпанием конструкционным материалом своего ресурса (старение и явление усталости материала)36.
Изнашивание – это процесс разрушения или отделения материала с
поверхности твердого тела и (или) накопления его остаточных деформаций при трении, проявляющийся в постепенном изменении размеров
36
Мотовилов К.В., Лукашук В.С., Криворудченко В.Ф., Петров А.А. Указ. соч.
48
или формы тела. Изнашивание характеризуется величиной износа, интенсивностью и скоростью изнашивания.
Рассмотрим рис. 5.137, где износ – это результат изнашивания, определяемый в установленных единицах. Величина износа может выражаться
единицами длины, массы, объема и др. (соответственно линейный, массовый и объемный износ).
Интенсивность изнашивания – это отношение величины износа к
объему выполненной работы, например мм/км пробега (рис. 5.1, а).
Скорость изнашивания – это отношение величины износа к времени, в течение которого проходило изнашивание (рис. 5.1, б).
а
б
h
υ
hпр
a
b
c
t
a
b
c
t
Рис. 5.1. Графики интенсивности (а) и скорости (б)
изнашивания деталей в зависимости от времени
Интенсивность и скорость изнашивания, как правило, не остаются
постоянными во времени (рис. 5.1). Процесс изнашивания обычно происходит на протяжении трех стадий.
На первой стадии (участок а) происходит приработка детали, сопровождаемая интенсивным износом.
На второй стадии процесс изнашивания стабилизируется (участок b),
скорость изнашивания практически постоянная (рис. 5.1, б). Этот участок
характеризует нормальную работу узла. Постепенное изменение размеров трущихся деталей, приводящее к ухудшению условий смазывания,
появлению динамических нагрузок в соединении и другое.
На третьей стадии происходит катастрофическое увеличение скорости изнашивания (участок с).
Накопление статистических данных по характеру изнашиваемости
различных деталей локомотивов (вагонов) позволяет установить допустимые износы деталей hпр (рис. 5.1, а) и обоснованно планировать
межремонтные циклы (сроки или пробеги).
37
Там же.
49
Изнашивание является результатом трения соприкасающихся частей
машин друг с другом или с окружающей средой (для локомотивов (вагонов) – это элементы железнодорожного пути, перевозимый груз и др.).
Внешнее трение – это явление сопротивления относительному перемещению, возникающее между двумя телами в зонах соприкосновения поверхностей по касательной к ним, сопровождаемое диссипацией
энергии. По характеру относительного перемещения различают трение
покоя (при микроперемещениях до перехода к относительному движению, относительная скорость перемещения близка к нулю) и трение
движения – трение двух тел, находящихся в относительном движении.
Трение движения подразделяется на трение скольжения, при котором скорости относительного движения тел в точке контакта различны по
величине или направлению, и трение качения, происходящее при одинаковых по величине и направлению скоростях относительно движения.
«Чистое» трение качения возможно только теоретически. В процессе эксплуатации оно всегда сопровождается, пусть даже незначительным, проскальзыванием некоторых элементов деталей, образующих пару трения38.
По характеру смазывания контакта соприкасающихся поверхностей в
парах трения различают трение без смазочного материала (детали
фрикционных гасителей колебаний, поглощающих аппаратов, механизма автосцепки, тормозные колодки и обод колеса и др.), трение с граничной смазкой (толщина слоя смазочного материала от размеров одной молекулы до 0,1 мкм – смазывание деталей тормозных приборов
распыленным в воздухе маслом) и трение с жидкой или вязкопластической смазкой (детали подшипников и др.).
5.2. Механизм изнашивания деталей пар трения
и виды разрушения рабочих поверхностей
5.2.1. Виды трения
Основными видами отказов локомотивов (вагонов) являются преждевременные износы, вызываемые трением сопряженных поверхностей.
По условиям смазки трение подразделяется на сухое, граничное и
жидкостное.
При сухом трении смазка полностью отсутствует. Трение сопровождается повышенными температурами, вследствие чего может происходить пластическая деформация поверхностных слов металла, облегчающая их износ. При сухом трении работают сопряжения с неподвижными посадками, муфты сцепления, фрикционные гасители колебаний и
т. д. Коэффициент трения при сухом трении составляет 0,1–0,8.
38
Антимонов А.М. Основы технологии машиностроения: учебник. Екатеринбург:
Изд-во Урал. ун-та, 2017. 176 с.
50
Граничное трение возникает в присутствии весьма тонкого масляного слоя, толщина которого составляет 0,1 мм. При граничном трении
весьма важно удержание тончайшей масляной пленки на поверхности
трения, что достигается ее вязкостью и маслянистостью. Граничное трение является неустойчивым и легко может переходить в сухое трение.
Коэффициент трения составляет 0,01–0,05.
S
При жидкостном трении (гидродинамиP
ческом) поверхности деталей полностью
разделены слоем смазки (рис. 5.2), поэтому
n
d
износ оказывается ничтожным, так как коэффициент трения составляет 0,001–0,008.
По гидродинамической теории смазки
h
наименьшая толщина слоя h определяется
по формуле
d2 n
,
h
18,36 P C S
(5.1)
Рис. 5.2. Схема создания
жидкостного трения
где d – диаметр вала, м; n – число оборотов, об/мин; – вязкость масла,
кгс/м2; P – удельная нагрузка, кгс/м2; C – коэффициент, определяющий
соотношение между диаметром и длиной подшипника, C d l / l ; l –
длина подшипника, м; S – зазор между шейкой и подшипником, м.
Минимальная толщина масляного слоя должна соответствовать отношению S / 4 . Величины n , и P являются переменными. Нетрудно
заметить, что наиболее неблагополучные условия для жидкостного трения создаются при уменьшении соотношения n / Р , т. е. при снижении
частоты вращения и увеличении нагрузки.
Приведенная формула (5.1) имеет большое практическое значение.
Она позволяет рассчитывать, при прочих равных условиях, обороты вала, диаметр вала, вязкость масла и допустимую нагрузку на вал, при которых может быть осуществлено жидкостное трение.
Износ сопряжений, рассчитанных на жидкостное трение, происходит
главным образом в момент пуска машины, при перегрузках и при применении масла несоответствующего сорта.
Ещё не так давно основной причиной изнашивания считали то, что в
процессе относительного движения поверхностей неровности одной поверхности зацепляются за неровности другой поверхности, и это приводит
к срезанию или выламыванию неровностей. Исследования в области триботехники показывают, что механизм изнашивания значительно сложнее.
Изнашивание является результатом механических, физических и
химических процессов, протекающих в зоне контакта трущихся поверхностей, которые могут сопровождаться следующими явлениями39:
39
Там же.
51
1) взаимным внедрением и зацеплением неровностей сопряженных
поверхностей;
2) упругим и пластическим деформированием материала в зоне контакта;
3) молекулярным взаимодействием в виде адгезии и схватывания поверхностей;
4) изменением температурных режимов, приводящим к релаксационным процессам, в результате которых поверхностный слой не наклёпывается, а пребывает в состоянии повышенной пластичности.
В триботехнике рассматривается достаточно большой круг видов изнашивания рабочих поверхностей пар трения, сопровождаемых указанными выше явлениями.
Рассмотрим виды изнашивания, представляющие наибольший интерес для процессов проектирования, изготовления и эксплуатации локомотивов (вагонов)40.
Водородное изнашивание. Водородное изнашивание, как один из
процессов разрушения поверхностей при трении скольжения, выявлено
лишь около 30 лет назад российскими учеными Д.Н. Гаркуновым и
А.А. Поляковым. Водородное изнашивание проявляется в виде следующих процессов, протекающих в зоне трения:
а) интенсивное выделение водорода при трении из водородосодержащих материалов;
б) адсорбция водорода на поверхностях трения;
в) диффузия водорода в деформируемый в зоне контакта слой стали;
г) особый вид разрушения поверхности, связанный с одновременным
развитием большого числа зародышей трещин по всей зоне деформирования и проявляемый в виде мгновенного образования мелкодисперсного порошка материала.
На железнодорожном транспорте водородное изнашивание наблюдается в парах трения колес и композиционных тормозных колодок.
Абразивное изнашивание. Абразивным изнашиванием называют
разрушение поверхности детали в результате ее взаимодействия с
твердыми частицами при наличии относительной скорости. Такими частицами могут быть следующие:
а) неподвижно закрепленные твердые зерна в материалах пары трения;
б) частицы насыпных грузов или абразивные частицы верхнего строения пути, вовлекаемые воздушными потоками в зону контакта;
в) свободные абразивные частицы в виде продуктов изнашивания,
пребывающие в зазоре сопряженных деталей и др.
40
Антимонов А.М. Указ. соч.
52
Изнашивание вследствие пластичного деформирования. Этот
вид изнашивания (в форме смятия) заключается в изменении размеров
и формы детали в результате пластической деформации ее микрообъемов и вытеснения материала из зоны контакта. Чаще всего он проявляется в виде проката поверхности катания колеса.
Изнашивание при схватывании. Схватывание – это явление прочного соединения металлов в результате взаимного трения или совместного деформирования. При этом образуются прочные металлические
связи в зонах контакта поверхностей и исчезает граница между соприкасающимися телами. Изнашивание при схватывании может проявляться
в следующих видах:
а) вырывы материала в виде микроскопических частиц и перенос их
на другую поверхность при малой интенсивности изнашивания;
б) образование тонкой пленки мягкого материала на твердой поверхности (намазывание латуни сепараторов на ролики подшипников и др.);
в) вырывание материала с образованием глубоких борозд, уступов;
г) задиры – образование борозд с оттеснением материала как в стороны, так и по направлению скольжения;
д) заедание – форма проявления схватывания, характеризуемая образованием широких и глубоких борозд, крупных наростов, оплавления
поверхности, часто приводящих к заклиниванию деталей.
Другие виды изнашивания (такие, как кавитационное, эрозионное,
при фретинг-коррозии и др.) характерны для узкого класса машин и
здесь не рассматриваются.
5.2.2. Виды износа
По классификации профессора В.И. Костецкого, ведущими износами являются: износ схватыванием, окислительный, тепловой, абразивный, осповидный и коррозийный, усталостный.
Износ схватыванием возникает при отсутствии смазки и защитной
пленки окислов, при трении с малыми скоростями (до 1,0 м/с для стали)
и удельными давлениями, превышающими предел текучести металла.
Износ сопровождается высоким коэффициентом трения и образованием
металлических связей. Этот вид износа самый разрушительный из всех
видов. Он возникает во втулках и поршнях двигателей внутреннего сгорания (ДВС), шейках колесных пар, моторно-осевых подшипниках и на
поверхностях других деталей локомотива.
Окислительный износ вызывается микропластическими деформациями в тонких слоях металла с последующей диффузией кислорода.
Образующиеся окислы железа Fe O, Fe2 O3, Fe3 O4 обладают повышенной хрупкостью, это приводит при дальнейшей работе к выкрашиванию
53
металла. Этот вид износа проявляется на шейках коленчатых валов,
цилиндровых втулках и пальцах поршней ДВС.
Тепловой износ вызывается действием теплоты, возникающей в результате трения деталей при больших скоростях и удельных давлениях.
Получаемое тепло не успевает отводиться вглубь металла, нагревает
его и приводит в одних случаях к своеобразной термической обработке,
в других – к размягчению поверхности и смятию. Данный вид износа
проявляется на кулачках распределительных валов, тарелках толкателей, на рабочих поверхностях цилиндровых втулок ДВС.
Абразивный износ возникает в результате царапывающего и режущего действия твердых абразивных частиц, которые попадают в зону
трения с жидкостью и воздухом. Такому износу подвержены цилиндровые втулки, подшипники коленчатого вала, шейки колесных пар, плунжерные пары и другие соединения.
Осповидный износ возникает при трении качения в шарико- и роликоподшипниках и в зубьях шестерен. Причина износа – сосредоточение
большой нагрузки на очень малых площадях, приводящей к предельным
контактным напряжениям. Эти условия вызывают пластические деформации в тонких слоях металла с последующим насыщением их кислородом, т. е. образованием окислов металлов.
Коррозийный износ бывает двух видов: химический и электрохимический. Химическая коррозия происходит под влиянием сухих газов или
диэлектриков (смолы, керосина, топлива). В результате образуются соединения металла, обладающие низкой механической прочностью. Данному износу подвержены: выпускные клапаны газораспределительного
механизма ДВС, поршни, крышки цилиндровых втулок, выпускные коллекторы ДВС и другие соединения.
Электрохимическая коррозия возникает при соединении металла с
электролитами (растворы кислот, солей и щелочей). Образующиеся микрогальванические соединения, в которых роль анода выполняют зёрна чистого металла, приводят к разрушению поверхностей. Такому износу подвержены: блоки ДВС, подшипники скольжения, система охлаждения ДВС.
Усталостные износы и разрушения. Износы и разрушения деталей, происходящие под действием циклически изменяющихся во времени динамических нагрузок и проявляемые в форме зарождения и развития трещин, относятся к усталостным. Явление усталости материалов
проявляется лишь в случаях внешнего нагружения конструкции, приводящего к появлению в ее элементах знакопеременных или пульсирующих напряжений (в первом случае изменяется во времени знак, а иногда
амплитуда напряжений, во втором – только амплитуда).
Особенностью усталостного разрушения деталей является то, что
под воздействием указанных выше режимов нагружения в материале
детали появляются микроскопические трещины (0,1–0,5 мм), которые с
54
течением времени развиваются, достигая критической величины41. Период работы детали от возникновения первой микроскопической трещины до окончательного разрушения называют живучестью детали.
Трещинообразование присуще значительной части деталей и сборочных единиц локомотивов (вагонов), полученных различными технологическими методами (литые боковые рамы тележек, корпуса автосцепок, поглощающих аппаратов и букс, колеса, оси, сварные узлы рамы и
кузова и др.). Трещины усталости зарождаются и развиваются, как правило, на участках, имеющих концентрацию напряжений. В качестве концентраторов напряжений могут выступать неметаллические включения и
литейные дефекты, неровности грубо обработанной поверхности, необоснованные усиления сварных швов, подрезы основного металла в
зонах сварки, случайные ожоги электродом и др.
Усталостные разрушения ответственных деталей вагонов могут привести к аварийным ситуациям, поэтому задача повышения сопротивления усталости является весьма актуальной.
5.3. Факторы, влияющие на процессы изнашивания
При прочих равных условиях интенсивность изнашивания существенно зависит от качества контактируемых поверхностей. Качество поверхности определяется геометрией поверхности как границы тела и физикохимическими свойствами, обусловленными процессом ее образования
при обработке детали.
Качество поверхности деталей вагонов влияет на такие их служебные свойства, как: сопротивление усталости, износостойкость, коррозионная стойкость, прочность посадок с натягом, плотность подвижных и неподвижных соединений и др. Геометрия поверхности характеризуется ее шероховатостью и допусками формы (допуски плоскостности, цилиндричности и др.). Физико-химические свойства поверхности
определяются ее структурой, микротвердостью, глубиной наклепа, остаточными напряжениями.
Шероховатость поверхности (рис. 5.3)42 оценивают по ряду характеристик. В России для количественной оценки шероховатости поверхности
принято три высотных параметра Rа , Rz , Rmax , один комплексный параметр t p и два шаговых параметра: средний шаг местных выступов S и
средний шаг неровностей профиля Sт – всего шесть параметров (в Дании
и Франции – 10, Чехии – 3, Японии – 1).
41
42
Мотовилов К.В., Лукашук В.С., Криворудченко В.Ф., Петров А.А. Указ. соч.
Там же.
55
l
Линия выступов
Линия впадин
H5 min
h2 max
Rmax
b0
p
yn
m
h5 min
Si
H5 max
Smin
b1
H2 max
b1
h2 minH2 min
h1 min H1 min
y1
h1 max
H1 max
Si
Рис. 5.3. Профиль шероховатости поверхности и его характеристики
Указанные выше параметры определяют по следующим выражениям
Ra
5
1 n
1 5
y i ; Rz Hi max Hi min
n i 1
5 i 1
i 1
1 n
t
;
Bi ,
p
l i 1
(5.2)
где Ra – среднее арифметическое отклонение профиля; n – число выбранных точек на базовой длине l ; y i – отклонение профиля в выбранных точках от средней линии m ; Rz – высота неровностей по десяти
точкам; Hi max , Hi min – отклонения от средней линии пяти вершин
наиболее высоких выступов и пяти наиболее глубоких впадин; t p – относительная опорная длина профиля уровня р ; р – уровень сечения профиля (в процентах от наибольшей высоты неровностей Rmax ), определяемый расстоянием между линией выступов и линией, пересекающей
профиль эквидистантно линии выступов; Bi – длина отрезка, отсекаемого на микровысоте.
Полученная при обработке деталей начальная шероховатость поверхности оказывает существенное влияние на интенсивность изнашивания лишь на стадии приработки поверхностей. В результате приработки исходные параметры шероховатости изменяются, приобретая
значения, характерные для стадии нормальной эксплуатации.
Кроме рассмотренного, существенное влияние на процессы изнашивания оказывают: обоснованный выбор конструкционных материалов, а также
способы термической и химико-термической обработки рабочих поверхностей деталей в парах трения; жёсткость и податливость узлов; разгрузка
рабочих поверхностей; способы и приемы сборки, исключающие нежелательные остаточные напряжения; применение обоснованных смазочных
материалов и поддержание их свойств в процессе эксплуатации вагона43.
43
Там же.
56
5.4. Причины возникновения неисправностей в деталях машин
Возникновение неисправностей в деталях машин обусловлено конструктивными, технологическими и эксплуатационными факторами.
К конструктивным факторам относятся:
а) несоответствие расчётных и фактических нагрузок;
б) повышенные скорости относительного перемещения деталей в соединениях;
в) несоответствие свойств материалов и их структуры условиям эксплуатации;
г) неудачное конструктивное исполнение деталей и сборочных единиц;
д) неправильное назначение величин зазоров или натягов в сопряжениях;
е) наличие микрогеометрии, шероховатости с параметрами, которые
не обеспечивают нормальную работу деталей;
ж) необеспечение условий смазывания и охлаждения;
з) и др.
К технологическим факторам относятся: выбор способов получения заготовок, а также видов применяемых технологий при изготовлении
деталей, не обеспечивающих выполнение технических условий, назначенных конструктором, или приводящих впоследствии к возникновению
дефектов; нарушение правильности сборки.
К эксплуатационным факторам относятся: повышенная интенсивность и нарушение условий эксплуатации, несвоевременность и плохое
качество периодических ремонтов и технического обслуживания.
Кроме этого, в сборочных единицах, составляющих основу конструкции изделия и рассчитанных на длительный срок службы, имеются детали, замена или восстановление которых заложена конструктором при
проведение плановых видов ремонта44.
Многолетним опытом восстановления деталей установлена взаимосвязь между конструктивными элементами деталей (типовые поверхности), видами износов (повреждения) и технологическими способами восстановления деталей (устранение повреждений). Иллюстрация этой
взаимосвязи приведена в табл. 5.145.
Обработка на произвольный размер характеризуется тем, что деталь проходит механическую обработку на глубину, равную или несколько больше глубины дефекта.
44
Гапанович В.А., Андреев В.Е., Митрохин Ю.В., Яговкин А.Н., Иванов К.В. Эксплуатация и техническое обслуживание подвижного состава: учеб. пособие для вузов
ж.-д. транспорта / под общ. ред. В.А. Гапановича. М.: «ИРИС ГРУПП», 2012. 572 с.
45
Там же.
57
Например, обработка поверхностей катания колёс колёсной пары. При
этом накладываются дополнительные требования – допустимая разница в
диаметрах колёс и минимально допустимая толщина ободьев колёс.
Виды повреждений типовых поверхностей
и способы их устранения
Типовые поверхности
1. Цилиндрические
наружные поверхности
(материал – сталь)
2. Цилиндрические
внутренние поверхности
(материал – сталь)
3. Наружные резьбовые
поверхности (материал –
сталь)
4. Деформация детали
(материал – сталь)
5. Плоские рабочие поверхности (материал – сталь)
Виды
повреждений
Таблица 5.1
Технологические способы
устранения повреждений
Обработка на произвольИзнос
ный размер.
по диаметру,
Обработка на градационриски, задиры
ный размер.
и др.
Различные виды наплавки
Износ по диаПостановка насадок.
метру, риски
Различные виды наплавки
задиры
Износ резьбы, Обработка на меньший
срывы, забои- размер (диаметр).
ны
Различные виды наплавки
Правка в нагретом
Изгиб
и холодном состояниях
Износы
Различные виды наплавки
Обработка на градационный (ремонтный) размер, заключается в
обработке повреждённой поверхности на глубину дефекта с обеспечением определённого, заранее обусловленного, размера.
Например, этот способ применялся при ремонте шеек осей РУ на
втулочной посадке подшипников, когда полномерная шейка диаметром 135,0 мм, при наличии повреждений, перетачивалось на ближайшую градацию 134,5; 134,0; 133,5; 133,0 мм. Уменьшение диаметра шейки компенсировалось увеличением толщины закрепительной втулки.
Восстановление насадками обеспечивает доведение изношенной
поверхности до размера новой детали. Насадки – это втулки различного
размера, выполненные из материала с высокой износостойкостью.
Например, широко используются втулки, устанавливаемые в детали
рычажной передачи при постройке подвижного состава, которые при износе заменяются на новые.
Наибольшее применение для устранения неисправностей, таких, как
трещины, изломы, износы, у деталей и сборочных единиц различных
конструкций, получили различные способы автоматической, полуавтоматической и ручной наплавки и сварки46.
46
Там же.
58
ВОПРОСЫ ДЛЯ САМОКОНТРОЛЯ
1. Назовите разновидности ремонтных размеров, используемых при
ремонте локомотивов.
2. Назовите разновидности трения по условиям смазки.
3. Какими условиями обеспечивается жидкостное трение?
4. Почему происходит износ схватыванием?
5. На каких деталях возникает осповидный износ?
6. Какова причина возникновения электрохимической коррозии?
7. Какие детали подвергаются химической коррозии?
8. В чем причина увеличения износа в начальный период работы
машины?
9. Укажите виды повреждений типовых поверхностей и способы их
устранения.
Рекомендуемая литература: [32, 34] (см. Библиографический
список).
6. ТЕХНОЛОГИЧЕСКИЕ МЕТОДЫ ПОВЫШЕНИЯ
ИЗНОСОСТОЙКОСТИ ДЕТАЛЕЙ
6.1. Методы модифицирования поверхностей
деталей лазерным излучением
Повышения износостойкости деталей можно добиться, применив сравнительно недорогие, но эффективные методы химико-термической обработки рабочих поверхностей деталей (цементация, азотирование, фосфатирование), а также прогрессивные методы поверхностного упрочнения
деталей, такие, как алмазное выглаживание и др.
В целях повышения долговечности деталей подвижного состава перспективным является использование при обработке поверхностей высококонцентрированных источников тепловой энергии – лазерное излучение.
Методы модифицирования поверхностей деталей лазерным излучением подразделяют на две основные группы47.
К первой группе следует отнести обработку, которая не вызывает
оплавления или какого-либо другого изменения исходной шероховатости поверхности и связана только с нагревом поверхностного слоя и последующим его самоохлаждением. Управляя процессами нагрева и
охлаждения, можно получить различные эффекты в поверхностном
слое: термическое упрочнение, отпуск, отжиг. Эффект упрочнения угле47
Мотовилов К.В., Лукашук В.С., Криворудченко В.Ф., Петров А.А. Указ. соч.
59
родосодержащих сталей заключается в образовании в поверхностном
слое специфической дезориентированной в пространстве структуры, которая имеет микротвердость, превышающую в 1,5–5 раза микротвердость основы. Глубина модифицированного слоя в зависимости от режимов облучения может достигать 0,05–3 мм.
Ко второй группе относят обработку, при которой происходит
оплавление поверхности: термическое упрочнение, лазерная аморфизация, поверхностное микролегирование и наплавка.
Лазерное термическое упрочнение с оплавлением поверхности
позволяет получить в наружном слое характерное для закалки из жидкого состояния дендритное строение.
Аморфизация поверхности – процесс, при котором в поверхностном слое обрабатываемого материала создается максимально возможный градиент температур. При этом в узком поверхностном слое толщиной около 0,02–0,05 мм скорости охлаждения могут достигать значений
106–107 С/с, которые являются достаточными для «замораживания»
разупорядоченной при расплавлении структуры, т. е. для перевода металла в аморфное состояние.
Лазерное микролегированние – процесс расплавления с помощью
лазерного излучения поверхностного слоя и введения в образовавшийся
расплав легирующих элементов. Поверхностное микролегирование используют в целях повышения износостойкости, жаропрочности, теплостойкости, коррозионной стойкости.
Лазерная наплавка – эффективный метод улучшения эксплуатационных характеристик и восстановления изношенных рабочих поверхностей деталей машин и инструментов. На подготовленную обрабатываемую поверхность предварительно или одновременно с лазерным излучением подается в виде проволоки или порошка наплавляемый материал. Под действием лазерного излучения происходит расплавление этого
материала и частичное оплавление материала основы, что обеспечивает хорошую адгезию покрытия и основы48.
6.2. Технологические методы повышения
сопротивления усталости
Одним из наиболее распространенных методов повышения сопротивления усталости является получение на поверхности детали упрочнённого слоя (наклёпа), создаваемого путем местного пластического
деформирования материала. Для деталей цилиндрической формы (оси)
обычно применяют накатку ответственных поверхностей стальными роликами. Детали сложной формы (пружины, листы рессор и др.) обраба48
Там же.
60
тывают стальной дробью в дробеметных камерах. Параметры режимов
обработки (геометрия ролика, сила прижатия его к детали, скорость
вращения детали, скорость перемещения ролика, размеры дроби, ее
скорость к моменту удара) обычно определяют опытным путем.
Положительная роль поверхностного пластического деформирования выявлена применительно к латунным сепараторам буксовых роликовых подшипников (латунь ЛC59-1), которые часто выходят из строя изза трещин в углах окон. Холодная деформация углов окон специальной
протяжкой с деформирующими зубьями позволила до трех раз повысить
количество циклов нагружения до появления трещин усталости.
В целях повышения сопротивления усталости сварных конструкций
рекомендуется применение следующих технологических методов: 1) термическая обработка сварного технологического узла; 2) механическая и
аргонодуговая обработка сварных швов и околошовной зоны; 3) наклеп
многобойковыми упрочнителями.
1. Термическая обработка (отжиг, нормализация) как способ повышения сопротивления усталости дает положительный результат при применении ее в технологических процессах изготовления достаточно сложных
сварных толстостенных конструкций (сварные рамы тележек, надрессорные
балки и др.). Отжиг сварной конструкции позволяет практически полностью
снять остаточные напряжения, обусловленные усадкой сварных швов. Однако термическая обработка не позволяет устранить деформации сварной
конструкции, вызванные остаточными напряжениями.
2. Механическая обработка сварных швов и околошовной зоны
режущим инструментом (абразивные круги, фрезы) выполняется на минимальную глубину (до 3 % толщины обрабатываемого элемента), необходимую для обязательного снятия поверхностного слоя металла на
всей длине линии сплавления в зоне обработки в целях получения чистой, блестящей поверхности и плавных переходов от металла шва к
основному металлу. Обработанная поверхность не должна иметь рисок,
расположенных поперек направления усилий, действующих в элементе
при его работе, а также надрезов и следов подрезов по границам шва,
выходящих на поверхность пор, раковин, шлаковых включений. Механическая обработка наиболее предпочтительна для стыковых соединений.
В этом случае обработке подвергают переходную зону шириной не менее 25 мм с образованием плавного перехода от металла усиления
сварного шва к основному металлу. Радиусы перехода и вершины усиления должны быть не менее 15 мм.
3. Аргонодуговая обработка применяется в основном на границе
сварного шва и основного металла в целях создания плавного перехода
в этой зоне (рис. 6.1)49.
49
Там же.
61
а
б
Рис. 6.1. Формы оплавленных линз при аргонодуговой обработке
швов сварных соединений: а – стыковых; б – нахлесточных
Аргонодуговой обработке рекомендуется подвергать конструкции из
спокойных и полуспокойных углеродистых и низколегированных сталей.
Обработка осуществляется на постоянном токе прямой полярности любыми серийными горелками (ГРА-1, АР-36, ГРА-3 и др.), предназначенными для сварки вольфрамовыми электродами в защитных газах. В качестве электрода используется пантанированный вольфрам марки ЭВЛ-10,
защитным газом служит аргон не ниже второго сорта. Другие сведения о
применяемом оборудовании приведены на рис. 6.250.
3
2
1
+
4
7
8
5
6
Рис. 6.2. Схема подключения оборудования при аргонодуговой обработке сварных швов: 1 – источник питания ПСО-500;
2 – балластный реостат РБ-300; 3 – измерительные приборы;
4 – горелка; 5 – обрабатываемый узел; 6 – индикаторная
шкала уровня; 7 – регулирующий кран; 8 – баллон с аргоном
При обработке конструкций с толщиной элемента 12 мм и более оплавление следует выполнять с введением в зону дуги проволоки Св-08Г2С
диаметром 1,6–2 мм.
50
Там же.
62
Качество аргонодуговой обработки контролируется визуально путем
сопоставления поверхности с контрольным эталоном. Обработанная поверхность не должна иметь пор, подрезов, грубой чешуйчатости, кратеров, раковин. Оплавленная линза должна располагаться строго на границе шва и основного металла.
Наклёп многобойковым упрочнителем. В сварных конструкциях
поверхностному наклепу целесообразно подвергать места с концентраторами напряжений преимущественно границы сварного шва и основного металла. Ширину наклёпанной зоны с одной стороны шва принимают
в пределах 15–20 мм. Наклёпу можно подвергать и бывшие в эксплуатации конструкции, если в них нет усталостных трещин.
В качестве инструмента для наклёпа используют пневматические
молотки типа 62КМ-6, КМП-13, КМП-31 с энергией удара 4–9 Нм со специальными насадками для крепления упрочнителя. Упрочнителями являются пучки термообработанной (закалка и отпуск по специальным режимам) до твердости HRC 50 проволоки диаметром 2–3 мм из стали марок 65Г, 60С2, П-70. Наклеп выполняют при давлении сжатого воздуха
0,4–0,5 МПа. Скорость перемещения инструмента по обрабатываемой
поверхности 1,5–2,5 мм/с.
Если на обрабатываемой поверхности имеются недоступные для инструмента места в виде больших усилений, свисаний, подрезов (рис. 6.3)51,
то их необходимо предварительно подварить или оплавить аргонодуговой
обработкой.
а
в
б
г
Рис. 6.3. Схема устранения недоступных мест при обработке сварных швов
многобойковым упрочнителем: а – свисание; б – устранение подваркой;
в – большое усиление и подрез; г – устранение аргонодуговой обработкой;
1 – многобойковая насадка
51
Там же.
63
Важно помнить, что подвергать наклёпу в целях повышения сопротивления усталости можно только конструкции, эксплуатируемые в условиях,
при которых не происходит релаксация остаточных напряжений (температура не выше 200 °С; действующие напряжения должны быть ниже предела
текучести). При ремонте наклеп необходимо выполнять только после производства сварочных работ в близко распложенных зонах и правки.
6.3. Способы снижения износа деталей
В целях снижения износа трущихся поверхностей требуется: не допускать длительную работу ДВС на минимальных оборотах коленчатого вала;
своевременно и качественно очищать масло, топливо и воздух от продуктов износа и абразивных частиц; вводить в масло антиокислители; проводить после ремонта качественную обкатку узла; повышать твердость трущихся поверхностей; вводить в масло модификаторы трения.
В шестидесятых годах прошлого столетия советскими учеными профессорами Д.Н. Гаркуновым и И.В. Крагельским было открыто явление
безызносности, позволяющее организовать работу трущихся пар без износа сопрягаемых поверхностей благодаря сервовитной пленке толщиной
1–2 мкм, которая создается путем переноса в зону контакта меди или другого металла. Медь при этом обладает удивительными свойствами: она
полужидкостная при комнатной температуре и имеет электрический заряд,
что удерживает ее в зоне трения. В промышленности это явление используется в виде металлоплакирующих смазок в машинах и механизмах, что
еще в восьмидесятых годах прошлого столетия позволило получить экономический эффект около восьми миллиардов рублей.
К металлоплакирующим смазкам относятся модификаторы трения,
т. е. смазки, полученные измельчением в порошок горной породы, содержащей кварциты. Такого рода смазки по своей эффективности не хуже,
чем металлоплакирующие, они не разжижают смазку, а наоборот, сгущают
её. Процесс работы машины становится значительно чище, поскольку
смазка не вытекает из трущихся узлов. Стоимость смазок на основе модификаторов трения значительно меньше, чем металлоплакирующих, поэтому они широко используются в ДВС.
Научными работниками кафедры «Локомотивы и локомотивное хозяйство» Российского университета транспорта (МИИТа) были проведены
исследования по использованию триботехнического состава «Форсан» в
ДВС маневровых тепловозов, приписанных к депо Лихоборы Московской
ж.д. Оценку влияния препарата на экономичность и надежность ДВС проводили на основе измерения основных параметров его работы до и после
обработки. После триботехнической обработки дизеля повысилась средняя удельная эксплуатационная экономичность на 17,5 %. Одновременно
64
с этим снизилось трение в узлах дизеля. Так, зазоры в подшипниках коленчатого вала при почти полной эксплуатационной загрузке не увеличились, что позволяет говорить о полном прекращении износа шеек коленчатого вала после обработки маслом дизеля. Ресурс узлов увеличился на
60 %, что снизило стоимость ремонта дизеля в два раза.
На Белорусской ж.д. в целях повышения износостойкости широко используется эпиламирование деталей. Эпилам – раствор фторосодержащего поверхностно-активного вещества марки 6МФК-180 в хладоне-113. Он
имеет плотность 1580 кг/м3 и температуру кипения 47 С. Эпиламирование
осуществляют окунанием в бак с раствором и выдержкой 10–15 мин. После
этого деталь сушат и оценивают качество обработки. Как показали исследования, наилучшие результаты дает эпиламирование одной трущейся поверхности, обладающей наибольшей твердостью (например, шейки коленчатого вала, втулки цилиндра и т. п.). После эпиламирования износостойкость повышается в 3–3,5 раза. Если эпиламирование интенсифицировать
ультразвуком, то износ деталей можно снизить в 7 раз, а коэффициент
трения в 1,7 раза52.
ВОПРОСЫ ДЛЯ САМОКОНТРОЛЯ
1. На какие группы делиться метод модифицирования поверхностей
деталей лазерным излучением?
2. Дайте определения таким видам обработки поверхностей деталей,
как «лазерное термическое упрочнение» и «лазерное микролегирование».
3. В чем заключается технология обработки детали путем аморфизации поверхности?
4. В чем заключается технология обработки детали путем лазерной
наплавки?
5. В чем особенность технологических методов повышения сопротивления усталости сварных конструкций?
6. В чем особенность способов термической и механической обработки поверхностей деталей, повышающих сопротивление усталости?
7. Назовите особенность способа аргонодуговой обработки поверхностей деталей повышающего сопротивление усталости.
8. Охарактеризуйте способ наклёпа многобойковым упрочнителем поверхностей деталей.
9. Почему модификаторы трения снижают износ?
Рекомендуемая литература: [34, 35] (см. Библиографический
список).
52
Там же.
65
7. МЕХАНИЧЕСКИЕ СПОСОБЫ ВОССТАНОВЛЕНИЯ
РАБОТОСПОСОБНОСТИ ДЕТАЛЕЙ
7.1. Восстановление детали пластической
деформацией (давлением)
При восстановлении деталей пластической деформацией (давлением)
используются пластические свойства металла. Существуют три метода
обработки деталей давлением: осадка, раздача и обжатие (рис. 7.1)53.
а
б
Р
в
Р
δ
δ
δ
Р
δ
Рис. 7.1. Схемы восстановления деталей давлением:
а – осадка; б – раздача; в – обжатие
Поскольку при раздаче и обжатии направление силы и деформации
совпадает, а при осадке не совпадает. То при обработке давлением
необходимо выдержать температурный режим. Обработка давлением,
протекающая при температуре меньше температуры рекристаллизации и
вызывающая упрочнение (наклёп), называется холодной обработкой.
Рекристаллизация – изменение структуры металла в результате
его нагрева. Обработка, протекающая при температуре более температуры рекристаллизации, при которой металл имеет структуру без следов
упрочнения, называется горячей обработкой. Минимальная температура рекристаллизации определяется по формуле
t 0, 4 tпр ,
(7.1)
где tпр – температура плавления металла, С.
При горячей обработке механические свойства металла детали зависят от температуры начала и конца обработки, т. е. от температурного
интервала. Начальная температура не должна вызывать пережога или
перегрева, конечная – не должна вызывать наклёпа.
Например, для углеродистой стали с содержанием углерода до 0,3 % t н
составит:
tн 1200 1150 С; tс 800 850 С.
53
Антимонов А.М. Основы технологии машиностроения: учебник. Екатеринбург:
Изд-во Урал. ун-та, 2017. 176 с.
66
Для пламенных печей время нагрева определяется по формуле
Т К Д
Д,
(7.2)
где К – коэффициент, для углеродистых сталей, К 12,5 , для легированных К 25 ; Д – диаметр детали, мм.
В целях уменьшения количества углерода и образования окалины,
особенно на цементированных поверхностях, нагрев желательно вести в
среде, обогащенной углеродом, например в ящиках с карбюризатором.
После обработки, чтобы снять внутренние напряжения и улучшить пластические свойства детали, необходимо выполнить термообработку: отжиг или нормализацию.
Примеры восстановления деталей давлением: пальца шатуна – раздачей, втулки верхней головки шатуна – обжатием.
Преимущества данного способа: восстановление не требует дополнительного металла, он прост и позволяет экономить цветные металлы
и высококачественные стали. Применение способа ограничивается наличием в детали необходимого запаса металла54.
7.2. Восстановление деталей обработкой под ремонтный размер
Сущность способа – обработка поврежденных поверхностей деталей
системы «вал-отверстие» в целях устранения овальности и конусности,
не изменяя при этом положения геометрической оси детали.
Ремонтные размеры подразделяются на
dн
два вида: 1) категорийные (градационные) и
dр1
2) пригоночные.
X
Категорийным называется размер, устаδ
новленный для определенной категории ремонта.
Пригоночным называется размер с учетом припуска на пригонку детали «по месту». Для вала ремонтный размер всегда
меньше номинального, а для отверстия –
больше номинального.
Схема установления категорийных размеров приведена на рис. 7.255.
Первый категорийный размер определяется по формуле
d p1 dн 2 δmax X min ,
54
55
(7.3)
Антимонов А.М. Указ. соч.
Там же.
67
Рис. 7.2. Схема установления категорийного размера
для вала
где d н – номинальный размер, мм; δmax – максимальный односторонний
износ, мм; X min – минимальный припуск на обработку, мм.
Ремонтный интервал определяется по формуле
Yp 2 δmax X min .
(7.4)
Количество ремонтных градаций (категорий) определяется по формуле
n dн dmin / Yp ,
(7.5)
где dmin – минимально допустимый размер вала по условиям прочности,
мм.
Обработкой под категорийный размер устраняется износ шеек коленчатых валов. Для коленчатого вала дизеля 10Д100 установлено 7 категорий, с градационным интервалом 0,5 мм; для коленчатого вала дизеля Д49 1-го и 2-го исполнения установлено 4 категории, с градационным интервалом 0,1 мм.
Схема установления пригоночных размеров. Для примера используем расчет пригоночных размеров для моторно-осевого подшипника колесо-моторного блока, представленного на рис. 7.356.
d
dв
dш
Натяг
Зазор на масло (ЗМ)
Рис. 7.3. Схема установления пригоночного размера
в моторно-осевом подшипнике
Моторно-осевые подшипники поступают в депо в виде отливки и поэтому перед монтажом их необходимо обработать по внутреннему и
наружному диаметру. Внутренний диаметр определяется по формуле
56
Данковцев В.Т., Киселев В.И., Четвергов В.А. Техническое обслуживание и ремонт локомотивов: учеб. для студентов вузов ж.-д. трансп. М.: Учеб.-метод. центр по
образованию на ж.-д. трансп., 2007. 557 с.
68
dв dш ЗМ ,
(7.6)
где dш – диаметр шейки оси колесной пары, мм; ЗМ – минимальный зазор «на масло», мм.
Наружный диаметр определяется по формуле
dн dп Н ,
(7.7)
где d п – диаметр постели остова ТЭД, мм; Н – максимальный натяг
подшипника в остове ТЭД, мм.
Преимущества способа – это простота и дешевизна, более того, не
требуется дополнительного металла. Недостаток – необходимость ремонта или замены сопряженных деталей, что увеличивает время на ремонт и ухудшает взаимозаменяемость деталей57.
7.3. Восстановление путем постановки добавочной детали
Сущность способа – вместо изношенной поверхности (вала или отверстия) ставится дополнительная (добавочная) деталь, компенсирующая износ. Этот способ применяется для восстановления деталей как под ремонтный, так и под номинальный размер58.
Порядок восстановления:
1) производят обточку изношенного слоя, с учетом толщины добавочной детали (чистота поверхности 8–9 класса);
2) изготавливают добавочную деталь в виде втулки, материал ее
должен соответствовать материалу восстанавливаемой детали. Допускается в отверстие чугунных деталей и деталей, изготовленных из легких сплавов, ставить добавочные детали из Стали Ст20. Посадочная поверхность добавочной детали должна иметь натяг относительно восстанавливаемой поверхности 0,05–0,07 мм;
3) монтаж добавочной детали на восстанавливаемую можно производить двумя способами: 1) с использованием давления или 2) тепла.
В первом случае необходимое усилие запрессовки рассчитывается
по формуле
Р f d l,
(7.8)
где f – коэффициент трения; – удельное давление на контактную поверхность, кгс/мм2; d – диаметр сопряженной поверхности, мм; l – длина контактной поверхности, мм.
57
58
Там же.
Там же.
69
В целях предупреждения образования задиров на сопряженных поверхностях деталей их покрывают машинным маслом или графитом.
В тех случаях, когда детали работают с большими нагрузками или изготовлены из материалов, имеющих различные коэффициенты линейного расширения, или сопряжения работают в условиях высоких температур, или посадка должна быть с большим натягом, то монтаж добавочной детали производят нагревом охватывающей или охлаждением
охватываемой. Температура нагрева или охлаждения, С, определяется
по выражению
S
(7.9)
t
tп ,
d
где – максимальная величина натяга, мм; S – минимальный сборочный
зазор, мм; для цилиндрических деталей S 0,001 d , для конусных деталей S 0,05 d ; – коэффициент линейного расширения; d – номинальный диаметр сопряжения, мм; t п – температура в помещении, С;
«+» берется при нагревании, «–» – при охлаждении).
Прочность посадки с нагревом в 3 раза больше, чем прочность посадки в холодном состоянии. Нагрев деталей производят в масляных
ваннах при температуре 60–80 С или индукционным нагревателем при
температуре 100–120 С, время нагрева 1–2 мин. Охлаждения производят в твердой углекислоте, в жидком воздухе, кислороде или азоте.
Наиболее благоприятным телом для охлаждения являются сухой лед,
имеющий температуру (– 78 С) и азот (–196 С).
При восстановлении износа отверстий добавочную деталь крепят
винтами или штифтами, количество которых зависит от диаметра: при
Ø 30 мм ставится один, при Ø 30–50 мм ставится два через 180, при
Ø более 50 мм ставится три через 120.
Данным способом восстанавливают валы якорей вспомогательных
электрических машин, гнездо роликового подшипника в корпусе вертикальной передачи дизеля 10Д100, резьбовые отверстия.
Преимущества способа – надежность и доступность. Способ позволяет восстановить деталь под номинальный размер.
Недостатки – требуются дополнительные затраты на обработку поверхности изношенной детали и изготовление добавочной детали59.
7.4. Восстановление резьбы резьбовыми вставками и втулками
В процессе изготовления и эксплуатации разъёмных соединений внутренняя резьба в отверстии может быть частично повреждена или полностью сорвана. Причина – превышение рекомендуемого усилия закручива59
Там же.
70
ния болтов, винтов или шпилек, влияние коррозии, наличие стружки или
загрязнений внутри отверстий, а также износ резьбового канала.
Весьма часто при выполнении ремонтных работ деталей и механизмов в резьбовых соединениях материалов с различными механическими
свойствами выявляются такие дефекты, как разрушение или срез
резьбы. Существует много способов восстановления поврежденной
резьбы в деталях. Самым простым и доступным является рассверливание отверстия с поврежденной резьбой с последующим нарезанием
резьбы под больший диаметр. Следует отметить, что рассверливание
отверстий и нарезание новой резьбы в отдельных случаях недопустимо,
например, если это приводит к дисбалансу изделия60.
В случае восстановления наружной резьбы старая резьба удаляется
не менее чем на глубину более одной второй высоты резьбы, наплавляется, как правило, вибродуговой наплавкой и нарезается новая резьба
номинального размера. Однако этот способ не всегда возможен по конструктивным соображениям, например из-за малого диаметра или толщины стенок изделия.
Кроме этого, используется метод «заклеивания» резьбы специальными эпоксидными композициями. Однако это неприемлемо для деталей, воспринимающих высокие нагрузки и вибрации.
В таких случаях одним из лучших способов восстановления резьбы
является установка в посадочном месте для закручивания крепёжных
деталей, специально предназначенных для такой цели резьбовых проволочных вставок, которые имеют простую конструкцию, обеспечивающую превосходную надежность и долговечность разъемного соединения. Резьбовые проволочные вставки используют для увеличения
наружного диаметра и восстановления поврежденной, сорванной или
изношенной внутренней резьбы отверстий. Резьбовая проволочная
вставка представляет собой проволочную спираль с ромбическим сечением профиля, изготовленную с очень высокой точностью (рис. 7.4)61.
Проволочные резьбовые вставки представляют собой спираль с ромбическим профилем высокой точности, таким же, как у резьбы. Изготавливаются резьбовые вставки из самых разных материалов. Наиболее распространены вставки из высококачественной нержавеющей стали, что
позволяет полностью забыть о коррозии. Деталь может быть легко и быстро установлена, а само изделие – сразу подвержено дальнейшей эксплуатации. Применение резьбовых проволочных вставок имеет значительное
преимущество по сравнению с другими методами нарезания и восстанов60
Антимонов А.М. Основы технологии машиностроения: учебник. Екатеринбург:
Изд-во Урал. ун-та, 2017. 176 с.
61
TIME-SERT – совершенная технология восстановления резьбы: энциклопедия [Электронный ресурс]. Вюрт. Владивосток: Wurth. Режим доступа:
http://www.wunerthmarket.ru/paedia/time-sert/
71
ления резьбы, а именно: большой ассортимент диаметров и длин для выбора деталей как с метрической, так и с дюймовой резьбой; возможность
быстрого ремонта поврежденного соединения без разборки изделия; высокая точность изготовления размеров и формы.
а
б
Рис. 7.4. Резьбовая вставка: а – вид ромбического
сечения профиля; б – внешний вид резьбовой вставки
Кроме того, превосходная износостойкость при эксплуатации, прочность посадки и отсутствие необходимости в принятии дополнительных
действий для фиксации, а также наличие двухстороннего профиля, что
позволяет использовать резьбовые вставки для создания наружной и
внутренней резьбы. Значительное усиление прочности внутренней поверхности резьбового канала в изделиях из нетвердых (алюминий и его
сплавы, пластмасса) и тонких материалов. Отличное соотношение затраченного на ремонт времени и материальных затрат.
Каждая резьбовая вставка имеет строго определенное число витков
спирали. Детали стандартных размеров имеют длину, размер которой
пропорционален диаметру самой вставки.
Например, резьбовые проволочные вставки 1D, 2D, 3D изготовлены с
размерами длины, равными одному, двум и трем диаметрам детали.
Резьбовые вставки имеют определенное количество витков. Стандартно
выпускаются вставки 1D, 1,5D, 2D, 2,5D, 3D. Это означает, что длина
вставки равна одному диаметру, двум диаметрам и т. д. Выпускаются и
другие, специальные вставки, но с другими размерами.
Комплексное предложение из вставок, технологии установки, инструмента обычно именуется «система» c добавлением отличительного
фирменного названия.
Например система «V-coil», система «Recoil», система «BaerCoil»,
система «HeliCoil» и т. д.
72
Рассматриваемый метод восстановление резьбы в отверстие (рис. 7.5)62
общепризнан наиболее дешёвым из всех существующих. Он чрезвычайно прост и состоит из трех операций (рис. 7.5, а):
1) сверление (рис. 7.5, а). Отверстие с повреждённой резьбой рассверливается для удаления поврежденной резьбы.
Рекомендуемый диаметр сверла зависит от вида резьбы и её параметров и обычно приводится каждым производителем в специальных
таблицах – рекомендациях. Производители вставок предлагают к поставке всю гамму рекомендованных свёрл, однако ничто можно использовать стандартные свёрла необходимого размера;
2) нарезка резьбы (рис. 7.5, б). Нарезать резьбу метчиком соответствующего диаметра. Метчики предлагаемых систем имеют определённые отличия от стандартных, поэтому следует использовать метчики,
идущие в комплекте (рекомендуемые производителем);
3) установка проволочной пружинной вставки (рис. 7.5, в). С помощью
специального приспособления, входящего в комплект каждой системы,
произвести установку резьбовой вставки в подготовленное отверстие.
а
б
в
г
Рис. 7.5. Восстановление резьбы за счет пружинных вставок:
а – рассверливание поврежденной резьбы; б – нарезание резьбы под пружинную вставку метчиком; в – установка проволочной
пружинной вставки; г – удаление установочного язычка
62
Усиление и восстановление внутренней резьбы с помощью пружинных проволочных
вставок [Электронный ресурс]. Минск: Shilf. Режим доступа: http://shlif.by/?page=contacts
73
Новая резьба не только не уступает по своим прочностным характеристикам, оригинальной резьбе, но значительно превосходит её. При
необходимости резьбовые вставки можно извлекать с помощью специальных приспособлений, входящих в «систему».
Для обламывания и удаления язычка применяется специальный инструмент (см. рис. 7.5, г), а на вставках большого диаметра используются обычные плоскогубцы.
Наружный диаметр каждой резьбовой вставки в свободном состоянии
больше принимающей резьбы на точно рассчитанную величину. Эта разница обеспечивает необходимый натяг в месте посадки резьбовой вставки
и не даёт ей самостоятельно выкручиваться. Резьбовые вставки устойчиво
и практически без зазора располагаются в принимающей резьбе. При такой очень прочной посадке полностью отпадает необходимость использовать клей для фиксации, как в случае с классической втулкой.
Упругие свойства резьбовых вставок позволяют равномерно распределять нагрузки и напряжения. Угловая и шаговая погрешность компенсируются по всей длине резьбовой вставки, что позволяет не только достигать
идеальных условий для передачи
усилия между болтом и приёмной
а
б
50
резьбой, но и увеличивать срок служ30
25
бы резьбового соединения при любых
22
12
статических и динамических нагруз17
6
ках (рис. 7.6)63.
13
3
10
Для ещё более прочной посадки
2
8
и соответственно ещё более надёжного резьбового соединения, выпускаются специальные, блокирующиеся резьбовые вставки (такие вставки
имеют другой цвет, отличный от
стандартных – обычно красный)
(рис. 7.7)64.
Рис. 7.6. Распределение нагрузок, %:
а – с резьбовой пружинной вставкой;
От обычных вставок блокируюб – в обычной резьбе
щиеся отличаются тем, что один из
витков выполнен в форме шестигранника. Именно это предотвращает не только выкручивание резьбовой вставки вместе с болтом, но и полностью самопроизвольное выкручивание её при вибрациях и цикличных температурных изменениях.
Применение пружинных резьбовых вставок даёт конструктору свободу
в выборе материала и его толщины. Благодаря уменьшению напряжений в
резьбовом соединении, конструктор может подбирать крепёжные элементы размером меньше, чем обычно без применения вставок (рис. 7.8)65.
63
Там же.
Там же.
65
Там же.
64
74
Рис. 7.7. Блокирующаяся резьбовая вставка
а
б
Рис. 7.8. Эпюра распределения напряжений при применении:
стандартной резьбы (а); резьбовой пружинной вставки (б)
Из-за уменьшения места соединения и сокращения размера, например
болта, а также экономии материала, рабочего пространства и веса при одинаковых или более высоких требованиях, предъявляемых к резьбовому соединению, достигается значительное сокращение финансовых затрат.
Заслуживает внимания ещё одно применение резьбовых вставок –
лёгкий переход с одной резьбы на другую, например с дюймовой на
метрическую.
Одним из примеров использования резьбовой пружиной вставки является компания «Вюрт, которая использует технологию восстановления
поврежденной резьбы «TIME-SERT»66. Её ключевым элементом является тонкостенная резьбовая втулка с наружной и внутренней резьбой.
Диаметр резьбы при этом не изменяется67.
66
TIME-SERT – совершенная технология восстановления резьбы: энциклопедия [Электронный ресурс]. Вюрт. Владивосток: Wurth. Режим доступа:
http://www.wunerthmarket.ru/paedia/time-sert/
67
Там же.
75
ВОПРОСЫ ДЛЯ САМОКОНТРОЛЯ
1. В чем заключается технология восстановления детали пластической деформацией (давлением)?
2. В чем заключается технология восстановление деталей обработкой под ремонтный размер?
3. В чем заключается технология восстановления путем постановки
добавочной детали?
4. Опишите порядок восстановления путем постановки добавочной
детали.
5. Опишите схему установления категорийных размеров для детали.
6. Опишите схему установления пригоночных размеров для детали.
7. Укажите методы восстановления резьбы в детали.
8. Опишите технологию восстановления резьбовыми вставками и
втулками.
9. Опишите технологию восстановления резьбы при помощи проволочных пружинных вставок.
10. Какими преимуществами обладает метод восстановления резьбы
при помощи пружинных вставок?
Рекомендуемая литература: [32, 34, 35] (см. Библиографический список).
8. ВОССТАНОВЛЕНИЕ РАБОТОСПОСОБНОСТИ ДЕТАЛЕЙ
ЭЛЕКТРОФИЗИЧЕСКИМИ СПОСОБАМИ
8.1. Восстановление деталей электрической сваркой и наплавкой
8.1.1. Определение свариваемости сплавов
Под свариваемостью понимается сочетание технологических свойств
образовывать в процессе сварки соединения, отвечающие конструктивным и эксплуатационным требованиям, предъявляемым к сварным соединениям68.
В общем случае свариваемость материала есть комплексное свойство, определяемое его составом и физическими свойствами.
Наиболее сильное влияние на свариваемость оказывают химический
состав металла, теплофизические и механические свойства, а также специальные физико-химические свойства, которые определяют активность реакций, протекающих в сварочной ванне и зоне термического влияния.
68
Бабенко Э.Г. Разработка технологических процессов восстановления и упрочнения деталей: учеб. пособие. Хабаровск: Изд-во ДВГУПС, 2016. 108 с.
76
Общим недостатком для металла, нагреваемого при сварке в зоне
термического влияния до температуры выше температуры фазовых
превращений, является образование в закаливающихся сплавах закалочных структур, что приводит к снижению пластических свойств и хрупкому разрушению как в процессе формирования сварного соединения
(холодные трещины), так и в процессе эксплуатации изделий.
Для углеродистых сталей с содержанием углерода более 0,25 %,
низко- и среднелегированных сталей, титановых сплавов и других образование представляет наибольшую опасность. закалочных структур.
Следует отметить, что при одинаковом содержании углерода чувствительность стали к образованию закалочных структур и склонность к образованию трещин тем выше, чем больше в них содержится легирующих
элементов, степень влияния которых не одинакова и может быть оценена
по различным признакам, один из них – эквивалент по углероду Сэ , показывающий чувствительность сварного соединения к образованию холодных трещин. Наиболее часто для его расчета используется следующая формула
Ni Cu Mn Cr V Mo P
Сэ С
.
(8.1)
15 13
6
5 5
4
2
При величине Сэ 25 предварительного нагрева зоны сварки не
требуется, однако после сварки желательна термообработка для снятия
внутренних напряжений.
Если Сэ находится в пределах 0,25–0,35 желателен подогрев перед
сваркой с обязательной термообработкой после нее.
При Сэ = 0,35–0,45 необходим подогрев перед сваркой, желателен сопутствующий сварке подогрев и обязательная термообработка после нее.
В случае, если Сэ 45 , требуется создание термического цикла сварки, устраняющего образование закалочных структур (предварительный и
сопутствующий подогревы, сварка короткими участками, термическая обработка сварного соединения непосредственно после сварки и т. д.).
Необходимо применение мер для снижения содержания водорода в металле сварного соединения (тщательная подготовка поверхностей кромок,
использование флюсов и электродных покрытий с низким содержанием
водорода и его соединений и др.). Желательно использование технологических приемов, снижающих остаточные напряжения (сварка каскадом,
применение приспособлений, создающих напряжения сжатия и т. д.).
Температура предварительного подогрева свариваемого изделия
рассчитывается по формуле
77
Т 350 Соб 0, 25 ,
(8.2)
где Соб – общий эквивалент по углероду.
Соб Сэ 1 0,005 S ,
(8.3)
где S – толщина свариваемого металла.
Чувствительность сварного соединения к образованию горячих трещин HCS определяется по формуле
HCS
C S P Si / 25 Ni / 100 3
10 .
3Mn Cr Mo V
(8.4)
Если HCS 4 , то горячие трещины в сварном шве не образуются.
Для высокопрочных сталей значительной толщины необходимо, чтобы
значения HCS были менее 1,6–2,0.
Показателем, указывающим на охрупчивание стали из-за структурных превращений, является твердость зоны термического влияния. Для
углеродистых и низколегированных сталей твердость зоны термического
влияния должна быть не выше HV 350. Возможная максимальная твердость определяется расчетным путем69:
HVmax 90 1050 C 47 Si 75 Mn 30 Ni 31Cr .
(8.5)
8.1.2. Подготовка к сварочно-наплавочным работам
В зависимости от характера сварочно-наплавочных работ выполняются следующие подготовительные операции: зачистка места сварки
или наплавки металлическими щётками; удаление загрязнений, ржавчины, остатков масел. При наличии на детали отверстий, шпоночных канавок их необходимо закрыть пробками или временными шпонками из малоуглеродистой стали.
Концы трещин выявляются нагревом, накерниваются, затем производится их засверловка.
Подготовку кромок под сварку следует выполнять механической обработкой (на токарном или строгальном станке, фрезерованием, пневматическим или ручным зубилом, крейцмейселем и др.). При подготовке кромок
у деталей из малоуглеродистой стали разрешается использовать газовую
резку с последующей механической зачисткой поверхности реза до получения чистого металла. При подготовке кромок газовой резкой на деталях
из сталей, содержащих более 0,3 % углерода, поверхность реза необходимо обработать механическим способом на глубину не менее 3 мм.
69
Бабенко Э.Г. Указ. соч.
78
При выборе формы разделки кромки (рис. 8.1)70 следует иметь в виду, что наиболее экономичной является I-образная без скоса кромок.
В сравнении с V-образной более экономичными являются Х-образные
двухсторонние формы разделки кромки. Однако они могут быть реализованы в случае возможности доступа к обеим сторонам детали.
hb
б
b
Fн
в
Fк
b3
е
α°
Fн
5
4
3
2
Fн
Fн(с)
1
bз
2
ж
з
b
Fн
b
с
h
hb
К
b
α°
hп
д
h
Fн
hb
г
1
h
h
Fн
hп
а
Рис. 8.1. Размеры и форма разделки кромок и сварного шва: а – I-образная (без
скоса кромок), односторонний стыковой шов; б – то же с металлической (остающейся) подкладкой 1; в – I-образная разделка кромок (без скоса кромок), двухсторонний стыковой шов; г – V-образная разделка кромок, стыковой шов с подваркой
корня шва 2; д – V-образная разделка кромок, многопроходной стыковой шов (цифры
указывают номер прохода – слоя); е – Х-образная разделка кромок, двухсторонний
стыковой шов; ж – угловой шов (без скоса кромки вертикального элемента); и – расположение валиков при наплавке
При заварке несквозных трещин чаще всего используется V-образная
разделка, при заварке сквозных – Х-образная.
Площадь поперечного сечения шва определяется геометрическим
расчетом. При этом высота усиления шва hв при сварке назначается в
пределах 0,1–0,3 толщины металла детали , а при заварке трещины –
0,2–0,3 от глубины трещины.
70
Бабенко Э.Г. Указ. соч.
79
Размеры валиков при однопроходной сварке можно принять 0,3–0,7 см2.
Сечение первого слоя при многопроходной заварке трещины не
должно превышать 0,3–0,35 см2.
При многослойной наплавке наложение последующих слоев необходимо проводить после полного остывания предыдущих и зачистки последних до металлического блеска71.
8.1.3. Выбор источника питания
Сварочная дуга является мощным дуговым разрядом в ионизированной
среде газов и паров металла. Характеристиками дуги являются ее ток Iд
и напряжение Uд . Статическая вольт-амперная характеристика дуги
(рис. 8.2)72 показывает зависиUд, В
мость Uд f Iд при постоянной
длине дуги ( Lд const ). Она
II
III
I
имеет три характерных участка:
1) падающий I; 2) жесткий II;
L1д
Тебе могут подойти лекции
А давай сэкономим
твое время?
твое время?

Дарим 500 рублей на первый заказ,
а ты выбери эксперта и расслабься

Включи камеру на своем телефоне и наведи на Qr-код.
Кампус Хаб бот откроется на устройстве
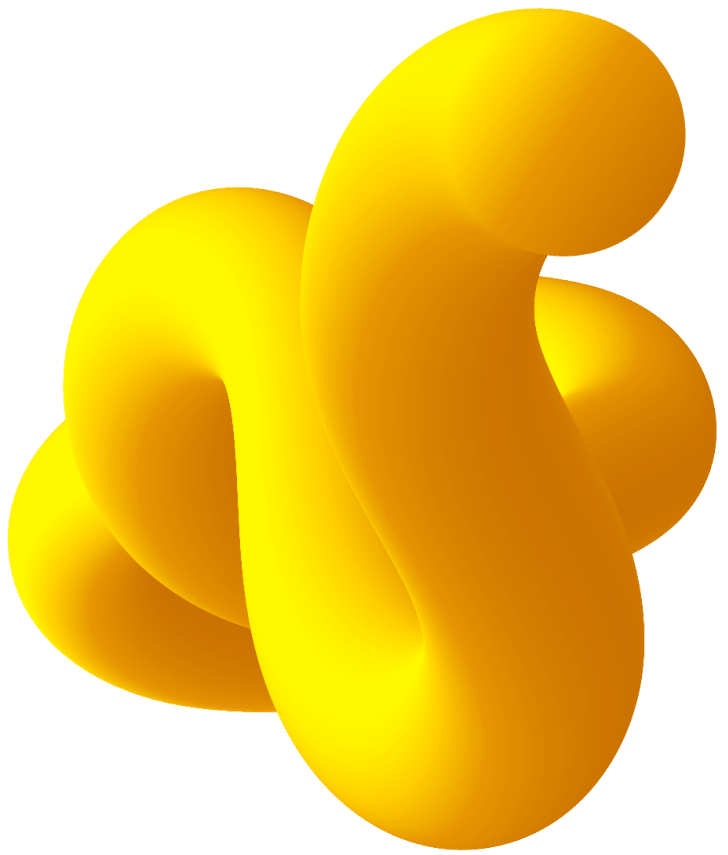
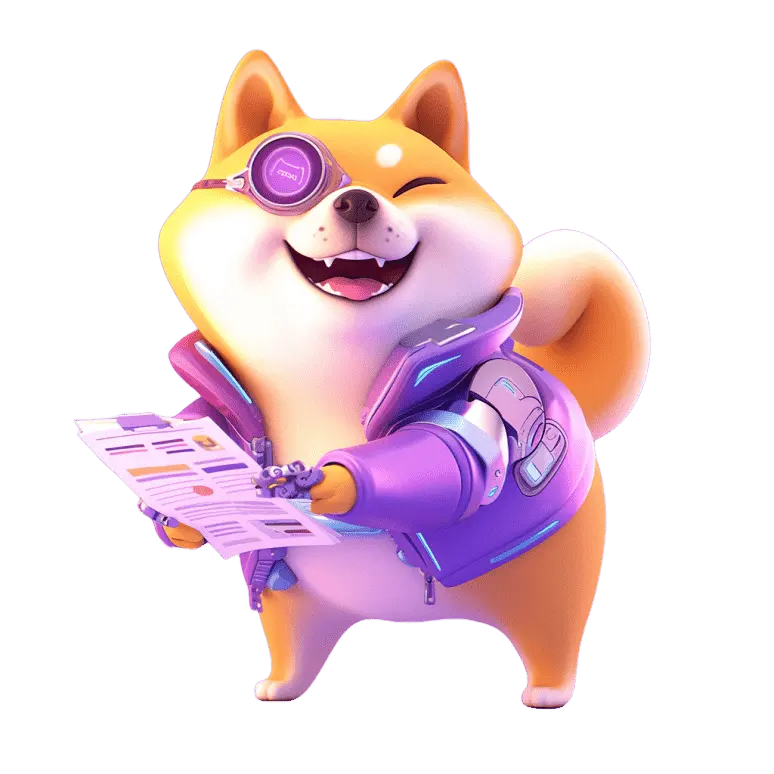
Не ищи – спроси
у ChatGPT!
у ChatGPT!
Боты в Telegram ответят на учебные вопросы, решат задачу или найдут литературу
Попробовать в Telegram

Оставляя свои контактные данные и нажимая «Попробовать в Telegram», я соглашаюсь пройти процедуру
регистрации на Платформе, принимаю условия
Пользовательского соглашения
и
Политики конфиденциальности
в целях заключения соглашения.
Пишешь реферат?
Попробуй нейросеть, напиши уникальный реферат
с реальными источниками за 5 минут
с реальными источниками за 5 минут
Основы технологии производства и ремонта подвижного состава

Хочу потратить еще 2 дня на работу и мне нужен только скопированный текст,
пришлите в ТГ