Теория обработки металлов давлением
Выбери формат для чтения
Загружаем конспект в формате pdf
Это займет всего пару минут! А пока ты можешь прочитать работу в формате Word 👇
МИНОБРНАУКИ РОССИИ
ФЕДЕРАЛЬНОЕ ГОСУДАРСТВЕННОЕ БЮДЖЕТНОЕ ОБРАЗОВАТЕЛЬНОЕ
УЧРЕЖДЕНИЕ ВЫСШЕГО ПРОФЕССИОНАЛЬНОГО ОБРАЗОВАНИЯ
«САМАРСКИЙ ГОСУДАРСТВЕННЫЙ АЭРОКОСМИЧЕСКИЙ УНИВЕРСИТЕТ
ИМЕНИ АКАДЕМИКА С.П.КОРОЛЕВА
(НАЦИОНАЛЬНЫЙ ИССЛЕДОВАТЕЛЬСКИЙ УНИВЕРСИТЕТ)»
М. Г. Лосев
Конспект лекций по курсу
«Теория обработки металлов давлением»
Электронное учебное пособие
САМАРА
2011
Автор: Лосев Михаил Григорьевич
Лосев, М. Г. Конспект лекций по курсу «Теория обработки металлов давлением»
[Электронный ресурс] : электрон. учеб. пособие / М. Г. Лосев; Минобрнауки России,
Самар. гос. аэрокосм. ун-т им. С. П. Королева (нац. исслед. ун-т). - Электрон. текстовые и
граф. дан. (1,95 Мбайт). - Самара, 2011. - 1 эл. опт. диск (CD-ROM).
Теория ОМД развивается в трех направлениях: механико-математическом,
физическом и физико-химическом. Эти направления тесно связаны между собой и
взаимно дополняют друг друга и рассмотрены в данном учебном пособии.
Пособие предназначено для бакалавров инженерно-технологического факультета,
обучающихся по направлению 150700.62 «Машиностроение» по дисциплине «Основы
теории обработки металлов давлением» и по направлению 150400.62 «Металлургия» для
«Теория обработки металлов давлением» для 6 семестра.
Подготовлено на кафедре обработки металлов давлением.
© Самарский государственный
аэрокосмический университет, 2011
2
СОДЕРЖАНИЕ
ВВЕДЕНИЕ .............................................................................................................. 4
1. Краткие сведения об основных технологических процессах ОМД ............ 7
2. Природа пластической деформации ............................................................. 14
2.1. Строение металлов ................................................................................... 14
2.2. Пластическая деформация монокристалла ............................................ 17
2.2.1.
Скольжение ................................................................................................. 17
2.2.2. Влияние ориентации плоскости скольжения на величину касательного
напряжения при пластической деформации ........................................................ 19
2.2.3.
Двойникование............................................................................................ 23
2.2.4.
Типы дислокаций и их роль в процессе пластической деформации ... 24
3. Кривые упрочнения ........................................................................................ 29
3.1. Определение .............................................................................................. 29
3.2. Индикаторная диаграмма......................................................................... 33
3.3. Диаграмма условных напряжений .......................................................... 36
3.4. Диаграмма истинных напряжений.......................................................... 41
3.5. Кривые упрочнения .................................................................................. 43
3.6. Свойства кривых упрочнения I рода ...................................................... 44
3.7. Свойства кривых упрочнения II рода ..................................................... 46
3.8. Построение диаграмм истинных напряжений ...................................... 48
3.9. Проверка правильности построения кривых упрочнения .................... 51
3.10. Аппроксимация кривых упрочнения. Определение коэффициентов
аппроксимирующих зависимостей .................................................................. 52
3.11.
Свойства «единых» кривых упрочнения ............................................ 57
3.12. Кривые упрочнения металлов, подвергнутых динамическому
нагружению ........................................................................................................ 57
3
ВВЕДЕНИЕ
Теория обработки металлов давлением (ОМД) – прикладная
инженерная дисциплина. Она базируется на основных положениях механики
сплошных сред и физики металлов.
Основной задачей дисциплины «Теория ОМД» является [ ] анализ
и разработка общих принципиальных основ рационального построения
процессов ОМД. Это дает возможность не только проектирования новых
технологических процессов, но и предвидение возможных их нарушений, а
следовательно принятие обоснованных мер для устранения последних.
Теория ОМД рассматривает и изучает следующие вопросы:
-
термические
и
механические
условия,
при
которых
обеспечивается наивысшая пластичность металла и тем самым возможность
максимальной деформации в конкретной операции ОМД;
- влияние обработки давлением на механические и физические
свойства металлов в целях получения наилучших эксплуатационных
характеристик заготовок и деталей;
- характер формоизменения заготовок при различных операциях
ОМД в целях отыскивания наиболее благоприятных соотношений между
размерами и формой исходных заготовок, а также между заготовкой и
готовой деталью;
-
сопротивление
металлов
пластическим
деформациям
при
операциях ОМД с целью определения необходимых усилий и работ для
осуществления этих операций, в целях правильного выбора прессового
оборудования и прочностного расчета штамповой оснастки.
В настоящее время считается бесспорным, что пластичность
является свойством металлов и зависит от температуры (термические
условия), скорости и степени деформации, схемы напряженного состояния,
внешнего трения (механические условия).
4
Влияние температуры на пластическую деформацию всегда
рассматривают в совокупности со скоростью деформации. С увеличением
температуры пластичность металла увеличивается. Однако увеличение
скорости деформации может привести к снижению пластичности, несмотря
на высокую температуру металла.
Пластическая
деформация
является
эффективным
способом
изменения механических и физических свойств металлов. Пластической
деформацией можно увеличить прочность сплавов, которые термически не
упрочняются. Также пластическая деформация приводит к изменению
электропроводности, коррозионной стойкости, магнитных свойств металлов
и сплавов.
Теория
ОМД развивается в трех направлениях:
механико-
математическом, физическом и физико-химическом. Эти направления тесно
связаны между собой и взаимно дополняют друг друга.
Механико-математическое направление изучает распределение
напряжений и деформаций в пластически деформируемом теле и условия
перехода упругой деформации в пластическую.
Физическое направление теоретически и экспериментально изучает
механизм перехода пластической деформации с учетом анизотропии,
обусловленной кристаллическим строением металлов. Также исследуют
влияние различных факторов на процесс пластической деформации, в
основном температуры, степени и скорости деформации, вида напряженного
состояния, внешнего трения.
Физико-химическое направление изучат связь химического состава
и фазового состояния металла на процесс пластической деформации.
Химический состав и фазовое состояние оказывают большое влияние на
пластичность и сопротивление деформации. В процессе пластической
деформации тела изменяются структура и фазовый состав, а также
происходят химические превращения.
5
Обработка металлов давлением является завершающим этапом в
производстве изделий из металлов и сплавов. Назначение данного этапа
заключается в том, чтобы изменить геометрическую форму и размеры тела, а
также придать ему определенные механические и физические свойства. Эта
же цель в той или иной мере может быть достигнута и иными путями,
главными из которых являются литье и обработка резаньем. Вопрос о выборе
вида обработки металлов для получения изделий с необходимыми
механическими и физико-химическими свойствами определяется техникоэкономическими соображениями применительно к конкретным условиям
производства.
Типичным является применение всех трех упомянутых способов
обработки в такой последовательности: литье; обработка давлением;
обработка резаньем (по возможности в качестве отделочной операции).
6
1. Краткие сведения об основных технологических процессах ОМД
В данном разделе рассматриваются краткие сведения о технологических
процессах ОМД, которые будут использованы при изложении данного курса.
Детально теорию и технологию этих процессов будут рассматривать в
разделах соответствующих специальных курсов.
Прокатка металла. Сущность процесса прокатки заключается в том, что
заготовка или слиток вследствие сил трения втягивается вращающимися
валками в зазор между ними и обжимается. При этом изменяются форма и
размеры поперечного сечения тела и, как правило, увеличиваются его
продольные размеры. Существуют три основных способа прокатки,
имеющих определенное отличие по характеру выполнения деформации:
продольная, поперечная и поперечно-винтовая прокатка.
При продольной прокатке деформация металла осуществляется между
вращающими в разные стороны валками (рисунок 1.1). При продольной
прокатке заготовка в поперечном сечении приобретает форму зазора между
валками (сортовой, листовой прокат).
При поперечной прокатке (рисунок 1.2) оси прокатных валков и
прокатываемого тела параллельны (или пересекаются под небольшим углом).
Оба валка вращаются в одном направлении, а заготовка круглого сечения – в
противоположном. В процессе поперечной прокатки обрабатываемое тело
удерживается в валках с помощью специального приспособления.
1-верхний валок; 2-прокатываемая полоса; 3-нижний валок
Рисунок 1.1- Схема продольной прокатки
7
Обжатие заготовки по диаметру и придание ей требуемой формы
сечения
обеспечивается
соответствующей
профилировкой
валков
изменением расстояния между ними. Данным способом изготавливают
изделия, представляющие собой тела вращения: шары, оси, шестерни и пр.
1-верхний валок; 2-прокатываемое изделие; 3-нижний валок
Рисунок 1.2-Схема поперечной прокатки
Волочение металла – это протягивание прутка круглого сечения или
другой формы через отверстие волочильного очка (волоку), выходящие
размеры сечения которого меньше сечения исходного продукта. Волочение
выполняется
тяговым
усилием,
приложенным
к
обрабатываемого тела (рисунок 1.3).
1-волока; 2-пруток
Рисунок 1.3-Схема процесса волочения
8
переднему
концу
Данным способом получают проволоку всех видов, прутки с высокой
точностью поперечных размеров и трубы разнообразных сечений.
Прессование металла. При прессовании металл, заключенный в контейнер,
выдавливается через отверстие в матрице и получает форму поперечного
сечения, соответствующего форме отверстия матрицы
(рисунок 1.4).
1-контейнер; 2-пресс-штемпель; 3-заготовка; 4-матрица;
5-прессизделие
Рисунок 1.4-Схема прессования с прямым истечением
Прессованием получают разнообразный сортамент профилей, прутков,
труб из цветных и черных металлов.
Различают несколько видов прессования: с прямым, обратным,
боковым и комбинированным истечением.
Ковка и объемная штамповка. При свободной ковке деформация
металла осуществляется между бойками. Нижний боек неподвижен, верхний
совершает возвратно-поступательное движение. В результате многократного
воздействия инструмента заготовка приобретает
необходимую форму и
размеры изделия. Основными операциями ковки являются: осадка, высадка,
прошивка, протяжка и т.д.
9
Осадкой называют формоизменяющую операцию, в процессе которой
производится уменьшение высоты заготовки при увеличении площади ее
поперечного сечения (рисунок 1.5).
1-верхний боек; 2-заготовка; 3-нижний боек
Рисунок 1.5-Схема процесса осадки
Осадка заготовки или слитка с хвостовиком (высадка) для получения
поковок с местным утолщением. В качестве инструмента применяют плоские
и вогнутые плиты, причем в нижней плите есть отверстие для хвостовика
(рисунок 1.6).
Протяжкой называют формоизменяющую операцию, в процессе
которой производится удлинение заготовки или ее части за счет уменьшения
площади
поперечного
сечения.
Протяжка
способствует
устранению
внутренних
1-верхний боек; 2-заготовка; 3-подклодное кольцо; 4-нижний боек
Рисунок 1.6-Схема процесса высадки
10
дефектов (пустот) и улучшает механические свойства металла в осевом
направлении заготовки.
Протяжка производится на плоских бойках, в вырезных бойках,
протяжка на оправке (рисунок 1.7).
1-верхний боек; 2-заготовка; 3-нижний боек; 4-оправка
Рисунок 1.7-Схемы процесса протяжки: а) протяжка на плоских бойках; б)
протяжка в вырезных бойках; в) протяжка на оправке
Прошивка - это получение полостей в заготовке за счет вытеснения
материала. Прошивка бывает открытой и закрытой. При открытой прошивке
боковая поверхность заготовки является свободной, при закрытой - заготовка
заключена в контейнер, определяющий ее наружный диаметр после
прошивки.
1-верхний боек; 2-заготовка; 3-прошивень; 4-нижний боек
Рисунок 1.8-Схема процесса свободной прошивки
11
Схема процесса свободной прошивки представлена на рисунке 1.8.
При объемной горячей штамповке заготовку помещают в полость
одной части штампа и под действием другой части штампа, заготовка
деформируется и заполняет полость, принимая ее форму. Различают два вида
объемной штамповки: открытую (рисунок 1.9) и закрытую (рисунок 1.10). В
закрытой объемной штамповке объем заготовки равен объему детали. В
открытой объемной штамповке объем заготовки больше объема детали и
часть металла, по мере заполнения полости штампа, вытекает в заусенец.
1-верхняя часть штампа; 2-изделие; 3-заусенец; 4-нижняя часть штампа
Рисунок 1.9-Схема открытой объемной штамповки
1-верхняя часть штампа; 2-изделие; 3-нижняя часть штампа
Рисунок 1.10-Схема закрытой объемной штамповки
12
Листовая штамповка представляет собой процесс получения полых
изделий из листового, ленточного и полосового металла без значительного
изменения толщины заготовки.
Основные операции листовой штамповки - вытяжка без утонения
стенки, гибка, отбортовка, обжим, раздача и другие операции. Некоторые
операции листовой штамповки представлены на рисунке 1.11.
Рисунок 1.11- Схемы операций листовой штамповки: а) вытяжка без
утонения стенки; б) гибка; в) отбортовка; г) обжим
Многообразие по форме и размерам получаемых листовой штамповкой
изделий определяет значительное количество штамповочных операций,
отличающихся характером изменения формы заготовки, а следовательно, и
условиями деформации металла при выполнении данной технологической
операции.
13
2. Природа пластической деформации
2.1.
Строение металлов
Все металлы и сплавы имеют кристаллическое строение. Оно
характеризуется закономерным и периодичным расположением атомов в
пространстве, при котором каждый атом находится в идентичном окружении
соседних.
Рентгенограммы металлов показывают, что атомы в них расположены
по
прямым
линиям
и
по
плоскостям
образуя
пространственную
кристаллическую решетку.
Кристаллическая решетка представляет собой трехмерную сетку из
прямых линий. В точках пересечения линий, называемых узлами, размещены
атомы. Точнее, узлы являются центрами, относительно которых происходят
тепловые колебания атомов. Пространственная кристаллическая решетка
состоит из элементарных ячеек.
Большинству
промышленных
металлов
свойственны
три
типа
кристаллических решеток (рисунок 2.1):
- объемно-центрированную кубическую (ОЦК) решетку;
- гранецентрированную кубическую (ГЦК) решетку;
- гексагональную плотноупакованную (ГПУ) решетку.
Решетку ОЦК имеют, например, металлы:
и железо, ванадий, вольфрам, молибден, хром, тантал, литий и
другие.
Решетку ГЦК имеют металлы: железо, медь, алюминий, никель,
свинец, кобальт, серебро, золото, платина и другие.
Решетка ГПУ свойственна бериллию, кадмию, кобальту, титану,
цинку и другим металлам.
14
Рисунок 2.1 – Типы пространственных решеток: а) объемно-центрированная
кубическая; б) гранецентрированная кубическая;
в) гексагональная плотноупакованная
Позволяющее
большинство
металлов,
применяемых
в
машиностроении, имеют решетку указанных трех типов. Исключением
являются олово, марганец, церий, имеющие тетрагональную решетку, и
мышьяк,
сурьма,
висмут,
кристаллизирующиеся
в
ромбоэдрическую
решетку. Как показывают сами названия, базой решетки последних двух
типов являются треугольник и ромб.
Для
определения
плоскостей,
которые
можно
провести
в
кристаллической решетке, а также для определения кристаллографических
направлений принята система индексаций.
Кристаллографические плоскости обозначаются тремя или четырьмя
цифрами в круглых скобках. Цифры представляют собой обратную величину
отрезков отсекаемых на координатных осях (рисунок 2.2). Единица
измерений - параметр решетки (расстояние между узлами).
Индексация
кристаллографических
направлений
осуществляется
следующим образом. Линию направления переносят в начало координат.
Положение прямой в пространстве определяется координатами первого
15
атома, лежащего на этой прямой. Координаты атома записываются в
квадратные скобки (рисунок 2.3). Единица измерения – параметр решетки.
Рисунок 2.2 – Индексация кристаллографических плоскостей
Рисунок 2.3 – Индексация кристаллографических направлений
Если для всего объема кристаллического тела характерно постоянство
кристаллографических направлений, то тело называют монокристаллом.
16
Монокристалл обладает анизотропией свойств, т.к. расстояние между
атомами в разных направлениях различные.
Все технические металлы имеют поликристаллическое строение, т.е.
представляют собой множество спаянных между собой кристаллитов (зерен)
неправильной формы. Нерастворимые примеси, чаще всего окислы и
силикаты, располагаются по границам спайности зерен, образуя так
называемое межкристаллическое (межзеренное) вещество. Форма и размеры
зерен зависят от условий кристаллизации и последующей обработки. Зерна
ориентированы совершенно произвольно. Разнообразная и беспорядочная
ориентировка кристаллографических направлений в различных зернах
поликристаллического тела позволяет рассматривать тело как изотропное.
2.2.
Пластическая деформация монокристалла
Для понимания процессов деформации реальных металлов, являющихся
поликристаллическими
телами,
целесообразно
вначале
рассмотреть
закономерности деформации монокристаллов.
Экспериментально установлено, механизмами пластической деформации
кристаллов
являются
скольжение
(трансляция)
и
двойникование.
Преобладающим механизмом, свойственным кристаллам с кубической и
гексагональной решеткой, является скольжение.
2.2.1. Скольжение
Скольжение представляет собой параллельное смещение тонких слоев
монокристалла относительно друг друга. Движение охватывает ряд
плоскостей или тончайших слоев (полосы скольжения), в промежутках
между которыми элементы пластической деформации отсутствуют.
(рисунок 2.4).
17
Экспериментально установлено, что полосы скольжения отстоят одна от
другой в среднем на расстоянии около 1 мкм [ ], в то время как расстояния
между соседними атомными плоскостями выражаются величиной порядка
1104 мкм .
1-участок отсутствия скольжения; 2-участок скольжения
Рисунок 2.4 - Схема пластического скольжения при деформации
монокристалла
Скольжение
происходит
по
кристаллографическим
плоскостям,
которые называются плоскостями скольжения. Плоскостями скольжения
обычно являются плоскости с наибольшей плотностью размещения атомов, а
направлениями скольжения являются направления, по которым межатомные
расстояния имеют минимальную величину.
Например, в металлах с решеткой ОЦК плоскостями скольжения
являются плоскости типа (111), а направлениями скольжения направления
типа [101].
18
В металлах с решеткой ГЦК скольжение может осуществляться по
плоскостям несколько типов (112), (123) и (110). Направлениями скольжения
является направление [111].
В металлах с решеткой ГПУ плоскостью скольжения обычно бывает
плоскость
(0001),
шестиугольника
а
направлением
[1120].
С
скольжения
повышением
является
температуры
диагональ
увеличиваются
амплитуды колебаний атомов, и в металлах с решеткой ГПУ появляется
возможность скольжения по плоскостям типа 1011 и 1012 .
Внешним проявлением скольжения в металлах обычно считают линии
скольжения или линии Чернова-Людерса, наблюдаемые на практике. Если
поверхность образца или заготовки полированная или покрыта твердой
окисной пленкой, то в месте выхода плоскости скольжения на поверхность,
образуется
микротрещина. Совокупность
таких
трещин
приводит к
образованию сетки, состоящей из двух семейств линий, пересекающихся под
прямым углом друг с другом. Впервые эти линии описаны В.Людерсом и
Д.Черновым.
2.2.2. Влияние ориентации плоскости скольжения на величину
касательного напряжения при пластической деформации
Рассмотрим растяжение образца из монокристалла усилием Р. Площадь
поперечного сечения образца обозначим через F0. Плоскость скольжения,
площадью F, расположим произвольно, у которой нормаль с осью образца
составляет угол (рисунок 2.5).
Рисунок 2.5 – Схема к определению касательного напряжения при
растяжении монокристалла
19
Величина
касательного
напряжения
в
плоскости
скольжения
определяется из выражения:
где - угол между направлением скольжения и силой Р.
В свою очередь FF0/cos, тогда:
Величина P/F0=1, где 1 – нормальное напряжение действующее вдоль
образца. Следовательно:
Для того, чтобы началась пластическая деформация при линейном
напряженном состоянии, нормально напряжение 1 должно достигнуть
предела текучести s. Тогда касательное напряжение достигает критического
значения кр. Отсюда выражение (2.1) можно переписать в виде:
Касательное напряжение, необходимое для начала пластической
деформации, величина постоянная для данного металла, при данной
температуре и скорости деформации кр=const, не зависящая от ориентировки
плоскостей скольжения относительно действующих на тело сил. Построим
график зависимости
(рисунок 2.6).
20
Рисунок 2.6 – Зависимость предела текучести монокристалла от
ориентировки плоскостей скольжения
Из графика видно, что величина предела текучести монокристалла для
каждого металла существенно зависит от ориентировки плоскостей
скольжения относительно направления действия сил, имея минимум при
углах ==45.
Результаты
(сопротивления
экспериментального
деформации)
от
определения
ориентировки
зависимости
монокристалла
с
гексагональной решеткой нанесены в виде точек на рисунке 2.6.
Совокупность
плоскости
и
направления
скольжения
называют
системой скольжения. При наличии нескольких систем скольжения в
монокристалле сдвиг начинается в плоскости, наиболее благоприятно
расположенной относительно действующей силы. Как было показано,
касательное напряжение достигает максимального значения в плоскости
расположенной под углом 45 к действующей силе. Следовательно,
скольжение начинается в плоскости скольжения, нормаль к которой образует
21
45 с осью растяжения или сжатия. Тогда угол между осью образца и
направлением скольжения будет равен также 45.
При
деформации
монокристалла
происходит
поворот
систем
скольжения. При растяжении угол между нормалью к плоскости скольжения
и направлением оси растяжения увеличивается и направление скольжения
приближается к оси растяжения. Это видно на модели растяжения
монокристалла с решеткой ГПУ (рисунок 2.7).
При сжатии угол между нормалью к плоскости скольжения и
направлением сжимающей силы уменьшается (рисунок 2.8).
Рисунок 2.7 – Схема скольжения при растяжении монокристалла: а –
исходное положение; б – после растяжения
Рисунок 2.8 – Поворот плоскостей скольжения при сжатии
22
Поворот
систем
скольжения
приводит
к
тому,
что
система,
расположенная сначала благоприятно (углы и близки к 45), занимает
неблагоприятное
положение,
при
этом
касательные
напряжения
уменьшаются. В то же время другая возможная система скольжения
вследствие поворота приближается к благоприятному положению.
2.2.3. Двойникование
Наряду с основным механизмом пластической деформации металлов –
скольжением
в некоторых
металлах
деформация
происходит путем
двойникования.
Двойникование представляет собой смещение атомов, расположенных в
плоскостях, параллельных некоторой плоскости, называемой плоскостью
двойникования,
на
расстояния,
пропорциональные
расстоянию
этих
плоскостей от плоскости двойникования (рисунок 2.9).
При
двойниковании
симметричное
двойникования.
остальной
части
кристалла
части
Двойникование
переходят
кристалла
редко
в
относительно
наблюдается
при
положение,
плоскости
статическом
нагружении и значительно чаще при деформации ударом.
При
двойниковании
не
происходит
непрерывного
изменения
ориентировки плоскостей, как при скольжении. Переход решетки в новое
положение
происходит
почти
мгновенно
и
сопровождается
часто
характерным потрескиванием. Двойникование может возникнуть не только
при воздействии внешних сил на деформируемое тело, но и в результате
отжига после пластической деформации. Такое явление наблюдается, в
частности, у меди, латуни и некоторых других металлов с решеткой ГЦК.
23
Рисунок 2.9 – Перемещение решетки при двойниковании: а – до деформации;
б – после деформации
Плоскостями двойникования являются плоскости (112) у металлов с
решеткой ОЦК, для металлов с решеткой ГЦК – плоскость (111) и для
металлов с решеткой ГПУ – плоскость (10 2).
Двойникованием может быть получена незначительная степень
деформации.
Этот
механизм
сопутствует
основному
механизму
–
скольжению.
2.2.4. Типы дислокаций и их роль в процессе пластической деформации
Скольжение в металлических кристаллах нельзя рассматривать как
одновременный сдвиг одной части монокристалла относительно другой по
всей плоскости скольжения. Расчеты показывают, что для такого смещения в
идеальном кристалле необходимо создать напряжения в сотни раз
превышающие величины, найденные из опыта. В таблице 2.1 приведены
фактические
и
теоретические
значения
напряжения при скольжении [ ].
24
критического
касательного
Большая разница между теоретической и действительной величинами
критического
касательного
напряжения
при
деформации
кристаллов
приводит к выводу, что представление о механизме скольжения как
одновременном
сдвиге
по
плоскости
скольжения
не
соответствуют
действительной картине процесса.
Таблица 2.1 – Фактические и теоретические значения критического
касательного напряжения при скольжении
Металл
Фактическое
значение Теоретическое значение
кр, МПа
кр, МПа
Алюминий
1,2 – 2,4
900
Медь
10,0
1540
Никель
5,8
2600
Железо
29,0
2300
Отличие фактических значений кр от теоретических объясняется тем,
что в реальных кристаллах имеются места ослабленных связей между
атомами, обусловленных несовершенствами кристаллической решетки.
В реальных металлах присутствуют дефекты кристаллического
строения четырех типов:
- точечные (вакансии и внедренные атомы посторонних примесей);
- линейные (дислокации);
- поверхностные (границы зерен, границы двойников, границы фаз);
- объемные (пустоты и различные объемные включения).
Возможность последовательного смещения отдельных групп атомов
вдоль плоскости скольжения при уменьшенных напряжениях возникает
вследствие наличия линейных дефектов кристаллической решетки –
дислокаций.
25
Появление элементов теории дислокаций относится к 20-м годам
прошлого столетия (работы Я.И.Френкиля, Дж.Тейлора, Е.Орована и др.).
однако
экспериментальное
подтверждение
существования
дислокаций
получено лишь в 50-х годах благодаря развитию экспериментальных средств
исследования строения кристаллов. Существование дислокаций было
подтверждено как прямыми методами исследования (с помощью ионного
проектора,
рентгеновской
топографии,
электронно-микроскопического
исследования), так и косвенными методами исследования (метод ямок
травления, муаровых фигур и др.).
Основными
типами
дислокаций,
встречающихся
в
реальных
монокристаллах, являются краевая и винтовая дислокации.
Краевая дислокация представляет собой несовершенство решетки,
когда по одну сторону от плоскости скольжения количество атомных
плоскостей, перпендикулярных к плоскости скольжения, больше чем по
другую (рисунок 2.10). из рисунка видно, что выше плоскости скольжения
имеется добавочная плоскость а перпендикулярная плоскости скольжения.
Линию вг пересечения добавочной плоскости с плоскостью скольжения
называют линией дислокации.
Краевая дислокация считается положительной (обозначается ), если
дополнительная плоскость находится выше плоскости скольжения, и
отрицательной
расположена
(обозначается
ниже
Т),
плоскости
если
дополнительная
скольжения.
Наибольшее
плоскость
нарушение
правильности взаимного расположения атомов наблюдается вблизи линии
дислокации. Таким образом, вблизи дислокации возникает силовое поле с
повышенным уровнем потенциальной энергии.
Под действием касательных напряжений , действующих параллельно
плоскости
скольжения,
краевая
дислокация
способна
перемещаться.
Элементарный акт смещения краевой дислокации на одно межатомное
расстояние схематично показан на рисунке 2.11.
26
Рисунок 2.10 – Схема краевой дислокации
Перемещение краевой дислокации состоит в том, что дополнительной
плоскостью становятся поочередно плоскости параллельные плоскости ав (
рисунок 2.
). Штриховыми линиями на рисунке 2.
показано, как
первоначальная линия плоскость ав замыкается на расположенную ниже
плоскости скольжения плоскость вс, а лишней плоскостью становится
плоскость а1в1.
Пробег краевой дислокации от одной боковой поверхности кристалла
дает смещение верхней части кристалла относительно нижней.
Винтовую дислокацию схематически можно представить следующим
образом:
часть
кристаллической
решетки
разрезана
по
плоскости
скольжения, и разделенные участки смещены один относительно другого на
одно межатомное расстояние (рисунок 2.12).
В области винтовой дислокации кристаллографические плоскости,
перпендикулярных плоскости скольжения, получают изгиб.
27
Рисунок 2.11 – Схема перемещения краевой дислокации на одно межатомное
расстояние
Рисунок 2.12 – Схема винтовой дислокации
28
3. Кривые упрочнения
3.1.
В
процессах
обработки
Определение
металлов
давлением
под
действием
приложенных усилий заготовка деформируется, то есть изменяет свою
форму и размеры.
Если после снятия нагрузки форма и размеры тела восстанавливаются,
то такая деформация носит название упругой, если же нет – необратимой,
пластической.
Так например, в процессе растяжения цилиндрического стержня под
нагрузкой Р происходит изменение его размеров: увеличивается длина l на
величину l и уменьшается площадь поперечного сечения F на величину F
(рисунок 3.1).
Рисунок 3.1 - Изменение размеров образца в процессе его растяжения
li = li - l0 ; Fi = F0 - Fi
29
В процессе пластической деформации в каждый последующий момент
времени,
чтобы
продолжить
процесс,
приходится
прикладывать
возрастающее усилие.
Эффект повышения усилия (нагрузки) в процессе пластической
деформации носит название «упрочнение металла».
Если бы металл в процессе пластической деформации не упрочнялся,
то его деформация осуществлялась бы при постоянной нагрузке. Для
рассматриваемого
примера
- растяжения образца - диаграмма Рi-li
представлена на рисунке 3.2.
Рисунок 3.2 – Диаграмма Рi - li
при испытании на растяжение образца из неупрочняемого материала;
P1 = P2
Деформации, соответствующие точкам 1 и 2, достигаются при одной
из той же нагрузке Р. Металл не упрочняем.
Диаграмма Рi-li для упрочняемого металла имеет вид, приведенный
на рисунке 4.3.
Деформации, соответствующие точкам 1 и 2, требуют возрастающей
нагрузки: Р2 >P1. Материал упрочняем. Упрочнение металла в процессе
30
пластической деформации можно выразить и другими эффектами, например,
наклепом металла, то есть повышением его твердости рисунок 3.4.
Упрочнение, наклеп или повышение твердости металла – явления,
которые сопровождают холодную пластическую деформацию. Эти явления
связаны с природой – механизмом пластической деформации. По одной из
гипотез в основе пластической деформации - перемещение дислокаций. Их
«переползание»
через
«препятствия» для
продолжения
пластической
деформации требует увеличения нагрузки. По другой гипотезе пластическая
деформация связана со скольжением одной части кристалла относительно
другой. Это скольжение в первую очередь происходит по плоскостям,
наиболее благоприятно ориентированным к направлению нагрузки, то есть
по плоскостям, где возникают максимальные касательные напряжения.
Чтобы привести в скольжение другие плоскости, отличные от плоскостей с
max, нужно увеличить нагрузку.
Рисунок 3.3 – Диаграмма
Pi - li при испытании на растяжение образца из упрочняемого материала;
P2 >P1
31
Рисунок 3.4 – Повышение твердости HVi материала образца в
результате его пластической деформации
При пластической деформации одни зерна действуют на другие,
происходит их дробление. Изменение структуры металла при пластической
деформации (измельчение зерен, то есть получение мелкозернистой
структуры) приводит к повышению твердости металла, к так называемому
его наклѐпу. Для одних металлов упрочнение выражено в большой степени,
для других -незначительно.
Не упрочняются, например, металлы, деформируемые при Т>Трекр.
(горячая обработка металлов давлением).
При проектировании «холодных» процессов ОМД необходимо
учитывать упрочнение металла. Неучѐт упрочнения может привести к
ошибкам в расчетах, превышающим 30 % от истинных значений.
Цель настоящего пособия – дать студентам представление об явлении
«упрочнения» и его учѐту при расчѐте, проектировании и моделировании
процессов ОМД.
32
3.2. Индикаторная диаграмма
Исходным материалом, отражающим упрочнение металла, является
индикаторная или машинная диаграмма, получаемая при испытании
стандартных образцов на статическое растяжение (ГОСТ 1497-88).
Образцы закрепляют в губках испытательной машины и подвергают
растяжению. Специальный измерительный механизм испытательной машины
записывает машинную (индикаторную) диаграмму: усилие – удлинение (Рi li). На рисунке 3.5
в качестве примера приведена реальная диаграмма,
полученная на испытательной машине
Теstometric при растяжении
алюминиевого (АМг6М) образца с исходными размерами = 10 мм , l = 100
мм.
На индикаторной диаграмме (рисунок 3.6) можно выделить два
участка – упругий «oc» (в пределах которого действует закон Гука)
и
пластический «сde», сопровождающейся упрочнением металла. Точка d на
диаграмме соответствует Рmax
и разделяет пластическую область в свою
очередь на два участка: 1 dP>0 и 2-й (после m.d) dP<0.
Рисунок 3.5 – Индикаторная (машинная) диаграмма растяжения
цилиндрического образца
33
Рисунок 3.6 - Индикаторная диаграмма Pi - li. Участок ос – упругая
деформация; участок сde - пластическая; c d – равномерная;
de –
сосредоточенная деформации
На
первом
участке
все
сечения
(1-1;
2-2;
3-3…)
образца
деформируются одинаково (рисунок 3.7) – Это так называемая стадия
равномерной деформации. При дальнейшем растяжении (после m.d)
деформация сосредотачивается на узком участке, называемом шейкой
образца (рисунок 3.8 ). Все участки удалѐнные от шейки образца уже не
деформируются. Деформация сосредотачивается в шейке. Эта ветвь
диаграммы
(участок
de)
носит
название
деформации.
34
участок
сосредоточенной
Рисунок 3.7 - Растяжение образца - стадия равномерной деформации
F1-1 = F2-2 = F3-3 = F4-4
В области равномерной деформации, во всех сечениях существует
одноосное (линейное) напряженное состояние, в сосредоточенной –
объемное.
Резкое уменьшение площади поперечного сечения образца (шейка)
влечѐт за собой уменьшение потребного усилия (ниспадающая ветвь
индикаторной диаграммы). Материал продолжает упрочняться, но потребное
усилие для дальнейшей пластической деформации падает, из-за резкого
сокращения сечения образца.
В испытательных машинах нового поколения измерительная система
связана с ПК, позволяющем не только распечатать индикаторную диаграмму,
но и по стандартным программам провести еѐ дальнейшую обработку.
35
Рисунок 3.8 - Растяжение образца - стадия сосредоточенной
деформации
Сечения 1-1 4-4 – остаются не изменяемыми;
F5-5 > F1-1 F4-4
3.3.
Полученную
Диаграмма условных напряжений
индикаторную
диаграмму
можно
перестроить
в
диаграмму условных напряжений (рисунок 3.9), разделив текущие значения
усилия Pi на исходную площадь испытываемого образца: σусл = Pi/F0, а
величину текущего абсолютного удаления li на исходную длину образца l0,
получив,
таким
образом
величину
относительной
деформации
(относительное удлинение) - i = li/l0.
Вид диаграммы условных напряжений не меняется, меняется масштаб еѐ
записи по осям координат, так как деление текущих значений Pi и li
осуществляется на постоянные величины F0 и l0.
36
Таким образом, диаграмма условных напряжений имеет те же
характерные участки, что и индикаторная диаграмма – упругий и
пластический , равномерной и сосредоточенной пластических деформаций
(рисунок 3.9).
Рисунок 3.9 - Диаграмма условных напряжений усл - i: ос – участок
упругой деформации; cd – равномерной и dе – сосредоточенной
пластической деформации
Термин «условных» напряжений связан с тем, что в процессе
испытания и F, и l меняются. Мы же условно принимаем их неизменными,
равными исходным значениям F0 и l0.
Кроме того, термин «диаграмма условных напряжений» подчеркивает
главенствующую роль именно напряжений, а не деформаций, подразумевая
под этим, что по оси абсцисс деформации могут быть выражены по разному:
относительное удлинение , относительное сужение (=F/F0) и истинная
(логарифмическая) деформация (e = ln(lk/l0) ). Между деформационными
характеристиками , и e, существует связь, вытекающая из закона
постоянства объема, например i = i (1-i).
37
Истинная деформация – это сумма бесконечно малых относительных
деформаций
После преобразования
также
получим
связь
e ln 1 . Следовательно, все три
деформационных характеристики связаны между собой.
В зависимости от cпособа оценки деформации
, , е различают
диаграммы условных напряжений первого, второго рода и третьего рода
соответственно.
Используя связь между деформациями, имея одну диаграмму, всегда
можно перестроить еѐ в других координатах.
Для различных марок материала вид диаграмм условных напряжений
меняется. Различают четыре их характерных вида со следующими
особенностями (рисунок 3.10):
1) – наличие площадки текучести (малоуглеродистые стали);
2) – отсутствие площадки текучести и четко выраженная m.d(Pmax),
наличие обеих участков равномерной и сосредоточенной деформаций
(алюминиевые сплавы);
3) – размытый максимум (Pmax) и большая область сосредоточенной
деформации (титановые сплавы);
4) – отсутствие сосредоточенной деформации (литейные сплавы).
38
1)
2)
3)
4)
Рисунок 3.10 - Виды диаграмм условных напряжений для образцов из
различных марок сплава
Диаграммы условных напряжений позволяют определить условные
константы механических свойств: условный предел текучести и условный
предел прочности.
Условный предел текучести – условное напряжение, при превышении
которого начинается пластическая деформация, когда в образце реализуется
линейная схема напряженного состояния. Этой характеристике соответствует
точка на диаграмме условных напряжений перехода из упругой области в
пластическую (т. С). Понятие
«начинается» - качественное понятие.
Количественное значение остаточной деформации для этой точки должно
составлять 0,2 % от первоначальной длины l0. Вот почему условный предел
текучести для всех диаграмм условных напряжений не имеющих площадки
39
текучести обозначается 0,2. Чтобы отличать условный предел текучести для
диаграмм с площадкой текучести ему дали термин «физический предел
текучести» и ввели обозначения s или T ,то есть это также условное
напряжение, но соответствующее площадке текучести
Условный предел прочности – условное напряжение при превышении,
которого начинается разрушение образца.
напряжений
условному
пределу
прочности
На диаграмме условных
соответствует
точка
d,
обозначается в и равен Pmax/F0.
Рисунок 3.11 - Составляющие деформационного процесса растяжения
образца
40
Под разрушением образца понимают начало процесса образования
шейки, а не фактическое разделение образца на две части (точка e).
Диаграмма условных напряжений позволяет продемонстрировать
(наглядно показать) все составляющие деформационного процесса (рисунок
3.11).
Для точки 1 – деформация под нагрузкой соответствует отрезку 01,
после снятия нагрузки (разгрузка осуществляется по линии параллельной
линии упругой деформации (закону Гука), мы возвращаемся в т. 0, то есть
остаточная деформация отсутствует.
Для точки 2 – деформация под нагрузкой соответствует отрезку «02».
После снятия нагрузки (разгрузка осуществляется вдоль линии параллельной
линии, соответствующей упругой деформации 0с), получим остаточную
деформацию, соответствующую отрезку 0h, причем эта деформация будет
равномерной.
Для точки 3 – деформация под нагрузкой соответствует отрезку «03».
После снятия нагрузки получим остаточную деформацию, соответствующую
отрезку «03, причем т. «dn» делит эту деформацию на равномерную «0d» и
сосредоточенную «dn».
Аналогично определяются все деформационные составляющие на
диаграмме условных напряжений II рода.
3.4.
Диаграмма истинных напряжений
Индикаторную диаграмму можно перестроить и в диаграмму
истинных напряжений, если текущие значения нагрузки Pi относить не к
исходной площади образца F0, а к его текущей площади Fi.в данный момент
времени
Истинные напряжение в этом случае обозначим как i. Итак, i = Pi/Fi.
Диаграммы истинных напряжений могут быть построены в координатах i
41
=f(i); i = f(i) и i = f (еi). то есть диаграммы истинных напряжений также
могут быть 1-го, 2-го и 3 рода. Диаграмма истинных напряжений по
внешнему виду отличается от диаграммы условных напряжений. Во первых,
так как Fi
Тебе могут подойти лекции
Включи камеру на своем телефоне и наведи на Qr-код.
Кампус Хаб бот откроется на устройстве
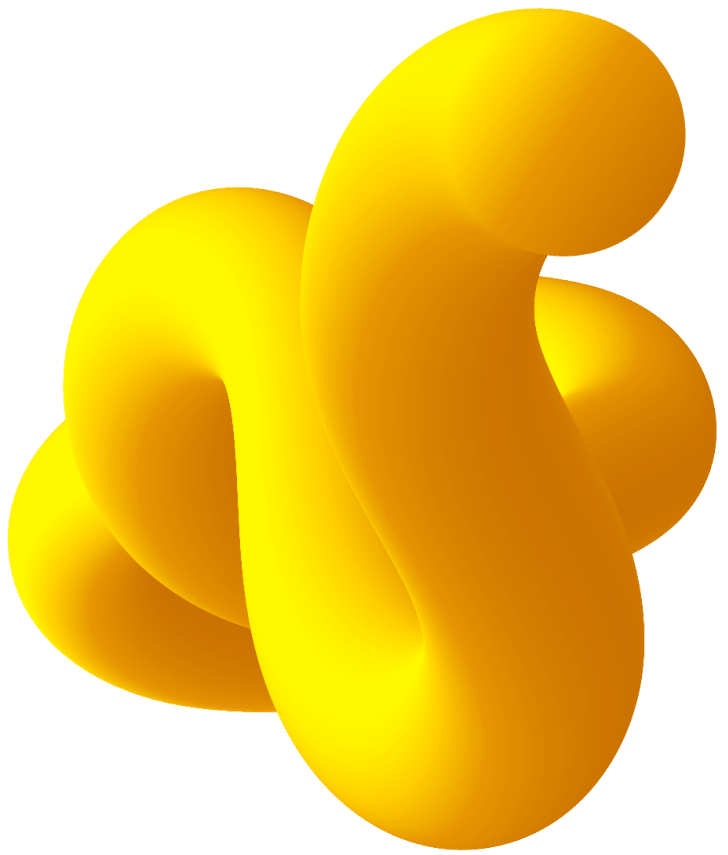
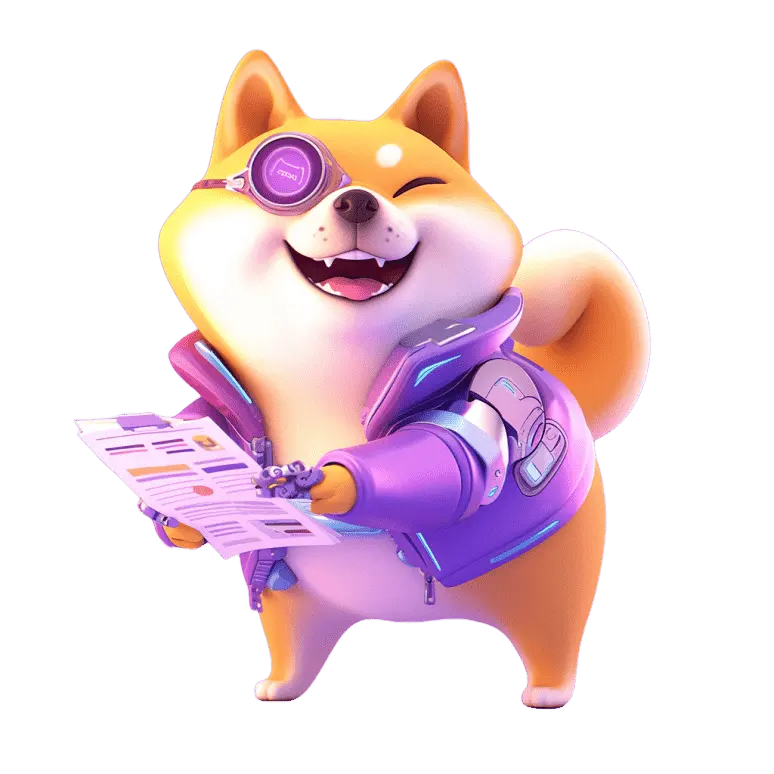
Не ищи – спроси
у ChatGPT!
у ChatGPT!
Боты в Telegram ответят на учебные вопросы, решат задачу или найдут литературу
Попробовать в Telegram

Оставляя свои контактные данные и нажимая «Попробовать в Telegram», я соглашаюсь пройти процедуру
регистрации на Платформе, принимаю условия
Пользовательского соглашения
и
Политики конфиденциальности
в целях заключения соглашения.
Пишешь реферат?
Попробуй нейросеть, напиши уникальный реферат
с реальными источниками за 5 минут
с реальными источниками за 5 минут
Теория обработки металлов давлением

Хочу потратить еще 2 дня на работу и мне нужен только скопированный текст,
пришлите в ТГ